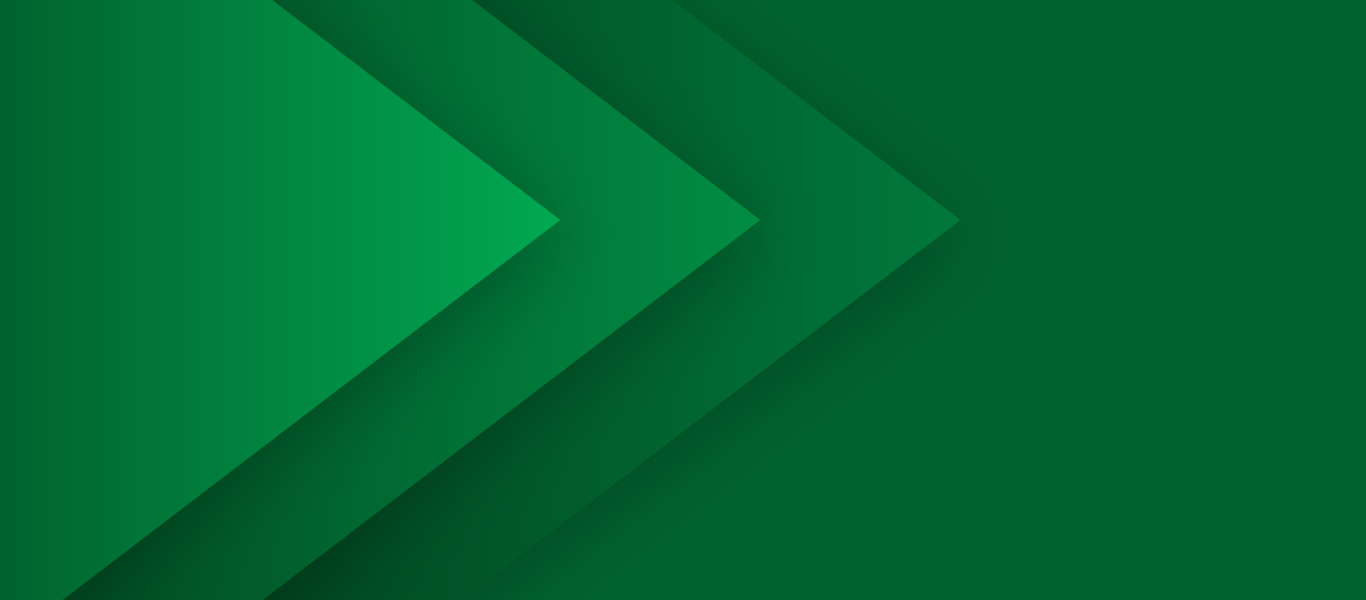
Der digitale Zwilling von Simio Process
Ein echter digitaler Zwilling, der Ihre Abläufe genau nachbildet, um sie zu entwerfen, zu analysieren und zu optimieren sowie aktuelle und künftige Leistungen vorherzusagen und vorzuschreiben
Was ist ein digitaler Zwilling?
Der Begriff „Digitaler Zwilling“ hat an Popularität gewonnen und ist zu einem Sammelbegriff für verschiedene digitale Modelle geworden. Der wahre Wert eines Digitalen Zwillings liegt jedoch in seiner Fähigkeit, alle Details der realen Betriebsprozesse, des Verhaltens und der Leistung genau abzubilden und dabei die Unternehmensdaten vollständig zu nutzen und nahtlos in die betrieblichen Systeme zu integrieren. Obwohl viele Anwendungen die Fähigkeiten des Digitalen Zwillings propagieren, treten bei der Implementierung oft erhebliche Herausforderungen auf – insbesondere bei der Anpassung an Prozessänderungen im laufenden Betrieb. Dieser kritische Fehler untergräbt oft die Lebensfähigkeit vieler Lösungen.
Simio hat eine agile Plattform entwickelt, die speziell auf die Anforderungen der Erstellung intelligenter, adaptiver Digitaler Zwillingsmodelle für Prozesse zugeschnitten ist, die das reale Verhalten von Betriebsprozessen präzise nachbilden und sich nahtlos in Unternehmensdaten und -systeme integrieren lassen. Die Simio-Plattform basiert auf unserer branchenführenden Technologie für diskrete Ereignissimulation und ist darauf ausgelegt, die digitale Transformation der Industrie 4.0 zu unterstützen. Von einer robusten Umgebung für das Entwerfen, Experimentieren, Analysieren und Optimieren von Simulationsmodellen zur Verbesserung der betrieblichen Effizienz und Entscheidungsunterstützung bis hin zum Einsatz eng integrierter Intelligent Adaptive Process Digital Twins, die einen vollständig autonomen Betrieb ermöglichen, bietet Simio den Anwendern eine nahtlose Reise durch das gesamte Kontinuum vom Entwurf bis zum Betrieb.
