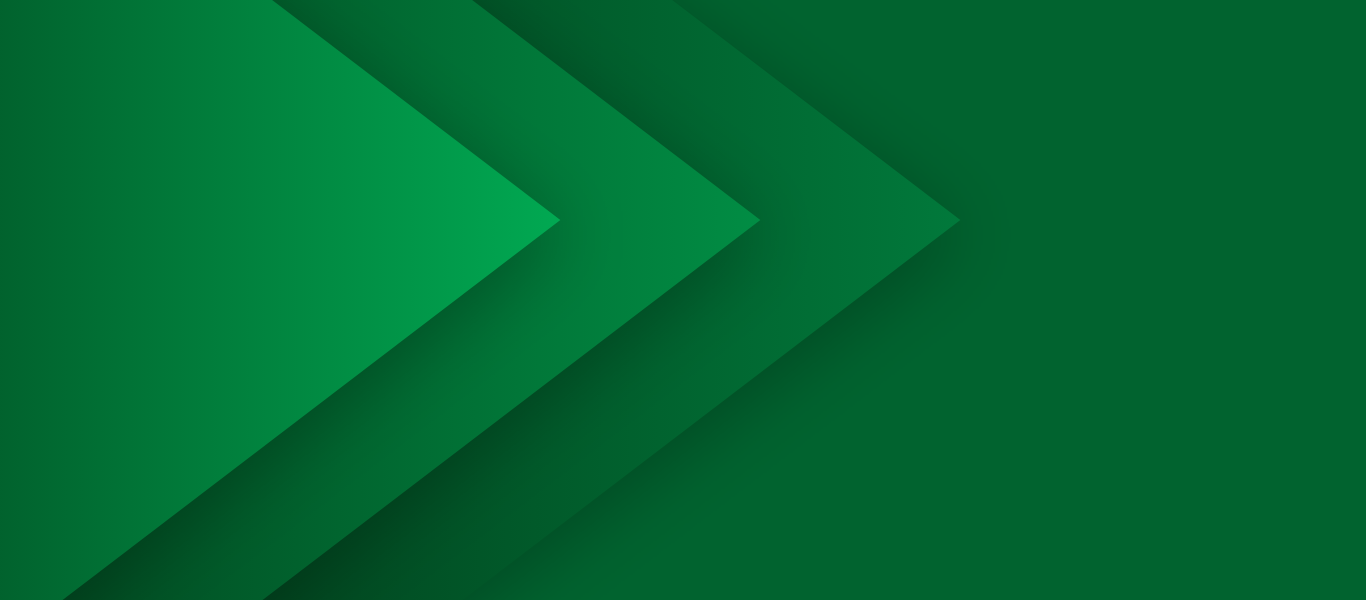
Le processus Simio Digital Twin
Un véritable jumeau numérique qui reproduit fidèlement vos opérations afin de concevoir, d’analyser et d’optimiser, ainsi que de prédire et de prescrire les performances actuelles et futures.
Qu’est-ce qu’un jumeau numérique ?
Le terme « Digital Twin » a gagné en popularité et est devenu une expression passe-partout pour différents modèles numériques. Cependant, la véritable valeur d’un jumeau numérique réside dans sa capacité à représenter avec précision tous les détails des processus opérationnels réels, du comportement et des performances, tout en exploitant pleinement les données de l’entreprise et en s’intégrant de manière transparente aux systèmes opérationnels. Bien que de nombreuses applications promeuvent les capacités des jumeaux numériques, des problèmes importants se posent souvent lors de la mise en œuvre, en particulier lorsqu’il s’agit de s’adapter aux changements survenant dans le processus en cours d’exploitation. Cette défaillance critique compromet souvent la viabilité de nombreuses solutions.
