Em uma cadeia de suprimentos centrada na manufatura, o fornecimento da fábrica é uma decisão crítica que impulsiona o rendimento e a entrega no prazo. Se mais de um local estiver disponível para produzir um produto, é importante equilibrar a carga entre os locais de produção dentro da cadeia de suprimentos para garantir que a capacidade disponível seja utilizada de forma otimizada para que você consiga fazer a entrega no prazo. Essa decisão de sourcing normalmente é feita com o uso do software MPS (Master Production Scheduling) para atribuir cada trabalho de produção a um intervalo de tempo (por exemplo, semanalmente) em um local específico. O resultado do MPS é uma lista de trabalhos a serem produzidos durante cada intervalo de tempo em cada local de produção. A ferramenta de programação detalhada da produção obtém o resultado do MPS e gera uma programação detalhada dentro do intervalo de tempo atual para um local específico.
Uso da abordagem de planejamento de capacidade de corte grosseiro
O MPS pressupõe um lead time de produção fixo e usa uma abordagem de planejamento de capacidade aproximada (RCCP) com base em uma medida de capacidade simples (por exemplo, total de horas de trabalho atribuído por intervalo de tempo) para selecionar o intervalo de tempo apropriado e limitar o trabalho atribuído a cada intervalo de tempo em cada local de produção, utilizando locais secundários conforme necessário para evitar a sobrecarga do local de produção preferencial. Entretanto, em sua abordagem RCCP e medição simplificada da capacidade disponível, o MPS ignora muitas restrições importantes de capacidade, como trocas, ferramentas, mão de obra, manuseio de materiais e regras de produção. Em seguida, o MPS emprega um solucionador heurístico (por exemplo, CPLEX) que, normalmente, leva horas para ser executado na busca de uma boa solução viável para essa representação simplificada do sistema. Embora os sistemas legados apresentem sua solução como ideal, o solucionador heurístico normalmente não encontra a solução ideal, mas simplesmente a melhor solução que pode ser encontrada pelo algoritmo de busca durante o tempo alocado para resolver o problema (normalmente algumas horas). Além disso, sua aproximação grosseira da capacidade e do tempo produz resultados que normalmente não são acionáveis no sistema real e, como resultado, são desalinhados com a programação de produção real, que deve considerar todas as restrições relevantes. Esse desalinhamento entre o plano mestre e as programações detalhadas da fábrica é ilustrado abaixo e é uma das principais causas do baixo desempenho na cadeia de suprimentos.
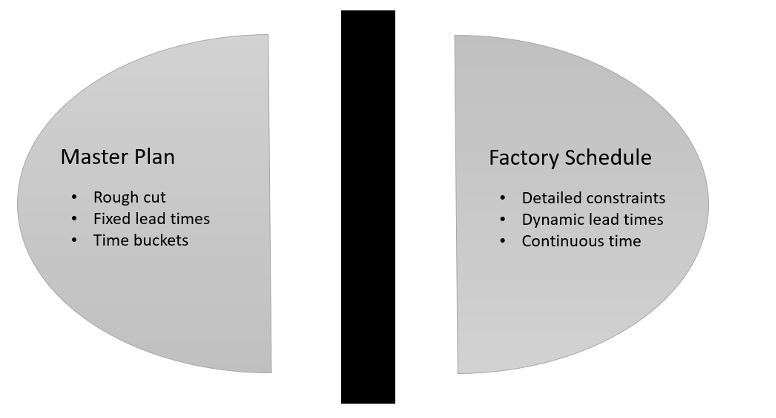
O problema com um sistema MPS desalinhado
Esse desalinhamento cria inconsistências em toda a cadeia de suprimentos e pode fazer com que os materiais errados sejam planejados, comprados e transportados para cada local. Em muitos casos, o MPS envia mais trabalho e materiais associados a um local de produção do que pode ser produzido dentro do intervalo de tempo, dadas as restrições reais de produção no local de produção.
Conforme ilustrado abaixo, mesmo quando o MPS gera uma lista viável de ordens de produção, o uso de intervalos de tempo artificiais rouba a capacidade do sistema, uma vez que a produção para o conjunto de ordens atribuídas deve aumentar e diminuir no final de cada intervalo de tempo para concluir todo o trabalho atribuído dentro do intervalo de tempo. Para evitar a perda dessa capacidade, a programação da fábrica às vezes é aumentada com ordens de serviço ad hoc não planejadas, que não fazem parte do plano mestre da cadeia de suprimentos. Esses pedidos ad hoc normalmente não estão alinhados com a demanda do cliente, o que incha o estoque com os produtos errados.
