2021 Simio Sync: Digital Transformation
WHEN
September 28, 2021
Presentation Highlights & Replays
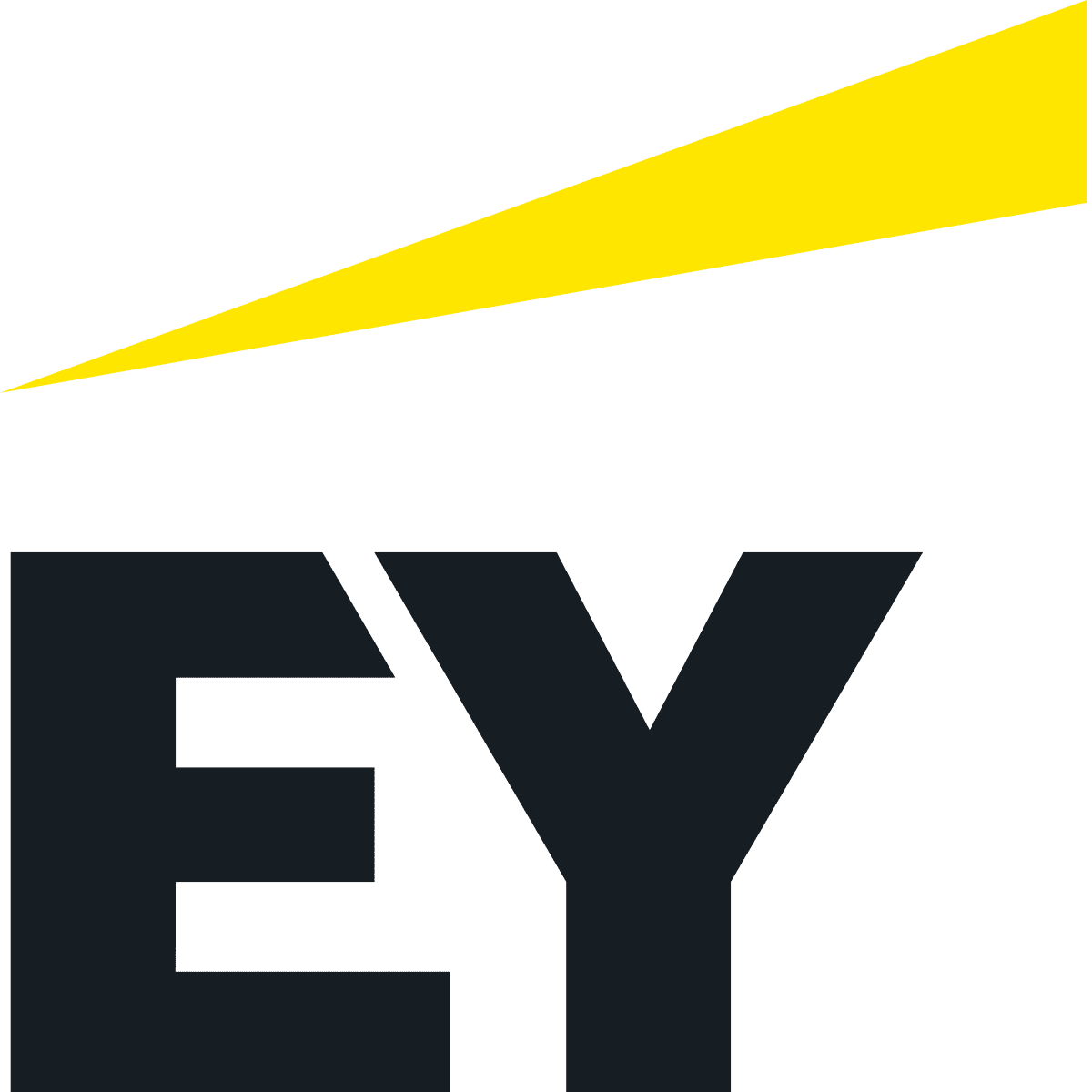
The Pandemic Push: Digital Transformation Takes On A New Sense Of Urgency
Presented by Sachin Lulla, EY Americas Consulting Sector Leader for Advanced Manufacturing & Mobility
COVID-19 has made digital transformation an imperative, exposing the traditional value levers of scope, scale and efficiency as no longer relevant to compete in the manufacturing sector. An HBR study found companies spent $1.3T dollars on Digital Transformation, and $900B of that was wasted due to pilots that did not scale. So what differentiates the leaders from the laggards? As one of the keynote speakers for the 2021 Simio Sync, Sachin Lulla, EY Americas Consulting Sector Leader for Advanced Manufacturing & Mobility, will share his point of view on how Advanced Manufacturing companies can accelerate their Digital Transformation journeys. Listen to Sachin’s keynote presentation and learn about: How the pandemic has accelerated the need for transformation and what are the key drivers Why do most Digital Transformations in Manufacturing fail? How do you build a bridge from Now to the Next and Beyond?
