In a manufacturing centric supply chain factory sourcing is a critical decision that drives throughput and on-time delivery. If more than one site is available to produce a product, it is important to balance the load across production sites within the supply chain to ensure available capacity is optimally utilized to achieve on time delivery. This sourcing decision is typically made using Master Production Scheduling (MPS) software to assign each production job to a time bucket (e.g., weekly) at a specific site. The output of the MPS is a list of jobs to produce during each time bucket at each production site. The detailed production scheduling tool then takes the output from the MPS and generates a detailed schedule within the current time bucket for a specific site.
Using the Rough-Cut Capacity Planning Approach
The MPS assumes a fixed production lead time and uses a rough-cut capacity planning (RCCP) approach based on a simple capacity measure (e.g., total hours of assigned work per time bucket) to select the appropriate time bucket and limit the work that is assigned to each time bucket at each production site, utilizing secondary sites as needed to avoid overloading of the preferred production site. However, in its RCCP approach and simplified measurement of available capacity the MPS ignores many important capacity constraints such as changeovers, tooling, labor, material handling, and production rules. MPS then employs a heuristic solver (e.g., CPLEX) which typically takes hours to execute to search for a good feasible solution to this simplified representation of the system. Although legacy systems present their solution as optimal, the heuristic solver does not typically find the optimal solution but simply the best solution that can be found by the search algorithm during the time allocated to solve the problem (typically a few hours). In addition, their rough-cut approximation of both capacity and time yields results that are typically not actionable in the real system and as a result are misaligned with the actual production schedule which must consider all the relevant constraints. This misalignment between the master plan and detailed factory schedules is illustrated below and is a primary cause of poor performance within the supply chain.
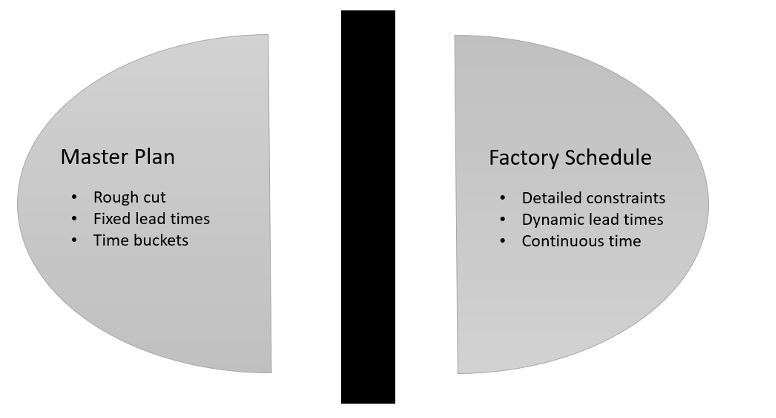
The Problem with a Misaligned MPS System
This misalignment creates inconsistencies across the supply chain and can cause the wrong materials to be planned, purchased, and transported to each site. In many cases the MPS sends more work and associated materials to a production site than can be produced within the time bucket given the real production constraints at the production site.
As illustrated below, even when the MPS generates a feasible list of production orders, the use of artificial time buckets steals capacity from the system since production for the set of assigned orders must ramp up and down at the ends of each time bucket to complete all assigned work within the time bucket. To avoid losing this capacity the factory schedule is sometimes augmented with ad hoc unplanned work orders, which are not part of the master supply chain plan. These ad hoc orders typically do not align with customer demand, which bloats inventory with the wrong products.
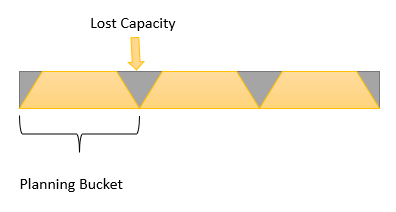
Improving the Model with a Detailed Simulation
In contrast, Simio’s Solution Platform for multi-plant supply chain captures all critical constraints at each inventory and production site along a true time horizon and produces a consistent, optimized, and actionable plan across the supply chain. This solution combines detailed simulation models of each site to accurately capture the evolving state of the system, DDMRP replenishment logic to generate replenishment orders, and neural networks to dynamically estimate production lead times at each production site, which are then used to optimize the assignment of production orders to sites. This synergistic use of DDMRP to plan when replenishment should occur and neural networks (NN’s) to optimize the selection between candidate production sites eliminates the need for the separate and long-running MPS software module to pre-assign work to artificial time buckets at sites and allows production to be planned along a continuous time frame.
As noted above, DDMRP is used within the supply chain model to generate replenishment orders, which in turn may generate production orders. When there is more than one candidate site that can supply the replenishment order a sourcing decision is required. If the preferred site always has adequate inventory buffer quantities, then the decoupled lead time (DLT) that is used to size the DDMRP buffers ensures that replenishment from the preferred site will occur in time to avoid late orders. However, variation in demand can sometimes drive inventory at the preferred replenishment site to be low or out of stock and congestion at a preferred production site can cause a longer lead time than planned to fill a replenishment order, thereby creating late orders. In this case alternate replenishment sites must be considered to balance the production load across sites.