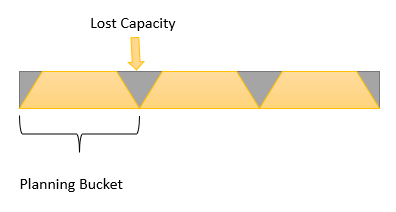
Aprimorando o modelo com uma simulação detalhada
Em contrapartida, a plataforma de soluções da Simio para a cadeia de suprimentos de várias fábricas captura todas as restrições críticas em cada local de estoque e produção ao longo de um horizonte de tempo real e produz um plano consistente, otimizado e acionável em toda a cadeia de suprimentos. Essa solução combina modelos de simulação detalhados de cada local para capturar com precisão o estado evolutivo do sistema, a lógica de reabastecimento DDMRP para gerar ordens de reabastecimento e redes neurais para estimar dinamicamente os tempos de produção em cada local de produção, que são usados para otimizar a atribuição de ordens de produção aos locais. Esse uso sinérgico do DDMRP para planejar quando o reabastecimento deve ocorrer e das redes neurais (NNs) para otimizar a seleção entre os locais de produção candidatos elimina a necessidade do módulo de software MPS separado e de longa duração para pré-atribuir o trabalho a intervalos de tempo artificiais nos locais e permite que a produção seja planejada ao longo de um período de tempo contínuo.
Conforme observado acima, o DDMRP é usado no modelo da cadeia de suprimentos para gerar ordens de reabastecimento, que, por sua vez, podem gerar ordens de produção. Quando há mais de um local candidato que pode fornecer a ordem de reabastecimento, é necessária uma decisão de sourcing. Se o local preferido sempre tiver quantidades adequadas de estoque em buffer, o lead time desacoplado (DLT) usado para dimensionar os buffers do DDMRP garante que o reabastecimento do local preferido ocorrerá a tempo de evitar pedidos atrasados. No entanto, a variação na demanda pode, às vezes, fazer com que o estoque no local de reabastecimento preferencial fique baixo ou fora de estoque, e o congestionamento em um local de produção preferencial pode causar um lead time maior do que o planejado para atender a um pedido de reabastecimento, criando, assim, pedidos atrasados. Nesse caso, é preciso considerar locais de reabastecimento alternativos para equilibrar a carga de produção entre os locais.
Como os fatores de lead time restrito são incluídos no modelo
Cada local candidato tem um lead time restrito (CLT) que é diferente do DLT usado para o planejamento do DDMRP. O CLT é o lead time com base nas restrições reais do sistema, considerando o estado atual do local. O CLT é afetado pelos níveis de estoque, mix de produtos e trocas, mão de obra, ferramentas, etc. Ao contrário do DLT, o CLT muda dinamicamente à medida que novos pedidos chegam ao local e a produção prossegue. Por exemplo, se um local de produção estiver sem estoque e tiver muito trabalho em processo com um alto mix de produtos que exija trocas demoradas, o CLT para um novo pedido poderá ser significativamente mais longo do que o DLT usado para o planejamento do DDMRP. Nesse caso, pode ser desejável um fornecedor alternativo com um CLT menor.
O CLT de um local candidato depende do nível atual de estoque, do tempo de chegada esperado de quaisquer pedidos de reabastecimento que já estejam em andamento e do tempo de reabastecimento esperado, caso um novo reabastecimento precise ser concluído antes que o pedido possa ser preenchido. Se um novo reabastecimento vier da produção, o tempo de reabastecimento será o tempo de produção esperado, considerando o estado atual do local de produção. Se o reabastecimento vier de um fornecedor, o CLT será o CLT do fornecedor selecionado, que pode retornar à cadeia de suprimentos e, por fim, atingir um local de produção.
O único componente difícil para calcular o CLT é estimar o lead time de produção em um local de produção com base no estado atual do local. No entanto, os recursos de rede neural do Simio oferecem uma solução ideal para esse problema. A decisão de sourcing pode ser otimizada com base no CLT previsto para cada local candidato, em que é selecionado o local de menor custo que pode entregar no prazo.