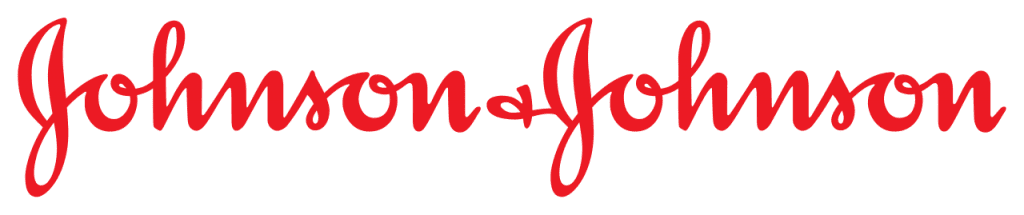
Staying Ahead of Next Crisis: Continuous Wargaming
Presented by Vishal A. Varma, PhD, Director, Digital & Data Science Hanzhang (Sally) Liu, Senior Data Scientist, Digital & Data Science
As we enter an age of sustained volatility and hyper-fast transitions in the external business environment, crisis preparedness is becoming critical towards ensuring business and supply chain resilience. The key elements of crisis preparedness include pro-active monitoring of the external environment, capability to predict the impact of supply and demand shock scenarios and capability to recommend corrective actions and optimal responses to highly disruptive scenarios. In the pharmaceutical and medical industries, the impacts of such disruptions can potentially be felt by patients and healthcare providers. Historically, business continuity teams handle crises around supply disruptions or demand surges via pre-defined contingency plans. However, the traditional approach to crisis preparedness is focused on activating risk mitigation plans for a set of well-known disruption scenarios. In contrast, low probability/high severity scenarios (so-called “black swan” events) are hard to plan for since by definition their occurrence is rare and there is little historical data to plan around (think loss of raw material supply and demand spike occurring simultaneously). Hence the question is – Can we create a “recommender engine” that proposes response plans for a large number of low and high probability disruption scenarios in a highly automated fashion so that supply chain teams can focus on architecting the required infrastructure and execution as opposed to manual contingency planning? There is a significant opportunity for automated digital scenario platforms to step in and provide this service. At Johnson & Johnson, we have taken steps in this direction towards standing up such digital scenario platforms, leveraging digital twin and AI technologies to improve the durability, agility, and resilience of our supply chains and ensure the security of supply (SoS) for our patients and customers. These E2E digital twin platforms based on Simio