Simio a développé une plateforme agile spécialement conçue pour répondre aux exigences de la création de modèles de jumeaux numériques de processus adaptatifs intelligents qui reproduisent précisément le comportement réel des processus opérationnels et s’intègrent de manière transparente aux données et aux systèmes de l’entreprise. Construite sur notre technologie de pointe de simulation d’événements discrets, la plateforme Simio est conçue pour soutenir les parcours de transformation numérique de l’industrie 4.0. D’un environnement robuste pour la conception, l’expérimentation, l’analyse et l’optimisation des modèles de simulation afin d’améliorer l’efficacité opérationnelle et l’aide à la décision, au déploiement de jumeaux numériques de processus adaptatifs intelligents étroitement intégrés qui permettent des opérations lights-out entièrement autonomes, Simio équipe et guide les utilisateurs à travers un voyage transparent sur l’ensemble du continuum de la conception à l’exploitation.
Intelligent
La combinaison de la simulation d’événements discrets et de l’IA crée une puissante synergie, qui donne naissance à des jumeaux numériques Simio Process dotés d’une intelligence inégalée, capables de générer des solutions hautement optimisées à des problèmes opérationnels complexes avec une efficacité fulgurante.
Adaptatif
Les jumeaux numériques de Simio Process ont la capacité de s’adapter automatiquement aux changements dans les données de l’entreprise telles que les ressources liées au processus, les matériaux, les propriétés et les attributs, les routages de produits, les changements de réseau, la nomenclature, les besoins et les horaires de travail, les horaires de maintenance et la gamme de produits.
Processus
Les processus commerciaux d’un large éventail d’industries peuvent être modélisés avec un jumeau numérique Simio Process, y compris les opérations de fabrication détaillées au sein d’installations uniques et sur plusieurs sites, les opérations d’entreposage et les chaînes d’approvisionnement complexes de bout en bout.
Jumeau numérique
Les jumeaux numériques de Simio Process sont des modèles de simulation d’événements discrets orientés objet, générés et pilotés par les données, qui reproduisent avec précision le comportement physique des processus opérationnels pour des systèmes de toute taille et de toute complexité. Les jumeaux numériques de Simio Process permettent aux utilisateurs de concevoir, d’optimiser, de prédire et de prescrire les performances actuelles et futures des systèmes.
Pourquoi développer un jumeau numérique Simio Process ?
La plateforme agile de Simio pour le développement de jumeaux numériques de processus intelligents et adaptatifs prend en charge un large éventail de flux de travail au sein d’un processus de transformation numérique. Indépendamment de l’axe de travail sélectionné, le développement réussi de jumeaux numériques de processus – qu’il s’agisse de modéliser des processus opérationnels actuels ou futurs – nécessite l’identification, la conception, l’analyse et le soutien à l’exécution des opérations. Quatre raisons clés se distinguent pour utiliser la plateforme Simio à la fois dans les phases de conception et d’analyse et dans les phases de planification opérationnelle et d’ordonnancement de votre transformation d’entreprise. Chacun de ces cas d’utilisation apporte une valeur ajoutée distincte à votre entreprise tout au long des différentes phases de développement et de déploiement de votre projet de transformation.
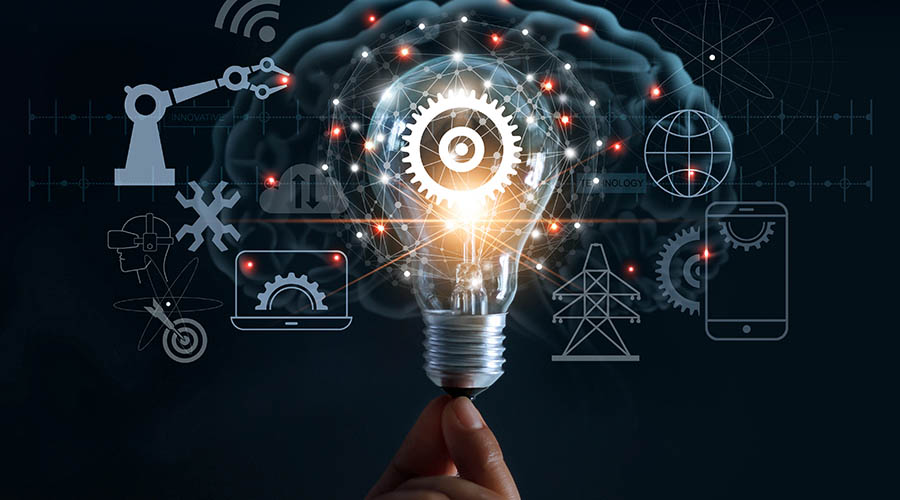
Raison principale n° 1
Base de connaissances
Développez une base de connaissances centralisée et unique en capturant toutes les contraintes du système, les règles de gestion et la logique détaillée dans un modèle complet de simulation d’événements discrets du processus. Cela permet de reproduire avec précision des opérations complexes et critiques sur un seul site ou sur de vastes systèmes multisites.