Intelligent
Die Kombination von diskreter Ereignissimulation und künstlicher Intelligenz schafft eine starke Synergie. Das Ergebnis sind Simio Process Digital Twins mit beispielloser Intelligenz, die in der Lage sind, blitzschnell hochoptimierte Lösungen für komplexe betriebliche Probleme zu entwickeln.
Anpassungsfähig
Simio Process Digital Twins sind in der Lage, sich automatisch an Änderungen der Unternehmensdaten anzupassen, z.B. an prozessbezogene Ressourcen, Materialien, Eigenschaften und Attribute, Produktrouten, Netzwerkänderungen, Stücklisten, Arbeitsanforderungen und -pläne, Wartungspläne und Produktmix.
Prozess
Mit einem Simio Process Digital Twin lassen sich Geschäftsprozesse in einer Vielzahl von Branchen modellieren, einschließlich detaillierter Fertigungsabläufe innerhalb einzelner Anlagen und über mehrere Standorte hinweg, Lagerabläufe und komplexe End-to-End-Lieferketten.
Digitaler Zwilling
Simio Process Digital Twins sind objektorientierte, datengenerierte und datengesteuerte Modelle der diskreten Ereignissimulation, die das physikalische Verhalten von Betriebsprozessen für Systeme beliebiger Größe und Komplexität genau nachbilden. Mit Simio Process Digital Twins können Benutzer die aktuelle und zukünftige Systemleistung entwerfen, optimieren, vorhersagen und vorschreiben.
Warum einen digitalen Zwilling für Simio-Prozesse entwickeln?
Die agile Plattform von Simio zur Entwicklung intelligenter adaptiver Process Digital Twins unterstützt eine Vielzahl von Arbeitsabläufen innerhalb eines digitalen Transformationsprozesses. Unabhängig vom gewählten Workstream erfordert die erfolgreiche Entwicklung von Process Digital Twins – unabhängig davon, ob es sich um die Modellierung aktueller oder zukünftiger betrieblicher Prozesse handelt – die Identifizierung, das Design, die Analyse und die Unterstützung bei der Ausführung von Operationen. Es gibt vier wichtige Gründe, die für den Einsatz der Simio-Plattform sowohl in der Design- und Analysephase als auch in der operativen Planungs- und Terminierungsphase Ihrer Unternehmenstransformation sprechen. Jeder dieser Anwendungsfälle bringt Ihrem Unternehmen in den verschiedenen Entwicklungs- und Implementierungsphasen Ihres Transformationsprojekts einen deutlichen Mehrwert.
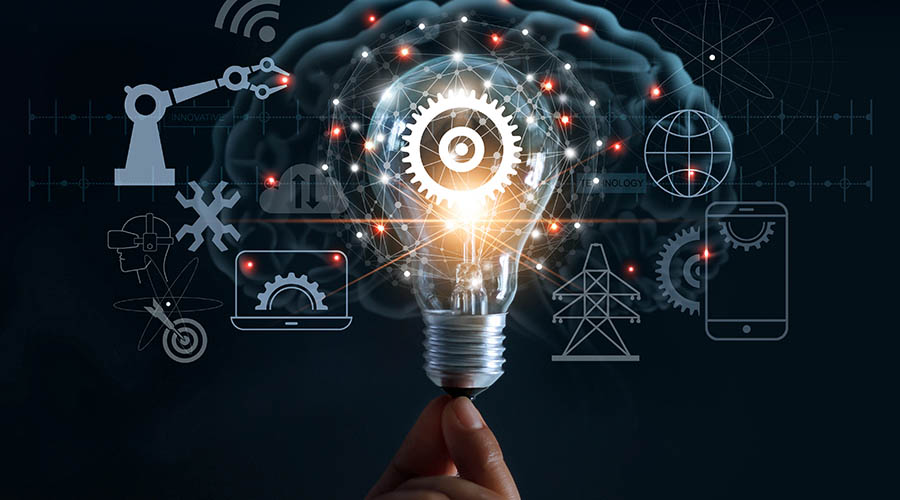
Hauptgrund Nr. 1
Wissensdatenbank
Entwickeln Sie eine zentralisierte Wissensbasis mit einem einzigen Bezugspunkt, indem Sie alle Systemeinschränkungen, Geschäftsregeln und detaillierte Logik in einem umfassenden Modell der diskreten Ereignissimulation des Prozesses erfassen. Dies gewährleistet die genaue Replikation komplexer, unternehmenskritischer Vorgänge an einem einzigen Standort oder in großen Systemen mit mehreren Standorten.