technology focus on creating virtual replicas of end-to-end value chain networks across suppliers, manufacturing and distribution sites to customer sites. This allows simultaneously optimizing decision trade-offs (at scale and speed) around new manufacturing and quality testing capacity, safety stock and inventory policies, product allocations by targeting outcomes such as cash, product cost, service and capital efficiency. We thereby unlock a high degree of flexibility to “wargame” various combinations of supply and demand scenarios and an ever-ready capability towards staying ahead of the next crisis.
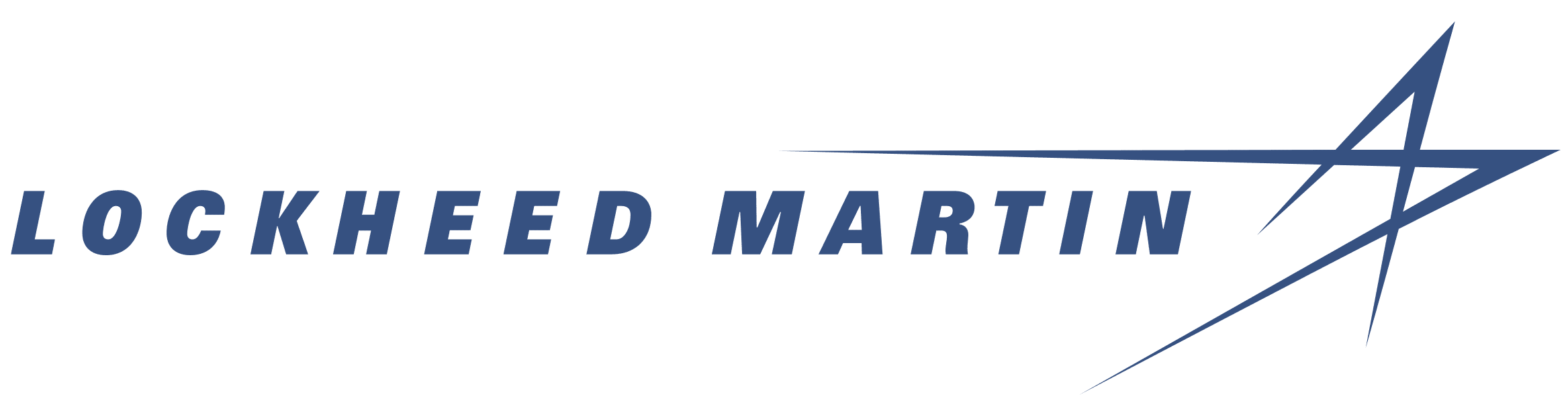
Discrete Event Simulation with Simio at Lockheed Martin Aeronautics - Growth and Challenges
Presented by Scott Swann, Modeling and Simulation Lead
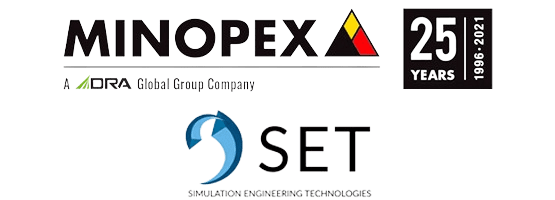
Leveraging Processing Plant Digital Twin to Maximize ROI
Presented by Willem Daling Executive Director of Operations, Simulation Engineering Technologies
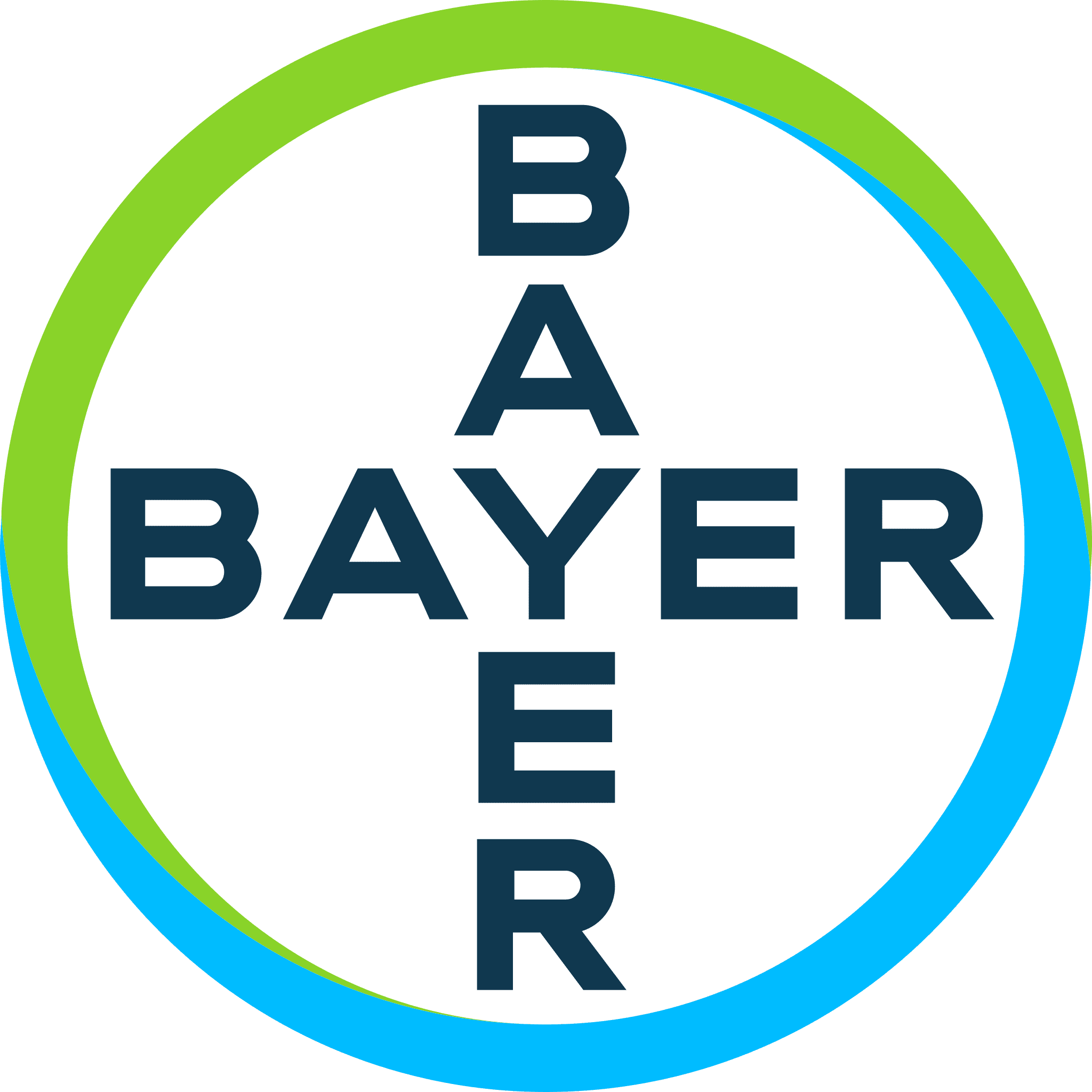
The Journey to Smart Manufacturing at Bayer
Presented by Manuel Pereira Remelhe, Principal Expert Process Simulation
Bayer has been using holistic discrete-event simulation models of complex manufacturing environments, also known as “Virtual Factories”, for more than a decade. As a result of various internal strategic programs, these Virtual Factories have created tremendous business value through more than 50 successful projects (from Bayer Crop Science to Bayer Pharmaceuticals). Operationalizing these Virtual Factories by connecting to enterprise data systems in order to create Digital Twins, is a key technology to unlock the value of Smart Manufacturing and Industry 4.0 at Bayer. A real example of a Simio Digital Twin in action at Bayer Consumer Health will be shown in a separate presentation by Pietro Bertuzzi. This presentation will discuss the organizational setup at Bayer, the current scope of applications, recent steps towards Smart Manufacturing including the Simio Digital Twin, and future initiatives to implement a seamless model lifecycle from design to digital operations, as well as the interconnection to a digital supply chain twin.
