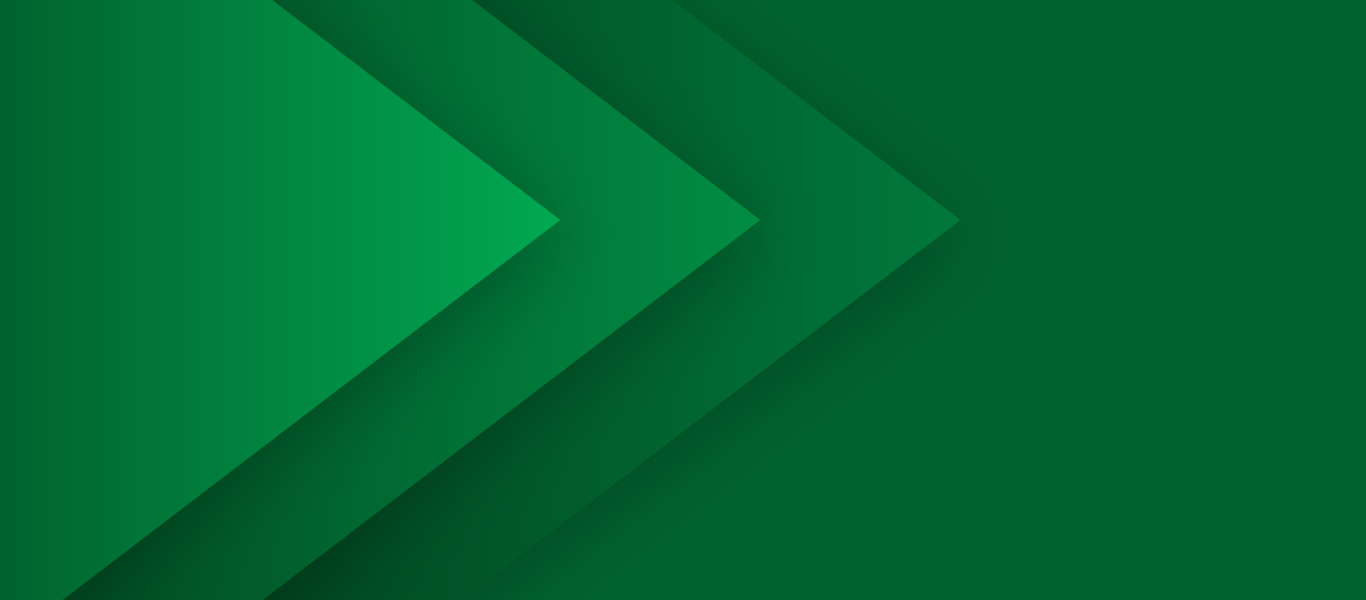
Simio Process Digital Twin Applications
Envision, design, and analyze your business transformation process — then operate, manage, and continuously improve to maintain your competitive advantage
Business Transformation Challenges
Drawing on years of experience in simulation and analysis, we at Simio have discovered that the most effective way to drive business and digital transformation, as well as address the challenges outlined below, is through the creation and use of a Discrete Event Simulation-based Intelligent Adaptive Process Digital Twin model. This model can be deployed in various steps according to use cases, overall business goals, and transformation requirements. Depending on an organization’s process and digital maturity and its business transformation goals, deployment may occur in phases, beginning with a virtual or offline Process Digital Twin. In this initial phase, the offline model serves as a predictive tool for designing and analyzing current and future processes. By integrating real-time data from enterprise systems, the offline model can evolve into a fully-fledged Intelligent Adaptive Process Digital Twin, operating online and deployed on the cloud, enabling operational deployment and near-real-time for both predictive and prescriptive decision-making. The information below explores the details of transformation and the benefits of leveraging an Intelligent Adaptive Process Digital Twin to achieve transformation objectives.
Understanding Current Processes & Constraints
Understanding begins with identifying all physical constraints in the process of sourcing materials, as well as producing and distributing products to customers. Additionally, numerous documents describe the business rules management wants to apply to govern the process, which often contradict the current reality. In most organizations, much of the execution know-how and detailed decision logic remains tribal knowledge, making it difficult to replicate in other systems, as it resides in the minds of those making day-to-day decisions on the shop floor.
