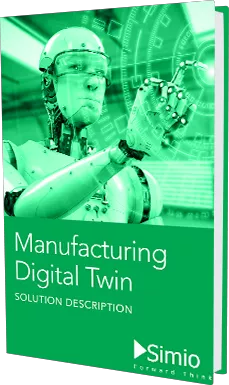
Manufacturing Digital Twin
By Gerrit Zaayman
The application of a digital twin to optimize industrial operations, processes, and systems is increasingly being used by business enterprises in the industrial sector. The digital twin is a virtual representation of real-world industrial systems. It is a connected ecosystem where real-time data transfers from physical processes are monitored, analyzed, and evaluated to improve industrial processes. The digital twin enhances industry 4.0 applications through its ability to provide decision-makers with instant remote access to plant floor operations.
Simio Manufacturing Digital Twin is one of the first books that seeks to provide students, educators, and the business community with a comprehensive insight into the Digital Twin, how to create one, and apply it to optimize specified industrial processes.
Get it Now
Description
Imagine a production system where all production decisions are optimized based on real time information from a fully integrated and connected set of equipment and people. The entire system makes the best possible use of the available resources to achieve its production goals, and the system automatically adjusts in real time to changing conditions. All work is automatically scheduled through the system, all equipment automatically records its performance and also plans and schedules its own maintenance to minimize impact on the system. Performance data is automatically recorded throughout the system and reported to the appropriate stakeholders. In addition, the system predicts forward in time and provides reliable management information on planned performance including critical KPIs such as expected delivery time and production costs for all planned orders. Managers have instant access to important current and forward-looking information to drive and grow the business. This is the vision of the Smart Factory of the future (4th Industrial Revolution).
The Smart Factory is an idea whose time has come. The technologies underpinning the Smart Factory have continued to evolve and become more mainstream. Each component is familiar technology and is in place in many factories today. However, the detailed factory model or Factory Digital Twin that provides forward visibility into the planned operations, supporting ongoing continuous improvement initiatives has been the critical missing component in enabling the Smart Factory. The Simio Factory Digital Twin provides this critical component.
About The Authors
Gerrit Zaayman completed his Bachelor’s degree in Electronic Engineering. He then went on to specialize in process and workflow simulation and completed advanced courses in process simulation, business process reengineering and artificial intelligence. As part of this process he helped to establishing the leading process, supply chain and workflow simulation business in South Africa providing the Siman and later the Arena simulation systems to the market. He then joined i2 Technologies where he later became the country manager for South Africa. There he was responsible for sales and delivery of i2’s leading supply chain planning and optimization software to large enterprises gaining experience in planning and optimisation from the strategic design level down to detail scheduling. Gerrit also spent time at Softeon, a provider of warehouse management and optimization systems, as director of sales and marketing where he gained valuable experience in the planning and optimization of warehouse operations. Most recently, Gerrit spent three years as Director scheduling solutions at Simio LLC.