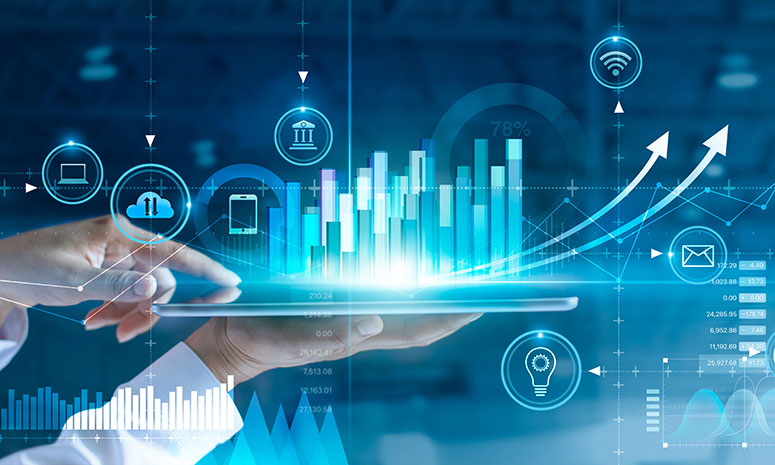
Hauptgrund #2
Leistungs-Benchmarking
Erstellen Sie einen Benchmark für die Prozessleistung, um die aktuelle Leistung zu bewerten und die zukünftige Leistung der Fabrik und der Lieferkette genau vorherzusagen. Dies ermöglicht die Validierung von Änderungen wie Automatisierung, neue Anlagen und Auffüllungsstrategien wie die bedarfsgesteuerte Materialbedarfsplanung (DDMRP).
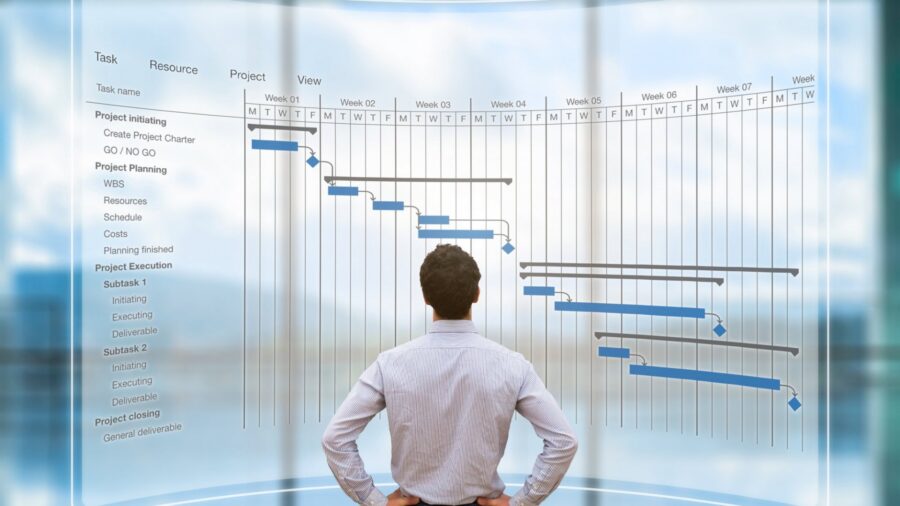
Hauptgrund #3
Plan & Zeitplan
Erstellen Sie realisierbare Pläne und Zeitpläne für die Ausführung in der Werkstatt, im Lager, in der Fabrik und in der Lieferkette über alle relevanten Zeitspannen hinweg, indem Sie sicherstellen, dass die Vorgänge in Bezug auf Ressourcenkapazität, Material und Zeitplan machbar sind. Dies ermöglicht eine völlig autonome Ausführung.
