En una cadena de suministro centrada en la fabricación, el abastecimiento de la fábrica es una decisión crítica que impulsa el rendimiento y la entrega a tiempo. Si hay más de un centro disponible para fabricar un producto, es importante equilibrar la carga entre los centros de producción de la cadena de suministro para garantizar que la capacidad disponible se utiliza de forma óptima para lograr la entrega a tiempo. Esta decisión de abastecimiento suele tomarse utilizando el software de Programación Maestra de la Producción (MPS) para asignar cada trabajo de producción a un intervalo de tiempo (por ejemplo, semanal) en un centro específico. El resultado del MPS es una lista de trabajos a producir durante cada intervalo de tiempo en cada centro de producción. A continuación, la herramienta de programación detallada de la producción toma la salida del MPS y genera una programación detallada dentro del intervalo de tiempo actual para un centro específico.
Utilizar el método de planificación de la capacidad aproximada
El MPS asume un plazo de producción fijo y utiliza un enfoque de planificación de la capacidad de corte aproximado (RCCP) basado en una medida de capacidad simple (por ejemplo, el total de horas de trabajo asignadas por cubo de tiempo) para seleccionar el cubo de tiempo adecuado y limitar el trabajo que se asigna a cada cubo de tiempo en cada centro de producción, utilizando centros secundarios según sea necesario para evitar la sobrecarga del centro de producción preferido. Sin embargo, en su enfoque RCCP y su medición simplificada de la capacidad disponible, el MPS ignora muchas restricciones de capacidad importantes, como los cambios, el utillaje, la mano de obra, la manipulación de materiales y las reglas de producción. A continuación, el MPS emplea un solucionador heurístico (por ejemplo, CPLEX) que suele tardar horas en ejecutarse para buscar una buena solución factible a esta representación simplificada del sistema. Aunque los sistemas heredados presentan su solución como óptima, el solucionador heurístico no suele encontrar la solución óptima, sino simplemente la mejor solución que puede encontrar el algoritmo de búsqueda durante el tiempo asignado para resolver el problema (normalmente unas horas). Además, su aproximación aproximada tanto de la capacidad como del tiempo arroja resultados que no suelen ser procesables en el sistema real y, en consecuencia, están desalineados con el programa de producción real, que debe tener en cuenta todas las restricciones pertinentes. Este desajuste entre el plan maestro y los programas detallados de fábrica se ilustra a continuación y es una de las causas principales del bajo rendimiento de la cadena de suministro.
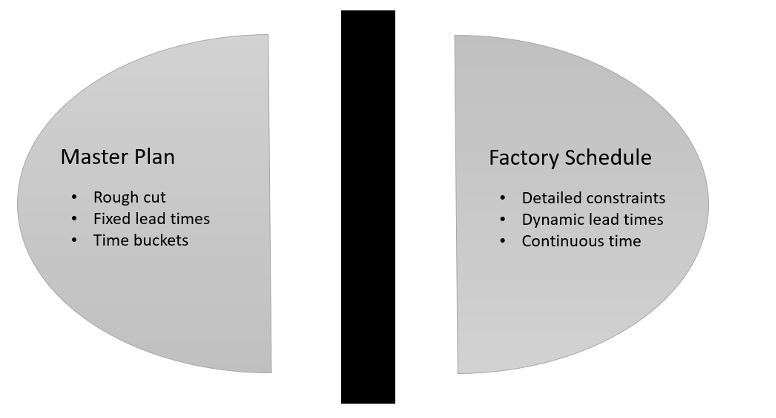
El problema de un sistema MPS mal alineado
Esta desalineación crea incoherencias en toda la cadena de suministro y puede hacer que se planifiquen, compren y transporten materiales equivocados a cada centro. En muchos casos, el MPS envía a un centro de producción más trabajo y materiales asociados de los que pueden producirse dentro del intervalo de tiempo, dadas las limitaciones reales de producción en el centro de producción.
Como se ilustra a continuación, incluso cuando el MPS genera una lista factible de órdenes de producción, el uso de cubos de tiempo artificiales roba capacidad al sistema, ya que la producción para el conjunto de órdenes asignadas debe aumentar y disminuir al final de cada cubo de tiempo para completar todo el trabajo asignado dentro del cubo de tiempo. Para evitar perder esta capacidad, a veces se aumenta el programa de fábrica con órdenes de trabajo ad hoc no planificadas, que no forman parte del plan maestro de la cadena de suministro. Estos pedidos ad hoc no suelen coincidir con la demanda de los clientes, lo que hincha el inventario con productos equivocados.