Identifying the Best Data Sources & Aggregating Accurate & Relevant Data
Understanding the current quality and correlation of data between various enterprise systems is a significant challenge, as values for identical fields frequently vary across different systems, making it difficult to ascertain accuracy. The level of detail and recording frequency vary between systems based on their application, complicating data correlation and aggregation further. Identifying the sources and flow of data to establish a relevant data pipeline to support process modeling, control, dashboarding, and analysis is key to the transformation process.
Identifying & Exploring Areas for Transformation & Modernization
It is difficult to accurately identify and determine the value that certain process changes and optimizations can deliver to increase performance in the factory or supply chain. Certain performance or value gains are often perceived, leading to large capital investments in capacity and extensions to physical infrastructure for future growth and new products, without a detailed understanding of the requirements and potential impact on the business. Transformation projects are often developed in isolation, resulting in a shortfall in delivering the overall expected value and the anticipated process transformation required to advance the business towards achieving its digital transformation goals.
Accurately Predicting Future Behavior & Performance
Transformation typically involves many concurrent aspects of a business, such as personnel, processes, equipment, new products, sales, global reach, distribution, and more. Without understanding the end-to-end impact of proposed changes in business operations, including policies and processes, there is a risk of falling short of expectations and potentially wasting money on investments that do not deliver the expected value. This includes understanding the impact of automation (robotics, AMRs, material handling, etc.), evaluating alternatives to understand the ROI of various options, and visualizing and presenting future results to all stakeholders for buy-in and decision-making.
Facilitating Business Transformation
At Simio, we have leveraged our Discrete Event Simulation expertise to create an agile platform for developing Intelligent Adaptive Process Digital Twins, designed to facilitate comprehensive digital transformation and process re-engineering initiatives. The Process Digital Twin simulates into the future, offering predictive and prescriptive analyses of the system and providing a forward-looking view of expected performance of the process. This enables businesses to understand and adjust constraints, rules, and decision logic, finding better ways to run the process and fostering continuous learning and improvement. As part of the overall digital transformation process, the Process Digital Twin also provides a systematic approach to evaluating, improving, and standardizing data across different enterprise systems (ERP, MES, Excel, etc.). These transformation projects can be executed at various levels of detail and areas of focus, with each focus area addressed within a specific application workstream to analyze, design, and implement initiatives that contribute to the project’s overall transformation goals.
Process Digital Twin Includes
- All physical constraints in the process
- Business rules governing the system
- Detail shopfloor-level decision logic
- Tribal knowledge of the workforce
- Third-party integration
- Data schema for model execution
Comprehensive Model Support
- Process analysis and optimization
- Data cleaning and standardization
- Harmonizing people and process
- Training and testing AI-based solutions
- Planning and scheduling operations
- Orchestrate automated systems
Reference Model to Manage
- Continuous improvement
- Future manufacturing process changes
- Distribution network changes
- New IT system implementations & upgrades
- New product introductions
- Revised operating and safety rules
Application Workstreams
Empowering All The Primary Business Processes
Simio Intelligent Adaptive Process Digital Twins add value for all stakeholders throughout the various phases of digital transformation, including final operational deployment. They address key questions during both the design and investment phases of transformation and business reengineering, as well as for the operational day-to-day management of ongoing manufacturing and supply chain processes.
Leadership
Increase ROI, reduce cost and grow revenue by setting and managing Business KPIs based on key business rules, goals, and objectives.
Operations
Reduce production costs and increase throughput using task and material-level work instructions to synchronize and manage operations, thereby reducing downtime.
Planning
Reduce costs, increase throughput and service, and optimize factory and supply chain performance with production planning and scheduling.
Procurement
Reduce inventory and material/service costs by generating detailed material requirements to optimize procurement, raw material lead times, and material availability.
Supply Chain
Reduce inventory and distribution costs by optimizing the supply chain and inventory, and managing third-party logistics services.
Supervisors
Reduce labor costs and increase throughput with process and labor management, while tracking adherence to the schedule and overall process performance.
Finance
Reduce costs and increase revenue by evaluating the impact of CapEx projects, new product introductions, market expansion, and entry into new markets.
Improvement
Reduce costs and increase throughput with continuous process improvement and design through experimentation, optimization, and what-if analysis.
Typical Development & Deployment Phases
An Intelligent Adaptive Process Digital Twin can be deployed in various steps based on use cases, overall business goals, and transformation requirements. Each deployment step may include the work of one or more application workstreams. The steps below illustrate typical deployment phases, given the scope of the business transformation initiative and the organization’s process and digital maturity. Each step can deliver significant value as part of the overall transformation journey, enabling informed and well-calculated decisions at each stage.