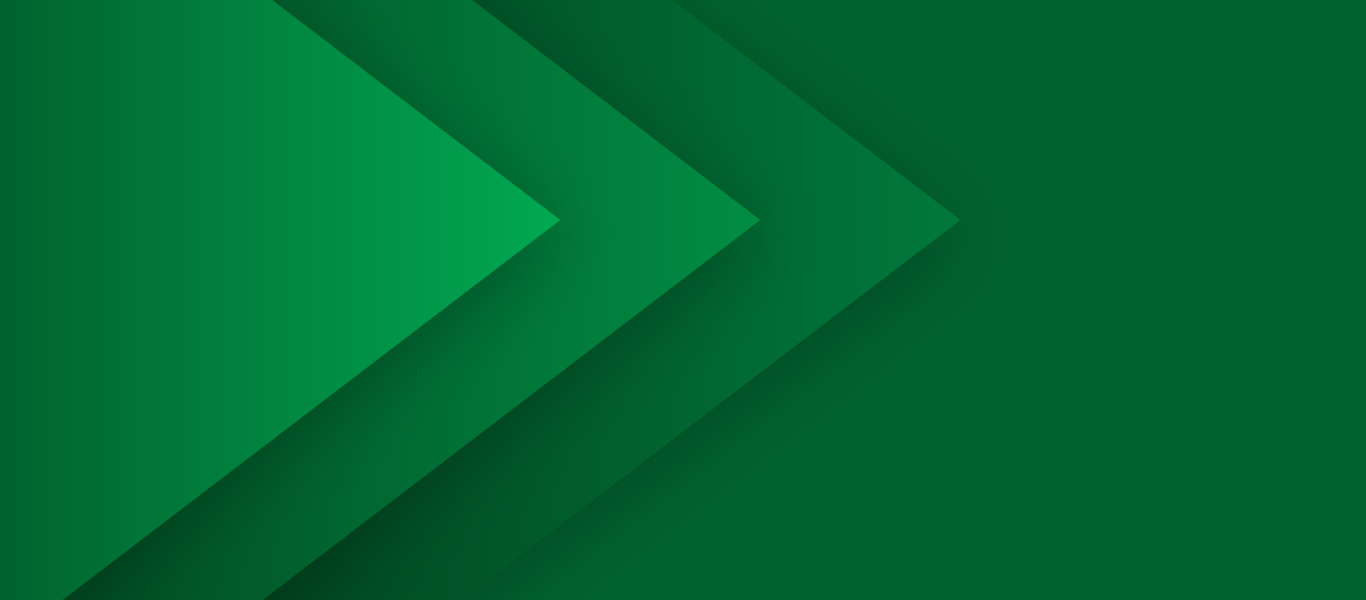
DDMRP Digital Twin Software
Transforming manufacturing and supply chain planning by seamlessly integrating DDMRP with Simio Intelligent Adaptive Process Digital Twins, resulting in optimized demand-driven execution
Simio has been certified by the Demand Driven Institute (DDI) for all three levels of software compliance to be used for Demand Driven Material Requirements Planning (DDMRP), Demand Driven Operating Model (DDOM) and Demand Driven Sales & Operations Planning (DDS&OP)
What is DDMRP?
Demand Driven Material Requirements Planning (DDMRP) is a formal multi-echelon planning and execution methodology designed to protect and promote the flow of relevant information in volatile, uncertain, complex, and ambiguous (VUCA) supply chain environments. DDMRP was developed through two decades of research and application across a wide range of industrial segments to address the evolving supply chain landscape and the challenges of using conventional MRP in that landscape. DDMRP is the strategic positioning and sizing of decoupling buffer stocks to manage customer lead times while reducing the impact of variability and improving the overall flow of product and information through the end-to-end network. DDMRP enables a flow-based operating model versus a pure cost-based operating model currently deployed at most businesses. DDMRP will eliminate the overall bullwhip effect by enabling synchronized flow of material and information across the supply chain to meet demand.