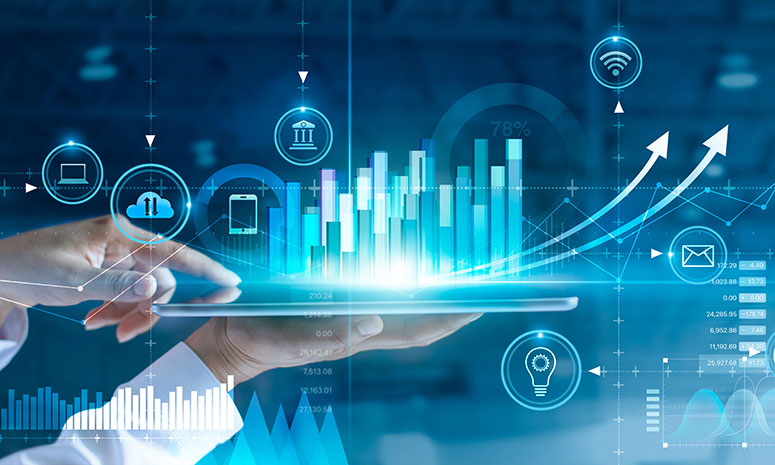
Raison principale n°2
Analyse comparative des performances
Établissez un référentiel de performance des processus pour évaluer les performances actuelles et prédire avec précision les performances futures de l’usine et de la chaîne d’approvisionnement. Cela permet de valider les changements tels que l’automatisation, les nouveaux équipements et les politiques de réapprovisionnement telles que la planification des besoins en matériaux en fonction de la demande (DDMRP).
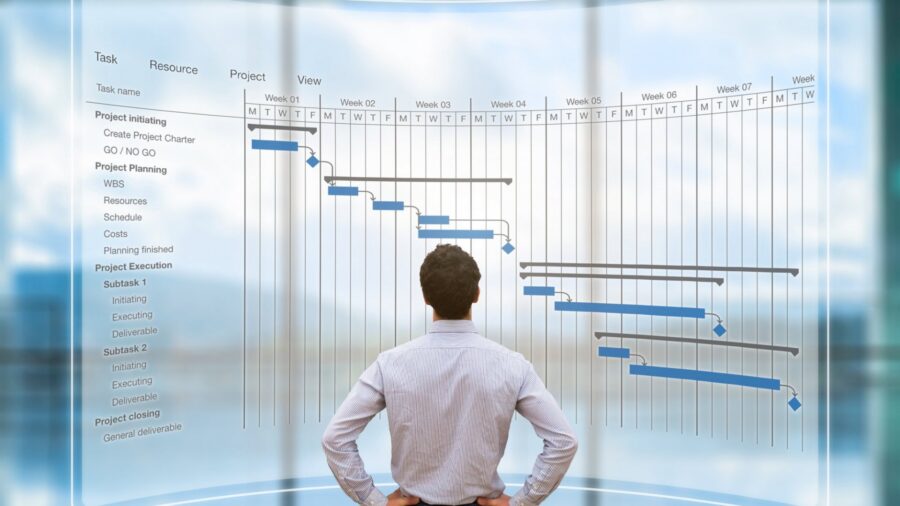
Raison principale n°3
Plan et calendrier
Créez des plans et des calendriers réalisables pour l’atelier, l’entrepôt, l’usine et l’exécution de la chaîne d’approvisionnement dans toutes les plages de temps pertinentes en veillant à ce que les opérations soient réalisables en termes de capacité des ressources, de matériel et de délais. Cela permet une exécution entièrement autonome.
