Dans une chaîne d’approvisionnement centrée sur la fabrication, l’approvisionnement de l’usine est une décision critique qui détermine le débit et le respect des délais de livraison. Si plusieurs sites sont disponibles pour fabriquer un produit, il est important d’équilibrer la charge entre les sites de production au sein de la chaîne d’approvisionnement afin de s’assurer que la capacité disponible est utilisée de manière optimale pour respecter les délais de livraison. Cette décision d’approvisionnement est généralement prise à l’aide d’un logiciel de planification de la production (Master Production Scheduling, MPS) qui affecte chaque tâche de production à une tranche horaire (hebdomadaire, par exemple) sur un site spécifique. Le résultat du MPS est une liste de travaux à produire pour chaque tranche de temps sur chaque site de production. L’outil de planification détaillée de la production utilise ensuite les résultats du PDP et génère un programme détaillé dans l’intervalle de temps actuel pour un site spécifique.
Utilisation de l’approche de la planification grossière des capacités
Le PDP suppose un délai de production fixe et utilise une approche de planification grossière de la capacité (RCCP) basée sur une mesure simple de la capacité (par exemple, le nombre total d’heures de travail assigné par tranche de temps) pour sélectionner la tranche de temps appropriée et limiter le travail assigné à chaque tranche de temps sur chaque site de production, en utilisant des sites secondaires si nécessaire pour éviter la surcharge du site de production préféré. Cependant, dans son approche RCCP et sa mesure simplifiée de la capacité disponible, le SPM ignore de nombreuses contraintes de capacité importantes telles que les changements de production, l’outillage, la main-d’œuvre, la manutention des matériaux et les règles de production. Le MPS utilise ensuite un solveur heuristique (par exemple, CPLEX) dont l’exécution prend généralement des heures pour rechercher une bonne solution réalisable à cette représentation simplifiée du système. Bien que les systèmes existants présentent leur solution comme étant optimale, le solveur heuristique ne trouve généralement pas la solution optimale, mais simplement la meilleure solution pouvant être trouvée par l’algorithme de recherche pendant le temps alloué à la résolution du problème (généralement quelques heures). En outre, leur approximation grossière de la capacité et du temps produit des résultats qui ne sont généralement pas exploitables dans le système réel et qui, par conséquent, ne sont pas alignés sur le programme de production réel qui doit tenir compte de toutes les contraintes pertinentes. Ce décalage entre le plan directeur et les programmes détaillés de l’usine est illustré ci-dessous et constitue l’une des principales causes des mauvaises performances de la chaîne d’approvisionnement.
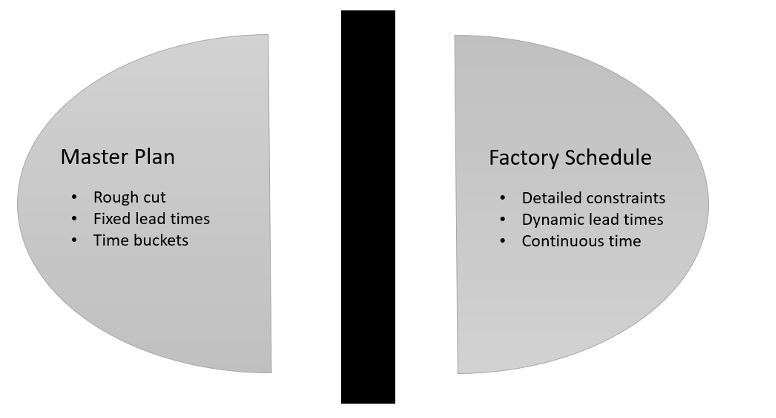
Le problème d’un système MPS mal aligné
Ce désalignement crée des incohérences tout au long de la chaîne d’approvisionnement et peut entraîner la planification, l’achat et le transport de matériaux inappropriés vers chaque site. Dans de nombreux cas, le PDP envoie à un site de production plus de travail et de matériaux associés qu’il n’est possible d’en produire dans le délai imparti, compte tenu des contraintes de production réelles sur le site de production.
Comme illustré ci-dessous, même lorsque le PDP génère une liste réalisable d’ordres de production, l’utilisation d’intervalles de temps artificiels prive le système de sa capacité puisque la production pour l’ensemble des ordres assignés doit augmenter et diminuer à la fin de chaque intervalle de temps afin d’achever tous les travaux assignés dans l’intervalle de temps en question. Pour éviter de perdre cette capacité, le programme de l’usine est parfois complété par des ordres de travail ad hoc non planifiés, qui ne font pas partie du plan directeur de la chaîne d’approvisionnement. Ces commandes ad hoc ne correspondent généralement pas à la demande des clients, ce qui a pour effet de gonfler les stocks avec les mauvais produits.