How Constrained Lead Time Factors Into the Model
Each candidate site has a constrained lead time (CLT) that is different than the DLT that is used for DDMRP planning. The CLT is the lead time based on the actual constraints in the system given the current state at the site. The CLT is impacted by inventory levels, product mix and changeovers, labor, tooling, etc. Unlike the DLT, the CLT dynamically changes as new orders arrive at the site and production proceeds. For example, if a production site is out of inventory and has lots of work in process with a high product mix requiring lengthy changeovers, the CLT for a new order may be significantly longer than the DLT used for DDMRP planning. In this case an alternative supplier with a smaller CLT may be desirable.
The CLT for a candidate site depends on the current level of inventory, the expected arrival time of any replenishment orders that are already in process, and the expected replenishment time if a new replenishment must be completed before the order can be filled. If a new replenishment is from production, the replenishment time is the expected production time given the current state of the production site. If replenishment is from a supplier, then the CLT is the CLT of the selected supplier, which may recurse back through the supply chain, eventually hitting a production site.
The one difficult component for computing the CLT is estimating the production lead time at a production site based on the current state of the site. However, Simio’s neural network features provide an ideal solution to this problem. The sourcing decision can then be optimized based on the predicted CLT for each candidate site, where the least cost site that can deliver on time is selected.
The Effects of Involving AI and Third Parties
Although AI has proven itself to be highly effective at solving difficult regression problems, one of the major challenges of AI is having the required labeled training data for training the algorithm. Many AI applications fail because of lack of good, labeled training data. Labeled training data is never available when evaluating a new system and even in cases with existing facilities any historical data becomes invalid once a new part or change in flow is introduced to the system. However, Simio’s built-in features for automatically collecting and labeling synthetic training data address this problem. The supply chain Process Digital Twin can self-generate all the required data for training the neural networks to accurately predict the production lead time given the current state of the site.
Simio’s built-in AI features provide support for defining, training, and using the classic feed forward regression neural network. However, as illustrated below, you are not limited to this machine learning algorithm since you can also import and use within Simio any machine learning regression model from over 50 third parties including Google and Microsoft that support the ONNX model exchange format. You can build and train models in third-party tools and then import them to Simio for complex decision making within your model. Exporting to the ONNX file format is also supported. You can also use Simio models to generate synthetic labeled training data for export for use by third party tools.
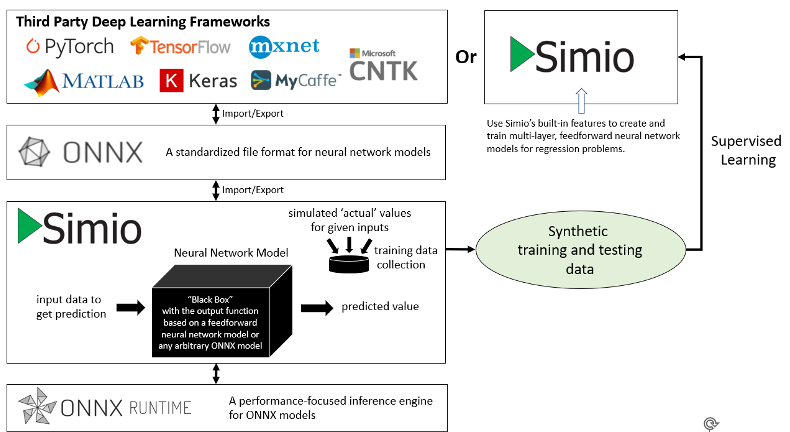
Accomplishing Goals with an AI-Driven Digital Twin
The benefits of the Simio Solution Platform for multi-plant scheduling begin with its accurate capacity model, continuous time horizon, AI-based optimization of factory sourcing, and fast execution to generate actionable schedules that are aligned across the supply chain. But the benefits culminate in Simio Solution Platform’s ability to communicate its structure, its model logic, and the resulting production schedules to everyone who needs to know. Simio provides more operational insights over traditional static MPS outputs through interactive 3D animation of the schedule, allowing users to preview a planned workflow. Detailed animation shows the movement of parts, workers, material handling devices, and other critical constraints as the planned schedule unfolds. Simio also records detailed transactional data of all constraint actions in scheduling logs that can be viewed, filtered, and used for generating custom reports and dashboards that can be shared across the enterprise using the Simio Portal. The data in these logs include information on materials, resources, orders, and material handling equipment, as well as non-value-added time spent by orders constrained by the system. This information is invaluable for not only judging the quality of the schedule, but also improving the schedule by providing root cause information on schedule delays.
The DDMRP, AI, and Process Digital Twin technologies underpinning the Simio Solution Platform for multi-plant scheduling have evolved and are becoming mainstream. More information on Simio’s Solution Platform can be found in this white paper: How Simio Objects Differ from Other Object-Oriented Modeling Tools. More information on Simio’s DDMRP features can be found in this white paper: Demand Driven Material Requirements Planning Powered by Simio. The time has come to replace your legacy MPS with an AI-driven Digital Twin of the supply chain.