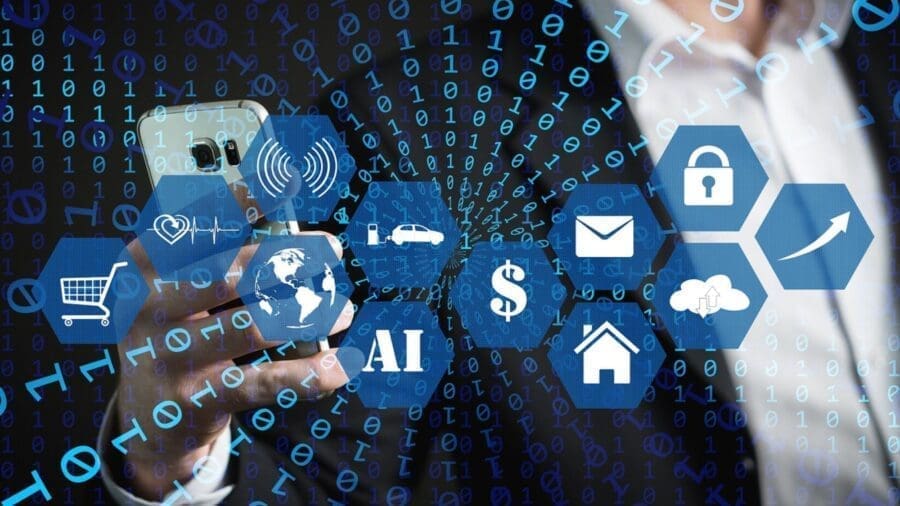
Raison principale n°4
Modèle de référence
Maintenir un jumeau numérique adaptatif, généré et piloté par des données, afin de garantir un modèle de référence numérique de l’état actuel du processus. Cela permet de déterminer les performances futures de l’usine et de la chaîne d’approvisionnement pour les projets de transformation en cours et nouveaux et les décisions d’investissement.
Valeur opérationnelle d’un jumeau numérique de processus Simio
Évaluer les alternatives et analyser l’impact des changements en cours
- Politiques opérationnelles ou changements de processus
- Introduction de nouveaux produits ou matériaux
- Augmentation de la capacité de production ou de l’automatisation (nouveaux équipements, outillage, robotique et AMR)
- Ajuster les compétences requises des travailleurs, les schémas de travail et les niveaux d’effectifs
- Redéfinir l’agencement des usines et réorganiser les séquences d’opérations
- Disponibilité des matériaux et politiques d’inventaire, y compris JIT, Kanban et DDMRP
Créer des plans et des calendriers réalisables et faisables
- Augmentez le débit et la ponctualité des livraisons en synchronisant la production sur l’ensemble du processus.
- Réduire les coûts de production, y compris les dépenses liées aux matériaux, à la main-d’œuvre, aux pénalités, à l’énergie et aux travaux en cours.
- Améliorer le respect du calendrier de production, le taux d’exécution des commandes et les niveaux de service.
- Rationaliser les opérations et améliorer l’efficacité grâce à des opérations autonomes soutenues par une planification et une orchestration en temps quasi réel.
- Optimiser les plans et les calendriers en formant, en testant et en déployant l’IA
Fonctionnalités intégrées de gestion des données et des flux de travail
- Accès multi-utilisateurs par navigateur avec personnalisation des autorisations, des rôles, des caractéristiques et de la localisation.
- Intégration dynamique via des connecteurs de données, y compris des API Web
- Généré et piloté par l’intégration directe ou par des pipelines de données d’entreprise basés sur le cloud.
- Interface avec les applications de support telles que MES, ML/AI/NN, Tableau et Power BI
- Contrôler et distribuer les résultats des modèles à travers les équipes de manière structurée
Composants clés d’un jumeau numérique Simio Process
Des données générées et pilotées
Les modèles sont générés et pilotés par les données de l’entreprise, notamment les ressources, la base de données des articles, les nomenclatures, les itinéraires et l’état actuel. Cela permet d’identifier et de valider les aspects clés des données de l’entreprise, tels que la granularité, la qualité, la corrélation, la vitesse et la disponibilité.
