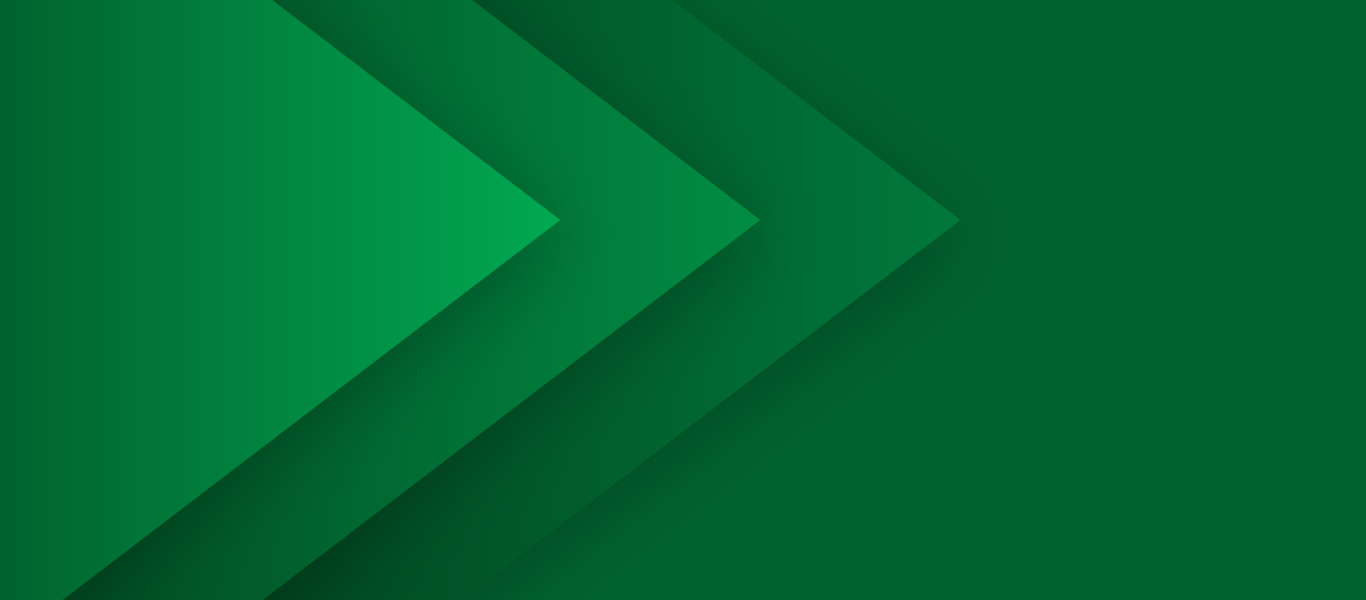
The Simio Process Digital Twin
A true digital twin that accurately replicates your operations to design, analyze, and optimize, as well as predict and prescribe both current and future performance
What is a Digital Twin?
The term “Digital Twin” has gained popularity and become a catchall phrase for various digital models. However, the true value of a Digital Twin lies in its ability to accurately represent the full details of real-world operational processes, behavior, and performance, while fully leveraging enterprise data and seamlessly integrating with operational systems. Although many applications promote Digital Twin capabilities, significant challenges often arise during implementation—particularly in adapting to changes within the process during operation. This critical failure often undermines the viability of many solutions.
Simio has developed an agile platform specifically designed to meet the demands of creating Intelligent Adaptive Process Digital Twin models that precisely replicate the real-world behavior of operational processes and integrate seamlessly with enterprise data and systems. Built on our industry-leading Discrete Event Simulation technology, the Simio platform is engineered to support Industry 4.0 digital transformation journeys. From a robust environment for designing, experimenting, analyzing, and optimizing simulation models to enhance operational efficiency and decision support, to the deployment of tightly integrated Intelligent Adaptive Process Digital Twins that enable fully autonomous lights-out operations, Simio equips and guides users through a seamless journey across the entire design-to-operate continuum.