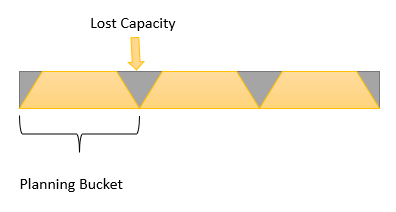
Améliorer le modèle par une simulation détaillée
En revanche, la plateforme de solutions Simio pour la chaîne d’approvisionnement multi-usines capture toutes les contraintes critiques sur chaque site d’inventaire et de production sur un véritable horizon temporel et produit un plan cohérent, optimisé et exploitable sur l’ensemble de la chaîne d’approvisionnement. Cette solution combine des modèles de simulation détaillés de chaque site pour capturer avec précision l’état évolutif du système, la logique de réapprovisionnement DDMRP pour générer des ordres de réapprovisionnement, et des réseaux neuronaux pour estimer dynamiquement les délais de production sur chaque site de production, qui sont ensuite utilisés pour optimiser l’affectation des ordres de production aux sites. Cette utilisation synergique du DDMRP pour planifier le moment du réapprovisionnement et des réseaux neuronaux pour optimiser la sélection entre les sites de production candidats élimine la nécessité d’un module logiciel MPS distinct et de longue durée pour pré-affecter le travail à des tranches de temps artificielles sur les sites et permet de planifier la production sur un horizon temporel continu.
Comme indiqué ci-dessus, le modèle DDMRP est utilisé dans le modèle de chaîne d’approvisionnement pour générer des ordres de réapprovisionnement, qui à leur tour peuvent générer des ordres de production. Lorsqu’il existe plus d’un site candidat capable de fournir la commande de réapprovisionnement, une décision d’approvisionnement est nécessaire. Si le site préféré dispose toujours de quantités de stocks tampons suffisantes, le délai d’exécution découplé (DLT) utilisé pour dimensionner les tampons DDMRP garantit que le réapprovisionnement à partir du site préféré aura lieu à temps pour éviter les commandes tardives. Toutefois, les variations de la demande peuvent parfois conduire à ce que les stocks du site de réapprovisionnement préféré soient faibles ou épuisés, et la congestion d’un site de production préféré peut entraîner un délai plus long que prévu pour exécuter une commande de réapprovisionnement, ce qui crée des commandes tardives. Dans ce cas, d’autres sites de réapprovisionnement doivent être envisagés pour équilibrer la charge de production entre les sites.
Comment le délai d’exécution contraint est-il pris en compte dans le modèle ?
Chaque site candidat a un délai contraint (CLT) qui est différent du DLT utilisé pour la planification DDMRP. Le CLT est le délai basé sur les contraintes réelles du système, compte tenu de l’état actuel du site. Le CLT est influencé par les niveaux de stock, la gamme de produits et les changements, la main-d’œuvre, l’outillage, etc. Contrairement au DLT, le CLT évolue dynamiquement au fur et à mesure que de nouvelles commandes arrivent sur le site et que la production progresse. Par exemple, si un site de production n’a plus de stock et a beaucoup de travaux en cours avec un mélange de produits élevé nécessitant de longs changements, le CLT pour une nouvelle commande peut être beaucoup plus long que le DLT utilisé pour la planification DDMRP. Dans ce cas, il peut être souhaitable de faire appel à un autre fournisseur dont le délai de livraison est plus court.
Le CLT d’un site candidat dépend du niveau actuel des stocks, de l’heure d’arrivée prévue des commandes de réapprovisionnement déjà en cours et de l’heure de réapprovisionnement prévue si un nouveau réapprovisionnement doit être effectué avant que la commande puisse être exécutée. Si un nouveau réapprovisionnement provient de la production, le délai de réapprovisionnement est le délai de production prévu compte tenu de l’état actuel du site de production. Si le réapprovisionnement provient d’un fournisseur, le délai de réapprovisionnement est le délai de réapprovisionnement du fournisseur sélectionné, qui peut remonter la chaîne d’approvisionnement et finir par atteindre un site de production.
La seule difficulté pour calculer le CLT est d’estimer le délai de production sur un site de production en fonction de l’état actuel du site. Cependant, les fonctionnalités du réseau neuronal de Simio offrent une solution idéale à ce problème. La décision d’approvisionnement peut alors être optimisée sur la base du CLT prédit pour chaque site candidat, en sélectionnant le site le moins coûteux qui peut livrer dans les délais.