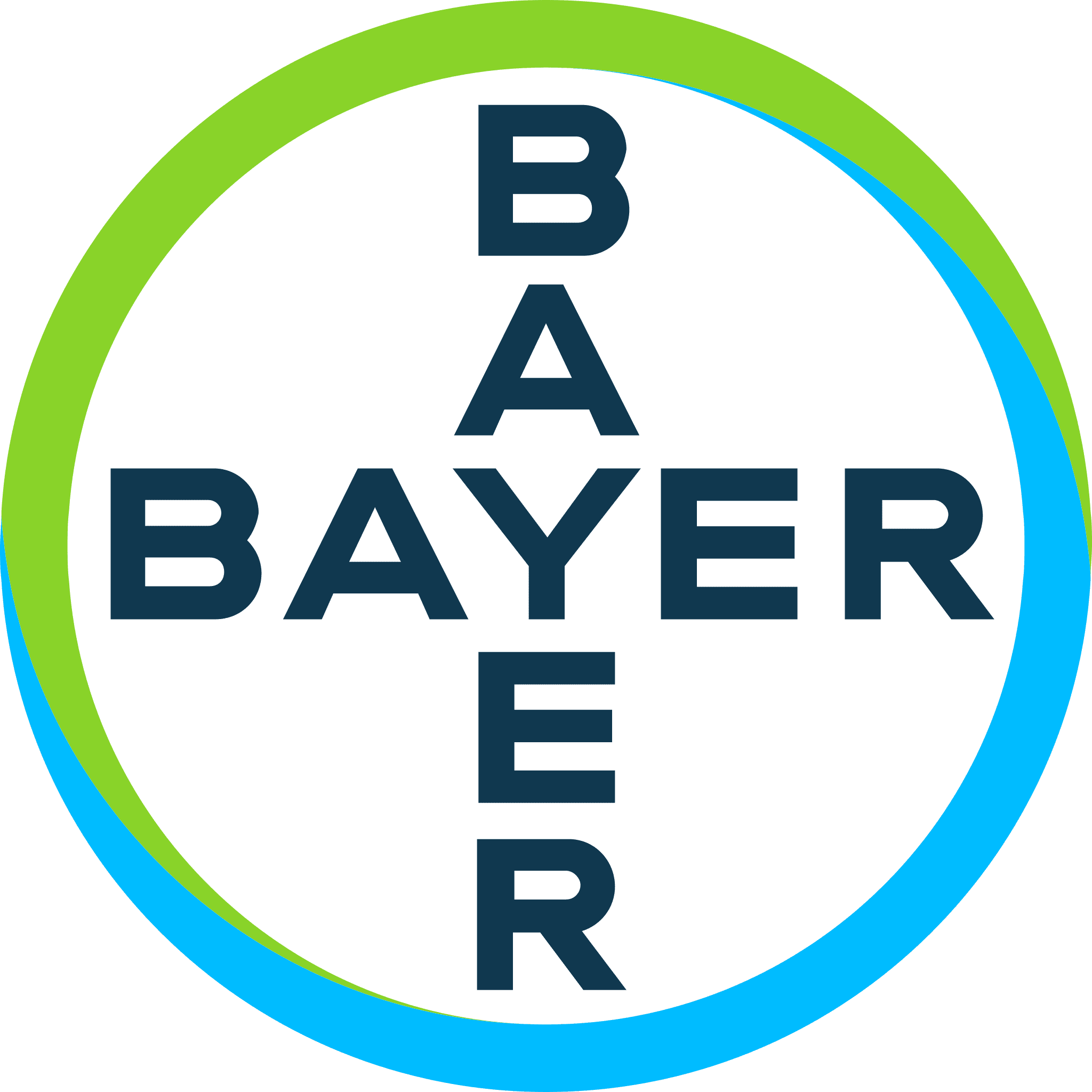
Digital Twin for Production Scheduling in the Consumer Health Industry
Presented by Pietro Bertuzzi, Supply Chain Digital Twin Engineer
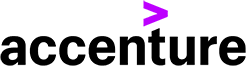
Digital Transformation: Think Big, Start Small, Scale Fast
Presented by Ken Buxton, Principal Director Roman Buil Giné, Data Science Senior Manager
End-to-end Digital Operations Transformation is the reinvention of companies through advanced digital technologies to drive new levels of efficiencies, customer experiences, and sustainability across their engineering, manufacturing, and supply chain functions. Transformation is no longer a once in a generation event…it is now a constant. The increasing pace of innovation combined with rapidly changing social, environmental, and regulatory environments are pressing organizations and ecosystems to continuously evolve to survive and thrive. Rapid Cycle Evolution has been driven by the convergence and application of new technologies to business, organizations, and consumers. Digital Transformation requires organizations to transform, it is not just technology. Leaders must realign business objectives, create new business models, transform experiences, and industrialize operations – taking care to transform to new business and operating models, not mapping digital onto the old.