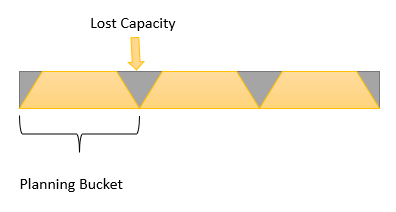
Mejorar el modelo con una simulación detallada
En cambio, la Plataforma de Soluciones Simio para la cadena de suministro multiplanta captura todas las restricciones críticas en cada centro de inventario y producción a lo largo de un horizonte temporal real y produce un plan coherente, optimizado y procesable en toda la cadena de suministro. Esta solución combina modelos de simulación detallados de cada centro para captar con precisión el estado evolutivo del sistema, la lógica de reabastecimiento DDMRP para generar órdenes de reabastecimiento, y redes neuronales para estimar dinámicamente los plazos de producción en cada centro de producción, que luego se utilizan para optimizar la asignación de órdenes de producción a los centros. Este uso sinérgico del DDMRP para planificar cuándo debe producirse el reaprovisionamiento y de las redes neuronales (NN) para optimizar la selección entre los centros de producción candidatos elimina la necesidad del módulo de software MPS, independiente y de larga duración, de preasignar trabajo a cubos de tiempo artificiales en los centros, y permite planificar la producción a lo largo de un marco temporal continuo.
Como ya se ha indicado, el DDMRP se utiliza en el modelo de la cadena de suministro para generar pedidos de reaprovisionamiento, que a su vez pueden generar órdenes de producción. Cuando hay más de un centro candidato que puede suministrar el pedido de reaprovisionamiento, es necesario tomar una decisión de aprovisionamiento. Si el centro preferido siempre dispone de cantidades adecuadas de existencias intermedias, el plazo de entrega desacoplado (DLT) que se utiliza para dimensionar las existencias intermedias del DDMRP garantiza que el reaprovisionamiento desde el centro preferido se producirá a tiempo para evitar pedidos tardíos. Sin embargo, la variación de la demanda a veces puede hacer que el inventario del centro de reaprovisionamiento preferido sea bajo o esté agotado, y la congestión en un centro de producción preferido puede provocar un plazo de entrega más largo de lo previsto para atender un pedido de reaprovisionamiento, creando así pedidos tardíos. En este caso, deben considerarse centros de reabastecimiento alternativos para equilibrar la carga de producción entre los centros.
Cómo influye el plazo de entrega limitado en el modelo
Cada centro candidato tiene un plazo de entrega limitado (CLT) que es diferente del DLT que se utiliza para la planificación DDMRP. El CLT es el plazo de entrega basado en las restricciones reales del sistema, dado el estado actual del centro. El CLT se ve afectado por los niveles de inventario, la mezcla de productos y los cambios, la mano de obra, el utillaje, etc. A diferencia del DLT, el CLT cambia dinámicamente a medida que llegan nuevos pedidos al centro y la producción avanza. Por ejemplo, si un centro de producción no tiene existencias y tiene mucho trabajo en curso con una gran mezcla de productos que requiere cambios prolongados, el CLT de un nuevo pedido puede ser significativamente más largo que el DLT utilizado para la planificación DDMRP. En este caso, puede ser conveniente un proveedor alternativo con un CLT menor.
El CLT de un centro candidato depende del nivel actual de inventario, de la hora prevista de llegada de los pedidos de reaprovisionamiento que ya estén en proceso y del tiempo previsto de reaprovisionamiento si hay que completar un nuevo reaprovisionamiento antes de poder atender el pedido. Si un nuevo reaprovisionamiento procede de producción, el tiempo de reaprovisionamiento es el tiempo de producción previsto dado el estado actual del centro de producción. Si el reaprovisionamiento procede de un proveedor, entonces el CLT es el CLT del proveedor seleccionado, que puede recurrir a través de la cadena de suministro, llegando finalmente a un centro de producción.
El único componente difícil para calcular el CLT es estimar el plazo de fabricación en un centro de producción basándose en el estado actual del centro. Sin embargo, las funciones de red neuronal de Simio proporcionan una solución ideal a este problema. La decisión de aprovisionamiento puede optimizarse basándose en el CLT previsto para cada centro candidato, seleccionando el centro de menor coste que pueda entregar a tiempo.