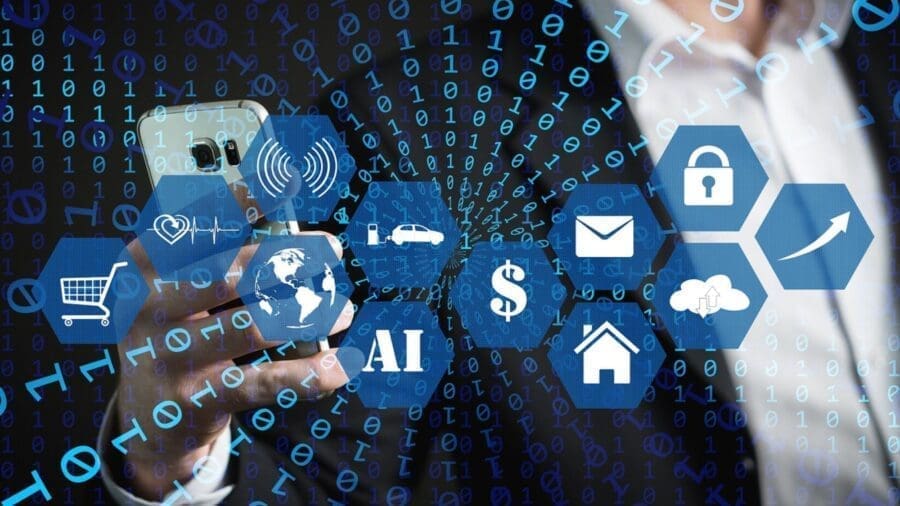
Hauptgrund #4
Referenzmodell
Pflegen Sie einen adaptiven, datengenerierten und datengesteuerten Intelligent Adaptive Process Digital Twin, um ein digitales Referenzmodell des Prozesses auf dem aktuellen Stand zu gewährleisten. Dies ermöglicht die Bestimmung der zukünftigen Fabrik- und Lieferkettenleistung für laufende und neue Transformationsprojekte und Investitionsentscheidungen.
Operativer Wert eines digitalen Zwillings von Simio Process
Bewerten Sie Alternativen und analysieren Sie die Auswirkungen laufender Änderungen
- Operative Richtlinien oder Prozessänderungen
- Einführung neuer Produkte oder Materialien
- Hinzufügen von Produktionskapazitäten oder Automatisierung, wie z.B. neue Anlagen, Werkzeuge, Roboter und AMRs
- Anpassung der Anforderungen an die Fähigkeiten der Mitarbeiter, der Schichtmuster und des Personalbestands
- Neugestaltung von Anlagenlayouts und Reorganisation von Arbeitsabläufen
- Materialverfügbarkeit und Bestandsrichtlinien, einschließlich JIT, Kanban und DDMRP
Erstellen Sie umsetzbare und realisierbare Pläne und Zeitpläne
- Erhöhen Sie den Durchsatz und die termingerechte Lieferung, indem Sie die Produktion über den gesamten Prozess hinweg synchronisieren.
- Reduzieren Sie die Produktionskosten, einschließlich der Kosten für Material, Arbeit, Strafen, Energie und unfertige Erzeugnisse
- Verbessern Sie die Einhaltung von Produktionsplänen, die Erfüllungsrate von Aufträgen und das Serviceniveau.
- Optimieren Sie die Abläufe und verbessern Sie die Effizienz durch autonome Abläufe, die durch nahezu Echtzeit-Planung und Orchestrierung unterstützt werden.
- Optimierte Pläne und Zeitpläne durch Training, Tests und Einsatz von KI
Integrierte Daten- und Workflow-Management-Funktionen
- Browserbasierter Zugriff für mehrere Benutzer mit anpassbaren Berechtigungen, Rollen, Eigenschaften und Standorten
- Dynamische Integration über Datenverbindungen, einschließlich Web APIs
- Erzeugt und gesteuert durch direkte Integration oder Cloud-basierte Unternehmensdaten-Pipelines
- Schnittstelle zu unterstützenden Anwendungen wie MES, ML/AI/NN, Tableau und Power BI
- Kontrollieren und verteilen Sie die Modellergebnisse strukturiert an die Teams
Schlüsselkomponenten eines digitalen Zwillings von Simio Process
Datengeneriert & -gesteuert
Modelle werden anhand von Unternehmensdaten erstellt und gesteuert, einschließlich Ressourcen, Materialstamm, Stücklisten, Arbeitsplänen und aktuellem Status. Dies ermöglicht die Identifizierung und Validierung von Schlüsselaspekten der Unternehmensdaten, wie Granularität, Qualität, Korrelation, Geschwindigkeit und Verfügbarkeit.