Intelligent
Combining Discrete Event Simulation and AI creates a powerful synergy, resulting in Simio Process Digital Twins with unparalleled intelligence, capable of generating highly optimized solutions to complex operational problems with lightning-fast efficiency.
Adaptive
Simio Process Digital Twins have the ability to automatically adapt to changes in enterprise data such as process-related resources, materials, properties and attributes, product routings, network changes, bill of materials, labor requirements and schedules, maintenance schedules, and product mix.
Process
Business processes across a wide range of industries can be modeled with a Simio Process Digital Twin, including detailed manufacturing operations within single facilities and across multiple sites, warehouse operations, and complex end-to-end supply chains.
Digital Twin
Simio Process Digital Twins are object-oriented, data-generated, and data-driven Discrete Event Simulation models that accurately replicate the physical behavior of operational processes for systems of any size and complexity. Simio Process Digital Twins enable users to design, optimize, predict, and prescribe current and future system performance.
Why Develop a Simio Process Digital Twin?
Simio’s agile platform for developing Intelligent Adaptive Process Digital Twins supports a wide range of workstreams within a digital transformation process. Independent of the workstream selected, successful Process Digital Twin development — whether modeling current or future operational processes — requires the identification, design, analysis, support for the execution of operations. Four key reasons stand out for using Simio’s platform in both the design and analysis phases and the operational planning and scheduling phases of your business transformation. Each of these use cases adds distinct value to your business throughout the various development and deployment phases of your transformation project.
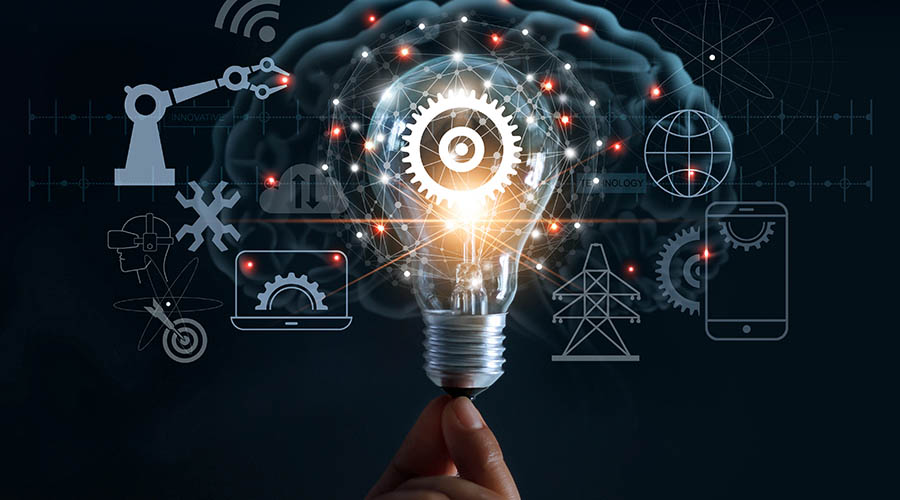
Key Reason #1
Knowledge Base
Develop a centralized, single-point-of-reference knowledge base by capturing all system constraints, business rules, and detailed logic in a comprehensive Discrete Event Simulation model of the process. This ensures the accurate replication of complex, mission-critical operations at a single site or across large multi-site systems.