Los efectos de implicar a la IA y a terceros
Aunque la IA ha demostrado ser muy eficaz para resolver problemas de regresión difíciles, uno de los principales retos de la IA es disponer de los datos de entrenamiento etiquetados necesarios para entrenar el algoritmo. Muchas aplicaciones de IA fracasan por falta de buenos datos de entrenamiento etiquetados. Nunca se dispone de datos de entrenamiento etiquetados cuando se evalúa un sistema nuevo, e incluso en casos con instalaciones existentes, cualquier dato histórico pierde validez una vez que se introduce en el sistema una pieza nueva o un cambio en el flujo. Sin embargo, las funciones integradas de Simio para recopilar y etiquetar automáticamente datos de entrenamiento sintéticos resuelven este problema. El Gemelo Digital de Proceso de la cadena de suministro puede autogenerar todos los datos necesarios para entrenar las redes neuronales y predecir con precisión el plazo de producción dado el estado actual del centro.
Las funciones de IA integradas en Simio permiten definir, entrenar y utilizar la clásica red neuronal de regresión feed forward. Sin embargo, como se ilustra a continuación, no estás limitado a este algoritmo de aprendizaje automático, ya que también puedes importar y utilizar en Simio cualquier modelo de regresión de aprendizaje automático de más de 50 terceros, incluidos Google y Microsoft, que admitan el formato de intercambio de modelos ONNX. Puedes construir y entrenar modelos en herramientas de terceros y luego importarlos a Simio para tomar decisiones complejas dentro de tu modelo. También se admite la exportación al formato de archivo ONNX. También puedes utilizar los modelos de Simio para generar datos de entrenamiento sintéticos etiquetados para exportarlos y utilizarlos con herramientas de terceros.
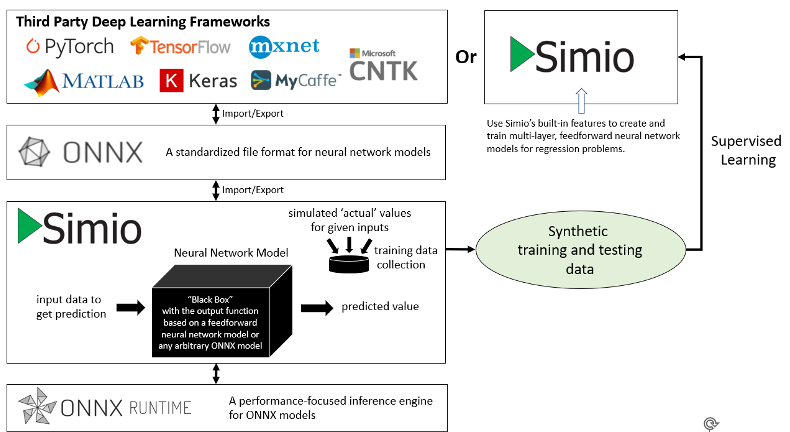
Conseguir objetivos con un gemelo digital basado en IA
Las ventajas de la Plataforma de Soluciones Simio para la programación multiplanta comienzan con su modelo de capacidad preciso, su horizonte temporal continuo, la optimización basada en IA del abastecimiento de las fábricas y su rápida ejecución para generar programaciones procesables y alineadas en toda la cadena de suministro. Pero las ventajas culminan en la capacidad de Simio Solution Platform para comunicar su estructura, la lógica de su modelo y las programaciones de producción resultantes a todo el que necesite saberlo. Simio proporciona más información operativa que los resultados estáticos tradicionales de MPS mediante la animación 3D interactiva de la programación, que permite a los usuarios previsualizar un flujo de trabajo planificado. La animación detallada muestra el movimiento de piezas, trabajadores, dispositivos de manipulación de materiales y otras limitaciones críticas a medida que se desarrolla el programa planificado. Simio también registra datos transaccionales detallados de todas las acciones de las restricciones en registros de programación que pueden visualizarse, filtrarse y utilizarse para generar informes y cuadros de mando personalizados que pueden compartirse en toda la empresa mediante el Portal Simio. Los datos de estos registros incluyen información sobre materiales, recursos, pedidos y equipos de manipulación de materiales, así como el tiempo sin valor añadido empleado por los pedidos restringidos por el sistema. Esta información es inestimable no sólo para juzgar la calidad de la programación, sino también para mejorarla proporcionando información sobre la causa raíz de los retrasos en la programación.
Las tecnologías DDMRP, IA y Gemelo Digital de Procesos en las que se basa la Plataforma de Soluciones Simio para la programación multiplanta han evolucionado y se están convirtiendo en la corriente principal. Puedes encontrar más información sobre la Plataforma de soluciones de Simio en este libro blanco: En qué se diferencian los objetos de Simio de otras herramientas de modelado orientadas a objetos. Puedes encontrar más información sobre las funciones DDMRP de Simio en este libro blanco: Planificación de necesidades de material en función de la demanda con Simio. Ha llegado el momento de sustituir tu MPS heredado por un Gemelo Digital de la cadena de suministro impulsado por IA.