Intelligente Objekte
Modelle werden aus intelligenten Objekten erstellt, die Systemkomponenten wie Maschinen, Transporter, Roboter und Arbeiter darstellen, die sich alle gegenseitig beeinflussen können und KI/NN/ML zur Prozessoptimierung einsetzen.
Einschränkungsmodelle
Constraint-Modelle umfassen alle physischen Beschränkungen (z.B. Ausrüstung, Arbeiter, Transport, Material), Geschäftsregeln (z.B. MOQ, Arbeitsrichtlinien, Bestandsrichtlinien) und detaillierte Entscheidungslogik (einschließlich „Stammeswissen“ aus der Produktion), um sicherzustellen, dass das Modell das Verhalten des physischen Prozesses genau nachbildet.
Ereignisgesteuert
Die Technologie der diskreten ereignisgesteuerten Simulation simuliert mit Hilfe des Ereigniskalenders in der Zukunft, um alle zukünftigen Aufgaben und Materialentscheidungen auf der Ausführungszeitachse zu synchronisieren. Dies gewährleistet die Durchführbarkeit des Zeitplans in der Werkstatt für die bedienergesteuerte Ausführung oder sogar die direkte Orchestrierung in hochautomatisierten Umgebungen.
Stochastisch
Die Digital Twin-Modelle von Simio Process enthalten Zufallsfaktoren, die für die Bewertung von Schwankungen wie Maschinenausfällen und verspäteten Materialeingängen entscheidend sind. Diese Fähigkeit ermöglicht eine Risikobewertung von Plänen und Zeitplänen, um proaktive Maßnahmen zu unterstützen und die Wahrscheinlichkeit zu erhöhen, dass Leistungsziele wie die pünktliche Lieferung erreicht werden.
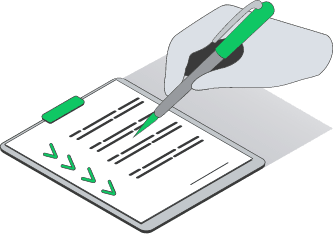
Vorlagen
Simio bietet eine Bibliothek anwendungsspezifischer Vorlagen mit vordefinierten Objekten, Prozesslogik und Datenschemata, um die Entwicklung von Process Digital Twin-Modellen für komplexe betriebliche Prozesse zu beschleunigen. Jede Vorlage ist anpassbar, um die benutzerspezifischen Anforderungen zu erfüllen.
Erstellen eines digitalen Zwillings von Simio Process
Die Entwicklung eines Process Digital Twin-Modells umfasst fünf Schlüsselphasen: angefangen bei der Dokumentation aller Prozessschritte über die Erstellung von Simulationsmodellen bis hin zur Integration des Process Digital Twin-Modells mit den Live-Unternehmenssystemen und relevanten Datenquellen.
Schritt 1: Spezifikation der Anforderungen
Dokumentieren Sie alle Prozessschritte und Benutzeranforderungen, einschließlich physischer Einschränkungen, Geschäftsregeln und detaillierter Entscheidungslogik, um eine umfassende funktionale Anforderungsspezifikation zu erstellen, die den Entwicklungsprozess effektiv einteilt und verwaltet.
Schritt 2: Datenüberprüfung
Prüfen Sie alle relevanten Unternehmensdatenquellen, einschließlich manuell gepflegter Excel- und CSV-Dateien, auf die erforderlichen statischen und dynamischen Daten, um das Process Digital Twin-Modell zu erstellen und zu betreiben.
Schritt 3: Entwicklung einer Datenpipeline
Entwickeln Sie die erforderliche Datenpipeline, um den Datenfeed zu liefern, der das Process Digital Twin-Modell generiert und antreibt, indem Sie es direkt in die Unternehmenssysteme integrieren oder eine Cloud-basierte Dateninfrastruktur nutzen.
Schritt 4: Modellentwicklung
Entwickeln Sie ein detailliertes, validiertes und verifiziertes datengesteuertes, objektorientiertes, simulationsbasiertes Process Digital Twin-Modell, um sowohl Offline- als auch Online-Anwendungsfälle (z.B. Simulation, Design, Scheduling, Orchestrierung) zu unterstützen, wie in der Spezifikation der funktionalen Anforderungen angegeben.
Schritt 5: Datenintegration
Integrieren Sie das Process Digital Twin-Modell mit Live-Unternehmensdaten-Feeds (z.B. ERP, MES, PM, IoT) für die Offline- und Online-Nutzung oder für die Entscheidungsunterstützung und -ausführung in nahezu Echtzeit in prädiktiven und präskriptiven Anwendungen.