Les effets de l’implication de l’IA et des tiers
Bien que l’IA se soit révélée très efficace pour résoudre des problèmes de régression difficiles, l’un de ses principaux défis consiste à disposer des données de formation étiquetées nécessaires pour entraîner l’algorithme. De nombreuses applications de l’IA échouent en raison du manque de données d’entraînement étiquetées de qualité. Les données d’entraînement étiquetées ne sont jamais disponibles lors de l’évaluation d’un nouveau système et, même dans le cas d’installations existantes, les données historiques deviennent invalides dès qu’une nouvelle pièce ou un changement de flux est introduit dans le système. Cependant, les fonctions intégrées de Simio pour collecter et étiqueter automatiquement les données d’entraînement synthétiques résolvent ce problème. Le jumeau numérique de la chaîne d’approvisionnement peut générer lui-même toutes les données nécessaires à l’entraînement des réseaux neuronaux pour prédire avec précision le délai de production en fonction de l’état actuel du site.
Les fonctions d’IA intégrées de Simio permettent de définir, d’entraîner et d’utiliser le réseau neuronal de régression feed forward classique. Cependant, comme illustré ci-dessous, vous n’êtes pas limité à cet algorithme d’apprentissage automatique puisque vous pouvez également importer et utiliser dans Simio n’importe quel modèle de régression d’apprentissage automatique provenant de plus de 50 tiers, dont Google et Microsoft, qui prennent en charge le format d’échange de modèles ONNX. Vous pouvez construire et former des modèles dans des outils tiers, puis les importer dans Simio pour une prise de décision complexe au sein de votre modèle. L’exportation vers le format de fichier ONNX est également prise en charge. Vous pouvez également utiliser les modèles Simio pour générer des données d’entraînement synthétiques étiquetées qui seront exportées pour être utilisées par des outils tiers.
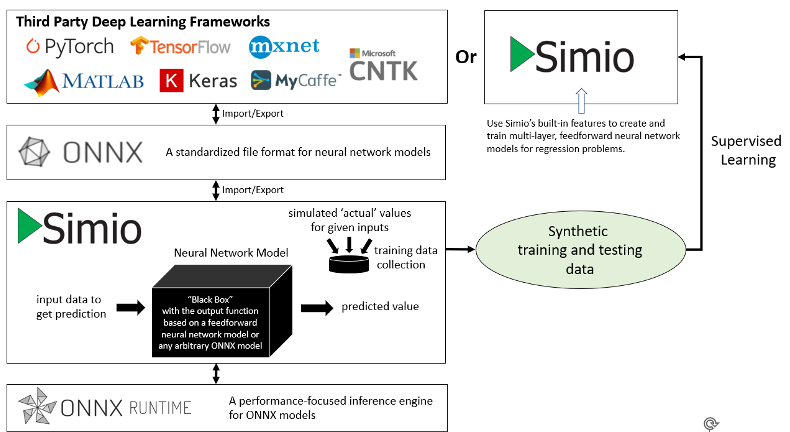
Atteindre les objectifs avec un jumeau numérique piloté par l’IA
Les avantages de la plateforme de solution Simio pour la planification multi-usines commencent avec son modèle de capacité précis, son horizon temporel continu, l’optimisation de l’approvisionnement des usines basée sur l’IA et l’exécution rapide pour générer des plannings exploitables qui sont alignés tout au long de la chaîne d’approvisionnement. Mais les avantages culminent dans la capacité de Simio Solution Platform à communiquer sa structure, sa logique de modèle et les programmes de production qui en résultent à tous ceux qui ont besoin de savoir. Simio fournit plus d’informations opérationnelles que les sorties statiques traditionnelles de MPS grâce à une animation 3D interactive du planning, permettant aux utilisateurs de prévisualiser un flux de travail planifié. L’animation détaillée montre le mouvement des pièces, des travailleurs, des dispositifs de manutention et d’autres contraintes critiques au fur et à mesure que le planning se déroule. Simio enregistre également les données transactionnelles détaillées de toutes les actions liées aux contraintes dans des journaux de planification qui peuvent être visualisés, filtrés et utilisés pour générer des rapports et des tableaux de bord personnalisés qui peuvent être partagés au sein de l’entreprise à l’aide du portail Simio. Les données contenues dans ces journaux comprennent des informations sur les matériaux, les ressources, les commandes et les équipements de manutention, ainsi que sur le temps sans valeur ajoutée passé par les commandes contraintes par le système. Ces informations sont précieuses non seulement pour juger de la qualité du planning, mais aussi pour l’améliorer en fournissant des informations sur les causes profondes des retards.
Les technologies DDMRP, AI et Process Digital Twin qui sous-tendent la plateforme de solutions Simio pour la planification multi-usines ont évolué et se généralisent. Vous trouverez plus d’informations sur la plateforme de solutions Simio dans ce livre blanc : Comment les objets Simio se différencient des autres outils de modélisation orientés objet. Vous trouverez plus d’informations sur les fonctionnalités DDMRP de Simio dans ce livre blanc : Demand Driven Material Requirements Planning Powered by Simio (Planification des besoins matériels en fonction de la demande). Le temps est venu de remplacer votre ancien système MPS par un jumeau numérique de la chaîne d’approvisionnement piloté par l’IA.