Based on research from 600 companies spanning 8 industry sectors, located across US, Europe, and Asia, the average digital maturity is 39% (with 100% indicating full deployment). Of the 40 key digital capabilities in which the research focused, three reside in a Digital Cluster focused on Planning, Simulation, and Execution Control. Interestingly, research shows that digital leaders have embraced digital twins as a transformational technology to support key operational capabilities including simulation and dynamic planning and scheduling. The research also revealed drivers that accelerate digital transformation as well as drivers that appear to slow digital technology adoption.
In this presentation, we’ll take you on a journey of discovery and transformation for several companies that have embraced digital technology and begun the transformation of how they operate and how they serve their customers.
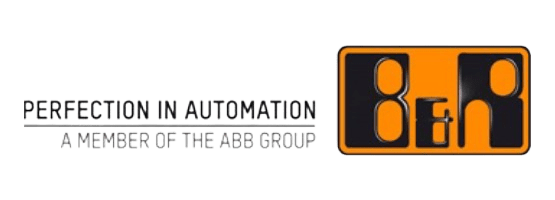
Deploying Digital Twins to Design and Operate Flexible Automated Manufacturing Systems
Presented by Martin Larsen, Head of Nordic Business Development
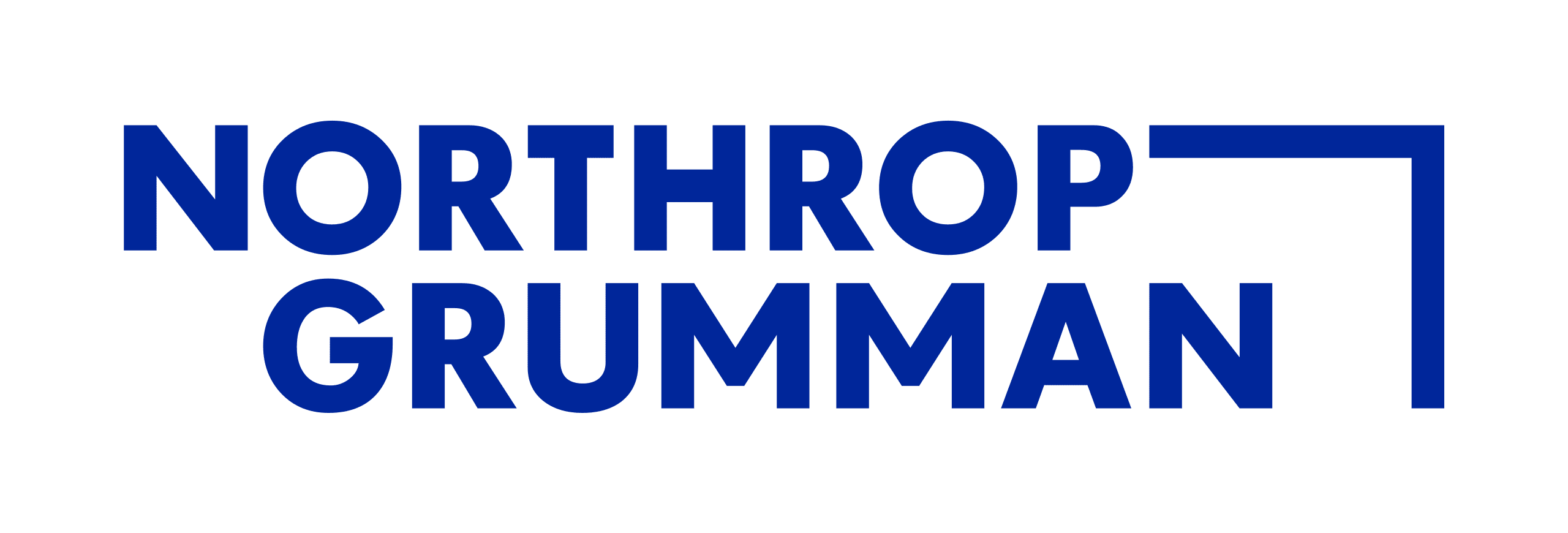
Simio Model Implementation for Space Manufacturing Scheduling & Capacity Planning
Presented by Eliza Sheppard, Industrial Engineer
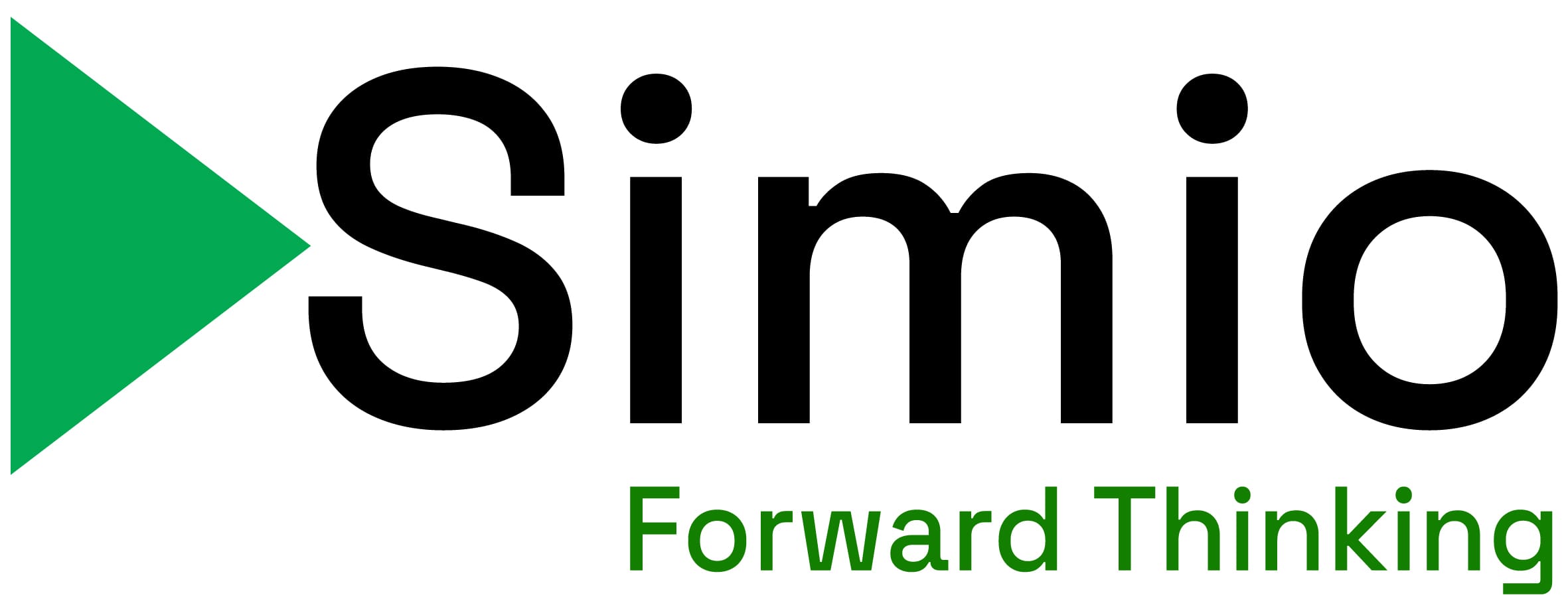
Simio Software Solution Overview
Presented by Renee Thiesing, VP Product
Digital Transformation is part of our business reality and the need to use data for strategic decisions and democratize information across an enterprise has been accelerated by the pandemic. Businesses across all industries have been forced to evolve and become resilient in the face of uncertainty. An organization’s ability to leverage data, visualize their system, perform what-if scenario analysis, and gain insight into real-time operational processes is pivotal to developing successful business strategies. Simio’s simulation based Digital Twin solution can become the central piece of technology enabling a digital transformation, helping companies make better