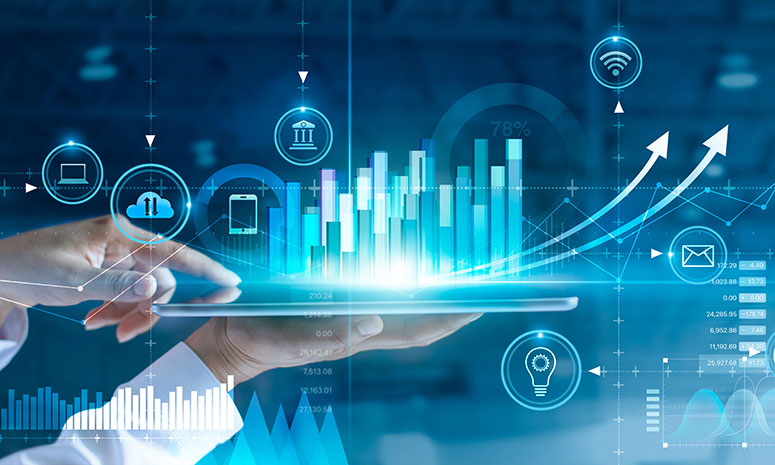
Key Reason #2
Performance Benchmarking
Establish a process performance benchmark to assess current performance and accurately predict future performance for the factory and supply chain. This enables the validation of changes such as automation, new equipment, and replenishment policies like Demand Driven Material Requirements Planning (DDMRP).
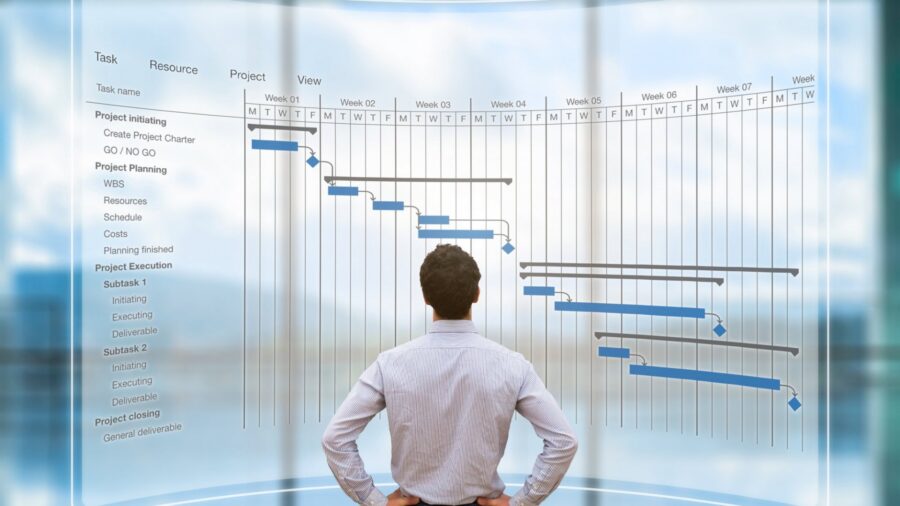
Key Reason #3
Plan & Schedule
Create feasible plans and schedules for shop floor, warehouse, factory, and supply chain execution across all relevant time ranges by ensuring that operations are resource capacity, material, and timeline feasible. This enables fully autonomous execution.
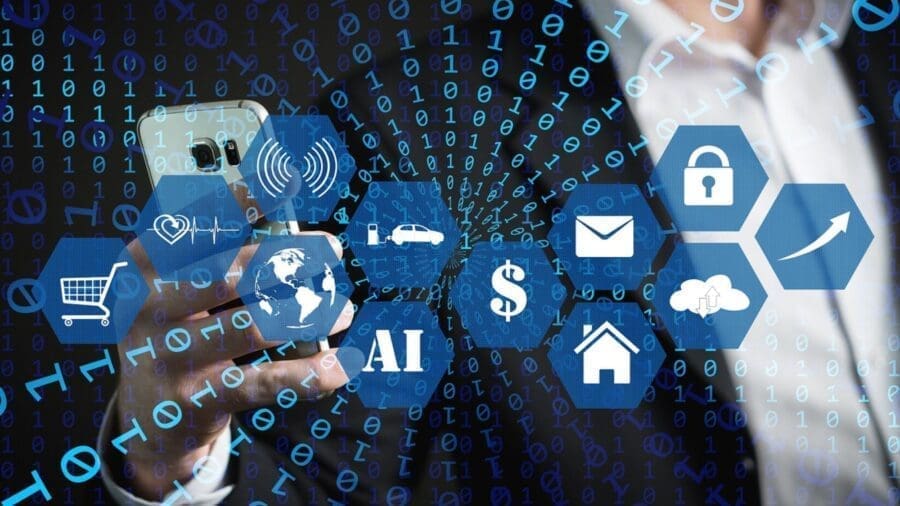
Key Reason #4
Reference Model
Maintain an adaptive, data-generated, and data-driven Intelligent Adaptive Process Digital Twin to ensure a “current status” digital reference model of the process. This enables the determination of future factory and supply chain performance for ongoing and new transformation projects and investment decisions.