Os efeitos do envolvimento de IA e de terceiros
Embora a IA tenha se mostrado altamente eficaz na solução de problemas difíceis de regressão, um dos principais desafios da IA é ter os dados de treinamento rotulados necessários para treinar o algoritmo. Muitos aplicativos de IA falham devido à falta de dados de treinamento bons e rotulados. Os dados de treinamento rotulados nunca estão disponíveis ao avaliar um novo sistema e, mesmo em casos com instalações existentes, todos os dados históricos tornam-se inválidos quando uma nova peça ou alteração no fluxo é introduzida no sistema. No entanto, os recursos integrados do Simio para coletar e rotular automaticamente os dados de treinamento sintéticos resolvem esse problema. O gêmeo digital do processo da cadeia de suprimentos pode gerar automaticamente todos os dados necessários para treinar as redes neurais a fim de prever com precisão o tempo de produção, considerando o estado atual do local.
Os recursos de IA integrados do Simio oferecem suporte para a definição, o treinamento e o uso da rede neural de regressão de avanço clássico. No entanto, conforme ilustrado abaixo, você não está limitado a esse algoritmo de aprendizado de máquina, pois também pode importar e usar no Simio qualquer modelo de regressão de aprendizado de máquina de mais de 50 terceiros, incluindo Google e Microsoft, que suportam o formato de troca de modelo ONNX. Você pode criar e treinar modelos em ferramentas de terceiros e, em seguida, importá-los para o Simio para tomar decisões complexas dentro do seu modelo. Você também pode exportar para o formato de arquivo ONNX. Você também pode usar os modelos do Simio para gerar dados de treinamento sintéticos rotulados para exportação e uso por ferramentas de terceiros.
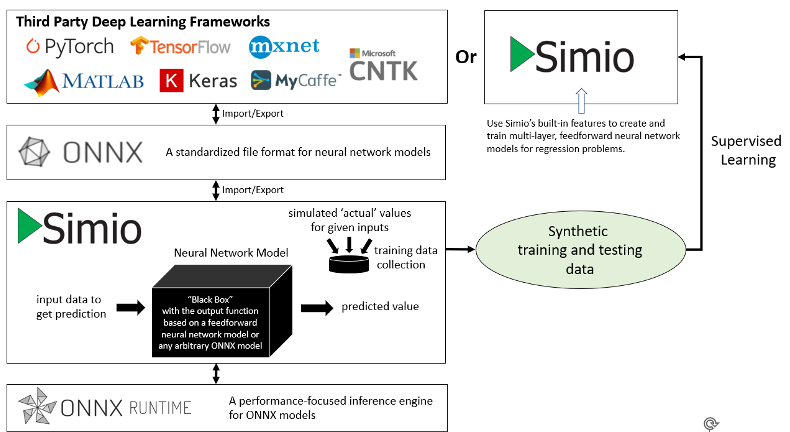
Cumprimento de metas com um gêmeo digital orientado por IA
Os benefícios da Simio Solution Platform para a programação de várias fábricas começam com seu modelo de capacidade preciso, horizonte de tempo contínuo, otimização baseada em IA do sourcing da fábrica e execução rápida para gerar programações acionáveis que estão alinhadas em toda a cadeia de suprimentos. Mas os benefícios culminam na capacidade da Simio Solution Platform de comunicar sua estrutura, sua lógica de modelo e as programações de produção resultantes a todos que precisam saber. O Simio oferece mais insights operacionais em relação às saídas MPS estáticas tradicionais por meio de animação 3D interativa da programação, permitindo que os usuários visualizem um fluxo de trabalho planejado. A animação detalhada mostra o movimento de peças, trabalhadores, dispositivos de manuseio de materiais e outras restrições críticas à medida que o cronograma planejado se desenvolve. O Simio também registra dados transacionais detalhados de todas as ações de restrição em logs de programação que podem ser visualizados, filtrados e usados para gerar relatórios e painéis personalizados que podem ser compartilhados em toda a empresa usando o Portal Simio. Os dados desses registros incluem informações sobre materiais, recursos, pedidos e equipamentos de manuseio de materiais, bem como o tempo sem valor agregado gasto pelos pedidos restringidos pelo sistema. Essas informações são valiosas não apenas para avaliar a qualidade do cronograma, mas também para aprimorá-lo, fornecendo informações sobre a causa raiz dos atrasos no cronograma.
As tecnologias DDMRP, IA e Process Digital Twin que sustentam a Simio Solution Platform para programação de várias fábricas evoluíram e estão se tornando comuns. Você pode encontrar mais informações sobre a Simio Solution Platform neste white paper: Como os objetos Simio se diferenciam de outras ferramentas de modelagem orientadas a objetos. Para obter mais informações sobre os recursos DDMRP do Simio, consulte este white paper: Demand Driven Material Requirements Planning Powered by Simio. Chegou a hora de substituir seu MPS legado por um gêmeo digital da cadeia de suprimentos orientado por IA.