decisions, optimize operations, and drive growth – no matter where you are on your digital transformation path. The journey begins with a virtual model for analyzing and predicting what might happen for a given situation. The model can next be connected to enterprise systems, then becoming a process digital twin, to produce a detailed production schedule that uses operational, real system data as input. As digital maturity increases, the Simio Digital Twin can support autonomous decisioning where the best action is prescribed automatically and sent back to the supporting enterprise systems for execution as part of a fully integrated workflow. Join Renee Thiesing, VP of Products at Simio, as she takes us on a journey of Digital Transformation, highlighting how Simio’s solution can add value at each step in the transformation process. You’ll see the Simio products in action, including examples of integration with other enterprise systems and some new Simio product features.
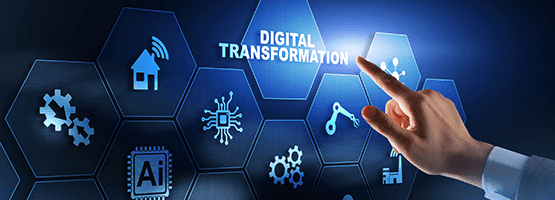
Real-world Perspectives on Undertaking a Digital Transformation Journey and Implementing Digital Twins
Presented by Tony Innamorato, VP Customer Solutions at Simio Manuel Pereira Remelhe, Principal Expert Process Simulation at Bayer Barbara Barańska, Global Workstream Lead - Production Planning at Colgate-Palmolive Eliza Sheppard, Industrial Engineer at Northrop Grumman Wiktor Pawlica, Integration Systems Leader at Colgate-Palmolive Pietro Bertuzzi, Supply Chain Digital Twin Engineer at Bayer
Throughout Simio Sync you’ll hear success stories from all points on the design to operate spectrum. Each success was hard-earned and taught valuable lessons. We’ve asked our Digital Twin clients to share some of their experiences in hopes that others will be encouraged to embark on the journey, borrowing from their experience and leveraging lessons learned. The discussion will be centered on challenges such as:
- Assessing in-house readiness levels, determining skill-gap limitations and the staffing resources needed to adopt new technologies.