Operational Value of a Simio Process Digital Twin
Evaluate Alternatives & Analyze the Impact of Ongoing Changes
- Operational policies or process changes
- New product or material introductions
- Adding production capacity or automation such as new equipment, tooling, robotics, and AMRs
- Adjusting worker skill requirements, shift patterns, and staffing levels
- Redesigning plant layouts and reorganizing sequences of operations
- Material availability and inventory policies, including JIT, Kanban, and DDMRP
Create Actionable and Feasible Plans and Schedules
- Increase throughput and on-time delivery by synchronizing production across the entire process
- Reduce production costs, including material, labor, penalties, energy, and work-in-progress expenses
- Improve production schedule adherence, order fulfillment rate, and service levels
- Streamline operations and improve efficiency through autonomous operations supported by near-real time scheduling and orchestration
- Achieve optimized plans & schedules by training, testing, and deploying AI
Integrated Data and Workflow Management Features
- Multi-user browser-based access with customizable permissions, roles, traits, and location
- Dynamic integration via data connectors, including Web APIs
- Generated and driven with direct integration or cloud-based enterprise data pipelines
- Interface with supporting applications such as MES, ML/AI/NN, Tableau, and Power BI
- Control and distribute model results across teams in a structured manner
Key Components of a Simio Process Digital Twin
Data-Generated & Driven
Models are generated and driven by enterprise data, including resources, material master, BOMs, routings, and current status. This enables the identification and validation of key aspects of the enterprise data, such as granularity, quality, correlation, speed, and availability.
Intelligent Objects
Models are built from smart objects that represent system components such as machines, transporters, robots, and workers, all of which can influence each other and incorporate AI/NN/ML to augment process optimization.
Constraint Models
Constraint models encompass all physical constraints (e.g., equipment, workers, transport, material), business rules (e.g., MOQ, labor policies, inventory policies), and detailed decision logic (including ‘tribal knowledge’ from the shop floor) to ensure the model accurately replicates the behavior of the physical process.
Event-Driven
Discrete Event-Driven Simulation technology simulates forward in time using the event calendar to synchronize all future tasks and material decisions on the execution timeline. This ensures schedule feasibility on the shop floor for operator-driven execution or even direct orchestration in highly automated environments.
Stochastic
Simio Process Digital Twin models incorporate randomness, which is crucial for evaluating variability such as machine breakdowns and late material arrivals. This capability enables plan and schedule risk assessment to support proactive actions and increase the probability of achieving performance targets like on-time delivery.
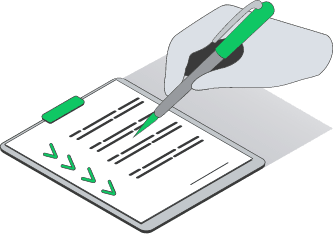
Templates
Simio provides a library of application-specific templates containing predefined objects, process logic, and data schemas to jump-start Process Digital Twin model development for complex operational processes. Each template is customizable to fit any user-specific requirements.
Creating a Simio Process Digital Twin
The development of a Process Digital Twin model involves five key stages: beginning with documenting all process steps, progressing through simulation model creation, and culminating in the integration of the Process Digital Twin model with live enterprise systems and relevant data sources.