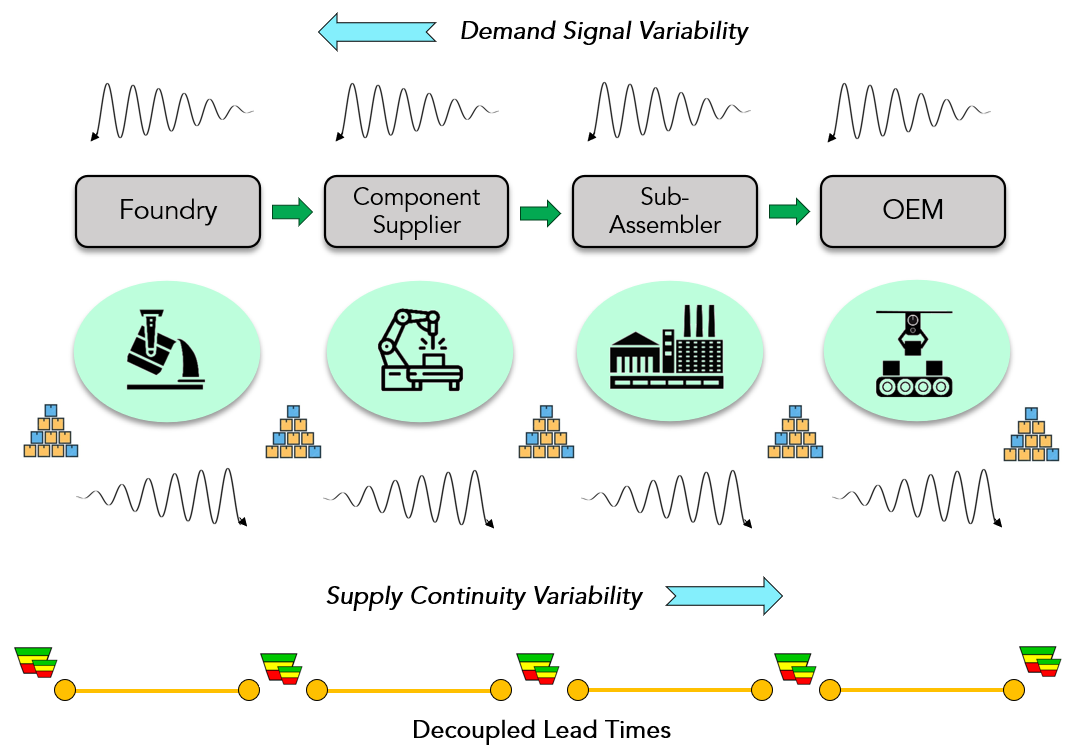
DDMRP Combines Three Key Industry Drivers
- Material Requirements Planning (MRP) and Distribution Requirements Planning (DRP)
- Pull and visibility emphasis on Lean and Theory of Constraints
- Variability reduction emphasis of Six Sigma
DDMRP Operates on Three Fundamental Assumptions
- Demand, except for explicit sales orders, is generally unknown and subject to change.
- The gap between cumulative lead times and customer tolerance times forces the holding of stock at key points to compress response times.
- There will be variability in execution.
Evolution Not Revolution
- For experienced planning practitioners, DDMRP is not about forgetting or abandoning what they know.
- DDMRP builds on that foundation by incorporating established principles to address the needs of modern supply chains.
DDMRP: A Proven Approach for Achieving Significant Gains in Network Performance
DDMRP Powered by Simio
An Intelligent Adaptive Process Digital Twin powered by Simio’s Discrete Event Simulation technology is an ideal platform for the design, test, optimization, and execution of DDMRP as a replenishment methodology to manage material flow that includes order generation for procurement, manufacturing orders, and stock transfers. Simio’s support of DDMRP includes features and functions specifically developed to support the accurate modeling of any DDMRP replenishment options as part of a single or multi-site manufacturing facilities and complex supply chains.
Accelerate Development of Manufacturing Supply Chain Models
- Predefined relational data tables to manage the inputs into Simio Process Digital Twin models take the guesswork out of setup.
- A customizable library tailored to supply chain modeling accelerates Simio Process Digital Twin development by including objects representing physical sites in the supply chain network — such as retail, distribution, manufacturing, and supplier sites — as well as objects for modeling transportation modes for delivering supply orders.
- DDMRP calculators in Simio determine key inputs for sizing strategic inventory buffers and generating supply orders, include average daily usage values, decoupled lead times, buffer red, yellow, and green zone sizes, and qualified spike demand values for net flow position calculations.
Tailored Features for Generating Plans & Analyzing Performance
- Demand-Driven MRP replenishment policy is applied at each strategic inventory buffer to determine when to generate a supply order and to recommend the appropriate order quantity.
- Process Digital Twin models include detailed warehouse, factory, supplier, and delivery-related objects, sourcing policies, and decision logic needed to exactly match real-world order fulfillment processes.