- Managing data pipelines.
- Implementing agile, iterative building methodologies to effectively deal with obstacles that arise when utilizing new digital transformation technologies such as a Digital Twin.
- Determining the trade-offs organizations consider due to data unavailability or the quality of available data.
The round table will consist of members of the implementation teams with technical expertise, both internal and external. The audience will learn about managing digital transformation adoption processes.
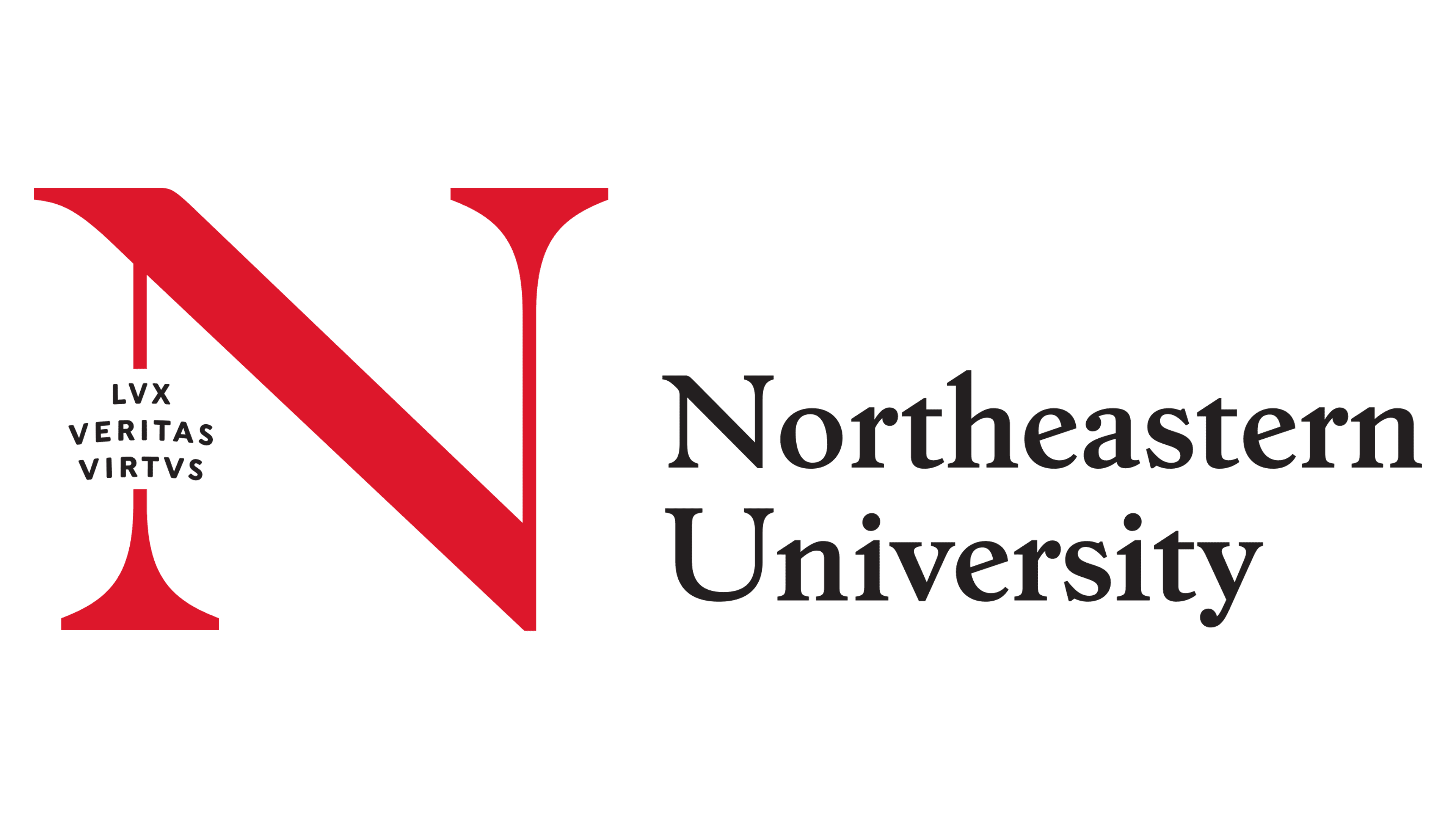
Simulation-Optimization of Digital Twin
Presented by Mohammad Dehghani, PhD, Associate Teaching Professor of Mechanical and Industrial Engineering
The demand for real-time decision-making in the manufacturing industry has given significant attention to the field of Digital Twin (DT). The whole idea revolves around creating a digital counterpart of the physical system based on enterprise data to exploit the effects of numerous parameters and make informed decisions. Based on that, this paper proposes a simulation-optimization framework for the DT model of a Beverage Manufacturing Plant. A data-driven simulation model developed in Simio is integrated with Python to perform Multi-Objective optimization using NSGA-II. The framework explores optimal solutions by simulating multiple scenarios by altering the availability of operators and dispatching/scheduling rules. The results show that simulation optimization can be integrated into the Digital-Twin models as part of real-time production planning and scheduling.
