La mise en œuvre de processus de transformation numérique au sein de l’industrie manufacturière est un processus continu depuis environ trois décennies. Dans un premier temps, les fabricants ont utilisé la numérisation pour collecter des données à des fins de stockage avant de passer à des applications plus complexes. L’optimisation de la conception industrielle est devenue l’étape logique suivante pour l’application des technologies de transformation numérique. Toutefois, il a fallu attendre l’introduction des modèles commerciaux de l’industrie 4.0 en 2011 pour que les fabricants appliquent la numérisation à l’amélioration des processus opérationnels.
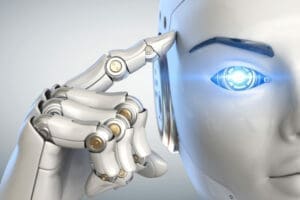
Il est logique de commencer toute discussion sur la numérisation par l’application de modèles virtuels. Les plateformes de conception assistée par ordinateur (CAO) ont fourni aux fabricants le premier outil de numérisation pour la conception de produits et la validation de leurs fonctionnalités. La modélisation 3D a permis aux fabricants de disposer d’un outil intuitif orienté objet pour concevoir des modèles de différents niveaux de complexité.
D’une part, les outils de modélisation tels que Revit d’Autodesk sont utilisés pour concevoir des produits aux géométries complexes, modéliser des environnements de fabrication et préparer des modèles numériques pour la fabrication à l’aide des technologies de fabrication soustractive ou additive. Il est possible de modifier des modèles d’objets physiques, mais c’était la limite de la CAO.
Le jumeau numérique
Améliorant les capacités de numérisation de la CAO, le jumeau numérique a été développé pour fonctionner en parallèle et interagir avec les systèmes de fabrication physiques du monde réel. Tout d’abord, les jumeaux numériques sont des représentations numériques de systèmes physiques qui reçoivent des données en temps réel des actifs producteurs de données au sein de l’atelier, formant ainsi un système cyber-physique.
L’échange continu de données permet aux utilisateurs du jumeau numérique de disposer d’une option virtualisée pour visualiser les fonctions au sein d’une installation. Par conséquent, l’environnement virtuel qu’il fournit sert de plateforme de validation précise pour l’évaluation de problèmes de fabrication complexes. L’utilisation du jumeau numérique en tant qu’outil de surveillance à distance, de contrôle des conditions et d’outil d’essai et de validation est l’un des cas d’utilisation du jumeau numérique.
Au sein du système cyber-physique d’un jumeau numérique fonctionnel, l’échange de données est un processus bidirectionnel. Les données provenant de l’usine sont envoyées au jumeau numérique et celui-ci peut également envoyer des données aux systèmes de l’usine pour déclencher des actions spécifiques. Par exemple, un fournisseur de services pétroliers et gaziers souhaitant déterminer ses besoins en matière d’expansion de capacité a utilisé un jumeau numérique pour déterminer ses besoins en matière d’expansion de capacité.
La détermination des besoins en capacité a commencé par le développement d’un jumeau numérique des processus opérationnels actuels de l’établissement. Ce jumeau numérique a permis à l’entreprise d’analyser les effets d’une augmentation de la demande sur la capacité de service de l’établissement. Diverses configurations de flux de terminaux ont également été évaluées et le résultat a été un niveau de service optimisé qui a amélioré les niveaux de satisfaction des patients.
L’ombre numérique
La confusion entre l’ombre numérique et les jumeaux numériques est une caractéristique normale dans le secteur industriel. D’une part, les deux utilisent les données d’objets physiques pour reconstruire des représentations numériques et, d’autre part, ils peuvent créer des représentations d’objets et de processus. Les similitudes s’arrêtent là.
En général, les ombres numériques s’appuient sur des données laser scannées pour capturer les objets tels qu’ils ont été construits. Plus important encore, le flux de données est un processus à sens unique. Les données circulent de l’entité physique vers l’ombre numérique, mais pas dans l’autre sens. Les ombres numériques peuvent également être créées à partir de jumeaux numériques parce qu’elles peuvent capturer et simplifier la pléthore d’informations qui passent par un jumeau à des périodes spécifiques.
Si l’on reprend l’exemple de l’entreprise pétrolière et gazière ci-dessus, une ombre numérique peut être utilisée pour présenter aux parties prenantes l’application du jumeau numérique conçu. L’ombre fournit aux décideurs non techniques des données sémantiquement adéquates et contextuelles issues de l’application du jumeau numérique.
Le rôle des modèles numériques, du jumeau numérique et des ombres numériques dans la fabrication
Les créneaux de l’industrie manufacturière utilisent ces concepts numérisés de plusieurs manières. Les modèles numériques sont parfaits pour la conception industrielle et le développement d’idées, les ombres numériques sont utiles pour le suivi de la production, tandis que le jumeau numérique permet d’évaluer les processus de fabrication en temps réel.
L’utilisation d’une plateforme capable de fournir ces trois éléments permet aux fabricants de disposer d’un puissant outil de transformation numérique pour l’analyse des données. Les plateformes de jumeaux numériques intelligents basées sur des objets intègrent l’utilisation de modèles 3D pour créer des jumeaux numériques précis qui soutiennent la capture d’ombres numériques. Les jumeaux numériques entièrement développés deviennent une plaque tournante pour l’analyse continue des processus de fabrication, la surveillance à distance et un outil de prise de décision.
Conclusion
Le jumeau numérique relie l’ensemble du processus de fabrication à des modèles numériques et à des ombres. Ces concepts de numérisation peuvent être appliqués ensemble pour optimiser les processus de production et contrôler chaque aspect du cycle de fabrication.