Implementing digital transformation processes within the manufacturing industry has been an ongoing process for approximately three decades. First, manufacturers utilized digitization to collect data for storage purposes before moving on to more complex applications. Optimizing industrial design became the next logical step for applying digital transformation technologies. However, it would take the introduction of Industry 4.0 business models in 2011 for manufacturers to apply digitization to improving operational processes.
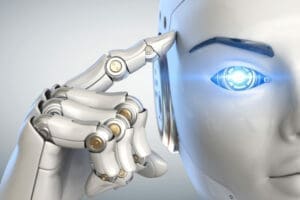
Logically, it is only right to kick-start any discussion about digitalization with the application of virtual models. Computer-aided design (CAD) platforms provided manufacturers with the first digitalization tool for designing products and validating their functionalities. 3D Modeling empowered manufacturers with an intuitive object-oriented tool for designing models with diverse levels of complexities.
For one, modeling tools such as Autodesk’s Revit is used to design products with complex geometries, model manufacturing environments, and to prep digital models for manufacturing using either subtractive or additive manufacturing technologies. Editing models of physical objects is possible but that was the limit one could get with CAD.
The Digital Twin
Improving on the digitalization capabilities of CAD, the digital twin was developed to run in parallel and interact with real-world physical manufacturing systems. First, digital twins are digital representations of physical systems that receive real-time data from the data-producing assets within the shop floor forming a cyber-physical system.
Ongoing interexchange of data empowers users of the digital twin with a virtualized option to view functions within a facility. Consequently, the virtual environment it provides serves as an accurate validation platform for evaluating complex manufacturing problems. Utilizing the digital twin as a remote monitoring tool, condition monitoring, and a testing and validation tool are some of the use cases for the digital twin.
Within the cyber-physical system of a functional digital twin, data exchange is a two-way process. Data from the factory floor is sent to the digital twin and it can also send data to systems on the factory floor to initiate specific actions. For example, an Oil and Gas service provider interested in determining its capacity expansion needs utilized a digital twin to determine its capacity expansion requirements.
Determining the capacity requirements started with the development of a digital twin of the facilities current operational processes. The digital twin enabled the enterprise to analyze the effects of increased demand on the facility’s servicing capacity. Diverse terminal flow configurations were also evaluated and the result was an optimized service level which improved patient satisfaction levels.
The Digital Shadow
Confusing the digital shadow with digital twins is a normal feature in the industrial sector. Firstly, both utilize data of physical objects to rebuild digital representations and secondly, they can create representations of objects and processes. That’s where the similarities end.
Generally, digital shadows rely on scanned laser data to capture as-built objects. More importantly, data flow is a one-way process. Data flows from the physical entity to the digital shadow but not the other way around. Digital shadows can also be created of digital twins because they can capture and simplify the plethora of information passing through a twin at specific periods.
Using the example of the Oil and Gas enterprise above, when providing stakeholders with presentations on the application of the designed digital twin a digital shadow can be used. Semantically adequate and context-aware data from the digital twin’s application is what the shadow provides to non-technical decision-makers.
The Role of Digital Models, the Digital Twin, and Digital Shadows in Manufacturing
Manufacturing industrial niches utilize these digitalized concepts in several ways. Digital models are great for industrial design and developing ideas, digital shadows are useful in tracking production, while the digital twin supports the evaluation of real-time manufacturing processes.
Utilizing a platform with the capabilities to provide all three empowers manufacturers with a powerful digital transformation tool for data-driven analysis. Intelligent object-based digital twin platforms incorporate the use of 3D models to create accurate digital twins which support the capture of digital shadows. Fully developed digital twins become a hub for continuously analyzing manufacturing processes, remote monitoring, and a decision-making tool.
Conclusion
The digital twin connects the entire manufacturing process alongside digital models and shadows. These digitalization concepts can be applied together to optimize production processes and monitor each aspect of the manufacturing cycle.