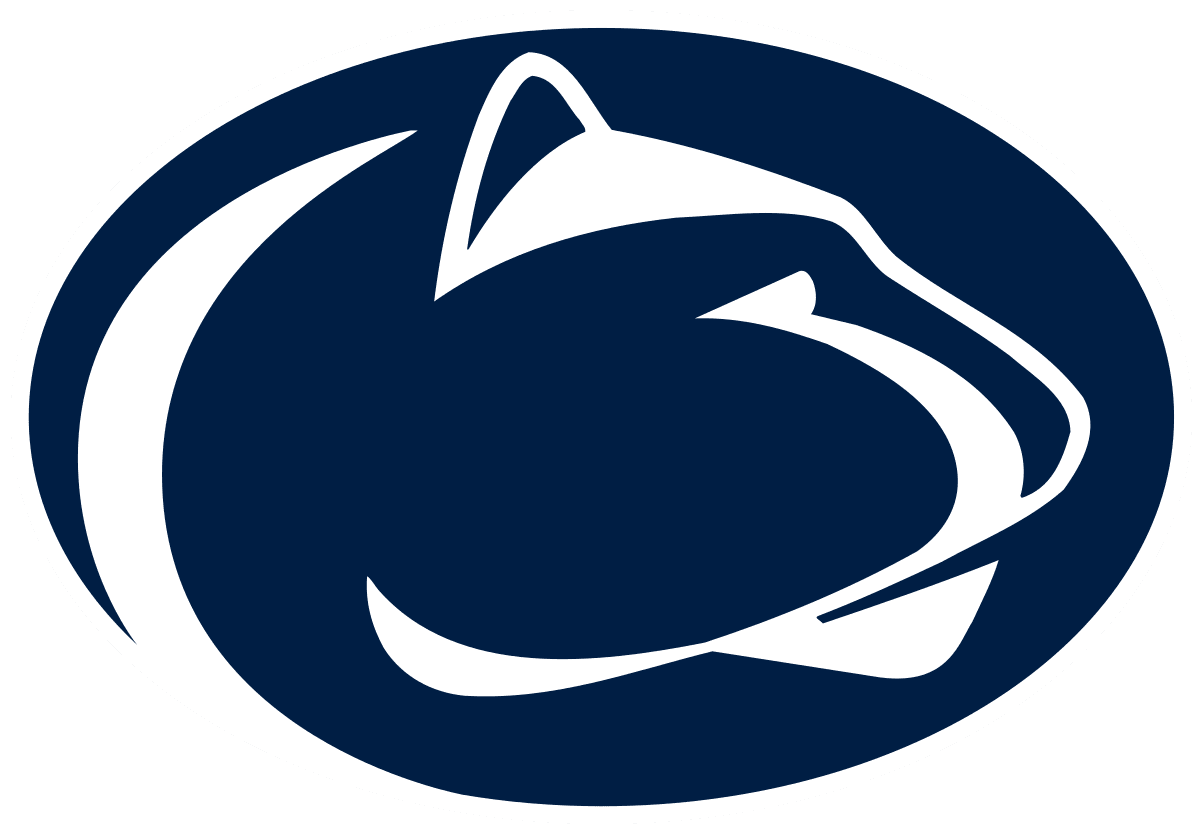
May 2021 Simio Student Competition Winners
Presented by Rob Newton, PhD Student Justin Rist, PhD Student
The Simio Shelving Shop is a shelving manufacturer and wholesaler specializing in several types of shelving units with design variations. The shop is currently experiencing low order fill rates, affecting the shop’s bottom line. Management recently hired an outside consultant to provide recommendations for revamping the inventory and buffering system. The consultant recommended a new buffering and inventory paradigm, Demand Driven Materials Requirement Planning (DDMRP), to address the rampant stockout issue.
The factory currently uses static buffer levels, where all stations have a fixed amount of raw material buffered at their station, and the factory maintains a fixed number of each end item ready to ship. The current buffering method, combined with variations in lead time and quality throughout the factory and its suppliers, drives stockouts of finished goods and raw material. Management embraced the consultant’s recommendation to incorporate a DDMRP buffering solution into the factory because they are convinced that a dynamic buffering solution will improve a collection of selected Key Performance Indicators (KPIs), especially fill rate and average inventory cost. As a secondary objective, management also seeks better methods of monitoring risk in the buffer levels, which the DDMRP buffer profiles will provide.
The challenge is to set up dynamic DDMRP buffers in the factory. This will include leveraging pre-existing data from Sales, Quality, machines, and suppliers to first determine the locations of the buffers, then fine-tune the buffer parameters to improve the selected KPIs. After the buffers are integrated, management wants to predict the change in the factory’s KPIs. Additionally, management would like to reevaluate potential suppliers, which have varying lead times and product quality. This assessment will include recreating optimal buffers for the potential suppliers to determine the impact the supplier could have on the company’s fill rate and average inventory costs.