Objets intelligents
Les modèles sont construits à partir d’objets intelligents qui représentent les composants du système tels que les machines, les transporteurs, les robots et les travailleurs, qui peuvent tous s’influencer mutuellement et intégrer l’IA/NN/ML pour améliorer l’optimisation du processus.
Modèles de contraintes
Les modèles de contraintes englobent toutes les contraintes physiques (par exemple, l’équipement, les travailleurs, le transport, le matériel), les règles commerciales (par exemple, le MOQ, les politiques de main-d’œuvre, les politiques d’inventaire) et la logique de décision détaillée (y compris la « connaissance tribale » de l’atelier) pour s’assurer que le modèle reproduit fidèlement le comportement du processus physique.
Piloté par les événements
La technologie de simulation par événements discrets simule l’avancement dans le temps en utilisant le calendrier des événements pour synchroniser toutes les tâches futures et les décisions relatives aux matériaux sur le calendrier d’exécution. Cela garantit la faisabilité du calendrier dans l’atelier pour une exécution pilotée par l’opérateur ou même une orchestration directe dans des environnements hautement automatisés.
Stochastique
Les modèles Simio Process Digital Twin intègrent l’aléatoire, ce qui est crucial pour évaluer la variabilité telle que les pannes de machines et les retards dans l’arrivée des matériaux. Cette capacité permet d’évaluer les risques liés au plan et au calendrier afin de soutenir les actions proactives et d’augmenter la probabilité d’atteindre les objectifs de performance tels que la livraison à temps.
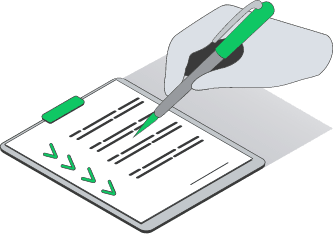
Modèles
Simio fournit une bibliothèque de modèles spécifiques à l’application contenant des objets prédéfinis, une logique de processus et des schémas de données pour lancer le développement du modèle Process Digital Twin pour les processus opérationnels complexes. Chaque modèle est personnalisable pour répondre aux besoins spécifiques de l’utilisateur.
Création d’un jumeau numérique de processus Simio
Le développement d’un modèle de jumeau numérique de processus comporte cinq étapes clés : la documentation de toutes les étapes du processus, la création d’un modèle de simulation et l’intégration du modèle de jumeau numérique de processus avec les systèmes d’entreprise en service et les sources de données pertinentes.
Étape 1 : Spécification des besoins
Documentez toutes les étapes du processus et les besoins des utilisateurs, y compris les contraintes physiques, les règles de gestion et la logique de décision détaillée, afin de créer une spécification des besoins fonctionnels complète qui permette de délimiter et de gérer efficacement le processus de développement.
Étape 2 : Examen des données
Examiner toutes les sources de données pertinentes de l’entreprise, y compris les fichiers Excel et CSV gérés manuellement, pour y trouver les données statiques et dynamiques nécessaires pour générer et piloter le modèle Process Digital Twin.
Étape 3 : Développement du pipeline de données
Développer le pipeline de données nécessaire pour fournir le flux de données qui génère et alimente le modèle Process Digital Twin en s’intégrant directement aux systèmes de l’entreprise ou en utilisant une infrastructure de données basée sur le cloud.
Étape 4 : Élaboration du modèle
Élaborer le modèle détaillé, validé et vérifié de jumeau numérique de processus, orienté objet et fondé sur des données de simulation, afin de prendre en charge les cas d’utilisation en ligne et hors ligne (par exemple, simulation, conception, programmation, orchestration), comme spécifié dans la spécification des exigences fonctionnelles.
Étape 5 : Intégration des données
Intégrez le modèle Process Digital Twin avec des flux de données d’entreprise en direct (par exemple, ERP, MES, PM, IoT) pour une utilisation hors ligne et en ligne, ou pour une aide à la décision et une exécution en temps quasi réel dans des applications prédictives et prescriptives.