Die Implementierung digitaler Transformationsprozesse in der Fertigungsindustrie ist seit etwa drei Jahrzehnten ein kontinuierlicher Prozess. Zunächst nutzten die Hersteller die Digitalisierung, um Daten für Speicherzwecke zu sammeln, bevor sie zu komplexeren Anwendungen übergingen. Die Optimierung des Industriedesigns war der nächste logische Schritt bei der Anwendung digitaler Transformationstechnologien. Doch erst mit der Einführung von Industrie 4.0-Geschäftsmodellen im Jahr 2011 setzten die Hersteller die Digitalisierung zur Verbesserung der betrieblichen Abläufe ein.
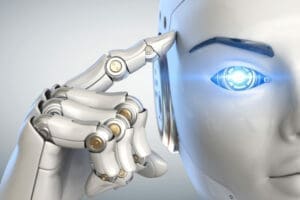
Logischerweise ist es nur richtig, jede Diskussion über die Digitalisierung mit der Anwendung von virtuellen Modellen zu beginnen. CAD-Plattformen (Computer-Aided Design) boten den Herstellern das erste Digitalisierungswerkzeug für das Design von Produkten und die Validierung ihrer Funktionalitäten. Mit der 3D-Modellierung erhielten die Hersteller ein intuitives, objektorientiertes Werkzeug für den Entwurf von Modellen mit unterschiedlichen Komplexitätsgraden.
Zum einen werden Modellierungstools wie Revit von Autodesk verwendet, um Produkte mit komplexen Geometrien zu entwerfen, um Fertigungsumgebungen zu modellieren und um digitale Modelle für die Fertigung mit subtraktiven oder additiven Fertigungstechnologien vorzubereiten. Die Bearbeitung von Modellen physischer Objekte ist möglich, aber das war die Grenze, die man mit CAD erreichen konnte.
Der digitale Zwilling
Der digitale Zwilling, der die Digitalisierungsmöglichkeiten von CAD verbessert, wurde entwickelt, um parallel zu laufen und mit realen physischen Fertigungssystemen zu interagieren. Zunächst einmal sind digitale Zwillinge digitale Repräsentationen physischer Systeme, die Echtzeitdaten von den datenproduzierenden Anlagen in der Fertigung erhalten und ein cyber-physisches System bilden.
Durch den ständigen Datenaustausch erhalten die Benutzer des digitalen Zwillings die Möglichkeit, die Funktionen innerhalb einer Anlage in virtueller Form zu betrachten. Folglich dient die virtuelle Umgebung, die er bietet, als genaue Validierungsplattform für die Bewertung komplexer Fertigungsprobleme. Die Nutzung des digitalen Zwillings als Fernüberwachungswerkzeug, Zustandsüberwachung und als Test- und Validierungswerkzeug sind einige der Anwendungsfälle für den digitalen Zwilling.
Innerhalb des cyber-physischen Systems eines funktionalen digitalen Zwillings erfolgt der Datenaustausch in beide Richtungen. Daten aus der Fabrik werden an den digitalen Zwilling gesendet und dieser kann auch Daten an Systeme in der Fabrik senden, um bestimmte Aktionen auszulösen. Ein Beispiel: Ein Öl- und Gasdienstleister, der seinen Bedarf an Kapazitätserweiterungen ermitteln wollte, nutzte einen digitalen Zwilling, um seinen Bedarf an Kapazitätserweiterungen zu ermitteln.
Die Ermittlung des Kapazitätsbedarfs begann mit der Entwicklung eines digitalen Zwillings der aktuellen Betriebsabläufe der Einrichtung. Der digitale Zwilling ermöglichte es dem Unternehmen, die Auswirkungen einer erhöhten Nachfrage auf die Servicekapazität der Einrichtung zu analysieren. Es wurden auch verschiedene Konfigurationen des Terminalflusses bewertet. Das Ergebnis war ein optimiertes Serviceniveau, das die Zufriedenheit der Patienten verbesserte.
Der digitale Schatten
Die Verwechslung des digitalen Schattens mit digitalen Zwillingen ist im industriellen Bereich üblich. Erstens nutzen beide die Daten physischer Objekte, um digitale Repräsentationen zu erstellen, und zweitens können sie Repräsentationen von Objekten und Prozessen erstellen. Hier enden die Gemeinsamkeiten.
Im Allgemeinen stützen sich digitale Schatten auf gescannte Laserdaten, um Objekte im Ist-Zustand zu erfassen. Noch wichtiger ist, dass der Datenfluss ein einseitiger Prozess ist. Die Daten fließen von der physischen Einheit zum digitalen Schatten, aber nicht andersherum. Digitale Schatten können auch von digitalen Zwillingen erstellt werden, da sie die Fülle von Informationen, die einen Zwilling zu bestimmten Zeitpunkten durchlaufen, erfassen und vereinfachen können.
In Anlehnung an das obige Beispiel des Öl- und Gasunternehmens kann ein digitaler Schatten verwendet werden, wenn Stakeholdern Präsentationen über die Anwendung des entwickelten digitalen Zwillings bereitgestellt werden. Semantisch adäquate und kontextbezogene Daten aus der Anwendung des digitalen Zwillings sind das, was der Schatten den nicht-technischen Entscheidungsträgern liefert.
Die Rolle von digitalen Modellen, dem digitalen Zwilling und digitalen Schatten in der Fertigung
Die Nischen der Fertigungsindustrie nutzen diese digitalisierten Konzepte auf verschiedene Weise. Digitale Modelle eignen sich hervorragend für das Industriedesign und die Entwicklung von Ideen, digitale Schatten sind nützlich, um die Produktion zu verfolgen, während der digitale Zwilling die Bewertung von Fertigungsprozessen in Echtzeit unterstützt.
Die Verwendung einer Plattform, die alle drei Funktionen bietet, gibt Herstellern ein leistungsstarkes Werkzeug für die digitale Transformation und datengesteuerte Analysen an die Hand. Intelligente objektbasierte digitale Zwillingsplattformen nutzen 3D-Modelle, um genaue digitale Zwillinge zu erstellen, die die Erfassung digitaler Schatten unterstützen. Vollständig entwickelte digitale Zwillinge werden zu einer Drehscheibe für die kontinuierliche Analyse von Fertigungsprozessen, zur Fernüberwachung und zu einem Werkzeug für die Entscheidungsfindung.
Schlussfolgerung
Der digitale Zwilling verknüpft den gesamten Fertigungsprozess mit digitalen Modellen und Schattenbildern. Diese Digitalisierungskonzepte können zusammen angewendet werden, um Produktionsprozesse zu optimieren und jeden Aspekt des Produktionszyklus zu überwachen.