- Customized and configurable forward-looking DDMRP-specific dashboards and reports provide expert insights into operational performance — prebuilt dashboards include:
- DDMRP Planning & Run Charts
- Resource & Warehouse Utilization
- Production & Deliver Schedules
- KPIs, Material Consumption
- Constraint Analysis
- Inventory & Operating Cost
Simulation is a Game-Changer
Imagine managing your manufacturing supply chain with real-time insights into what’s working and what isn’t. Picture having detailed reports that offer a clear understanding of your supply chain’s performance, paired with a low-risk environment for experimenting with changes. Envision designing a supply chain that generates operational plans achieving unmatched performance and efficiency. A detailed Process Digital Twin of your manufacturing supply chain, powered by Simio’s Discrete Event Simulation platform and the proven DDMRP replenishment methodology, can deliver exactly that!
The effectiveness of this approach lies in a powerful Simio simulation engine that operates a detailed Process Digital Twin, replicating the entire flow of information and materials across your supply chain — from generating supply orders with Demand-Driven MRP, through Sourcing, then Demand-Driven Scheduling and Execution, to Final Delivery.
Steps for simulating a Process Digital Twin of your Manufacturing Supply Chain:
Step 1: Supply Order
For supply order generation using DDMRP, the inventory position of each strategic inventory buffer is monitored and updated using key inputs such as Buffer Zone Sizes and Qualified Spike Demand.
Step 2: Inventory Reviews
Continuous or periodic inventory reviews (e.g., daily) are conducted using the DDMRP replenishment policy, which is applied at each review to assess the inventory’s Net Flow position and Green Zone, determining when to reorder and the appropriate order quantity.
Step 3: Sourcing Policy
Inventory sourcing policies determine whether the supply order is a manufacturing, purchase, or stock transfer order and specify the site (or sites) for sending the order. Sourcing policies also apply supplier-dependent order modifiers to enforce minimum, maximum, or fixed order size requirements.
Step 4: Sourcing Decisions
Sourcing decisions for supply orders are made at the time an order is generated as a result of the DDMRP replenishment policy. This enables both demand-driven replenishment and dynamic sourcing strategies based on the current system state. An AI-based Neural Network-driven approach can also be included in the Simio simulation to enhance sourcing decisions based on dynamically predicted lead times.
Step 5: Fulfillment Prep
Once a sourcing decision is made a supply order is sent to the selected site, capturing the detailed resource and scheduling constraints, as well as the decision logic required for the order fulfillment process.
Step 6: Fulfillment
When a supply order is ready to ship, a model of the delivery process manages the material’s delivery to the destination inventory site. This model can range from a simple delay time to a complex description detailing transportation modes and shipment consolidation policies.
The image below illustrates the steps of the DDMRP methodology applied to a Manufacturing Supply Chain simulation
Supporting the Complete Demand Driven Methodology
Adaptive S&OP
Simio’s support for DDMRP allows you to configure, plan, schedule, and simulate a full Demand Driven Operating Model including DDMRP, Demand Driven Scheduling and Execution, and Adaptive Sales and Operations Planning for all relevant time ranges — operational, tactical and strategic.
Demand Driven Adaptive Enterprise
Simio’s Intelligent Adaptive Process Digital Twin technology is the key to unlocking the full potential of operationalizing the Demand Driven Adaptive Enterprise for end-to-end supply chain applications, from material supply through manufacturing to final distribution.
Demand Driven Distribution
Simio’s comprehensive support of Demand Driven methodologies includes Demand Driven Distribution Requirements Planning (DDDRP), which focuses on distribution-centric applications.
Simio DDMRP Expert Insights
The Simio Advantage
When implementing an innovative material management methodology like DDMRP, the ability to optimize the master settings of the Demand Driven Operating Model (DDOM) before actual operation is game-changing. This approach prevents costly mistakes and avoids the need for experimentation on your actual factory or supply chain. Leveraging Simio’s Intelligent Adaptive Process Digital Twin technology, with its comprehensive support for the complete lifecycle of demand driven planning, will ensure your network planning remains agile and effective in the most demanding VUCA environments.
Integrate with ERP software
Integrate with MES & IoT
Optimize future use of resources
Visualize the supply chain system
Support analysis of DDOM settings
Assess DDMRP implementation risk
Identify future data patterns & trends
Detect & address process constraints
Create operational replenishment orders
Learn More About DDMRP
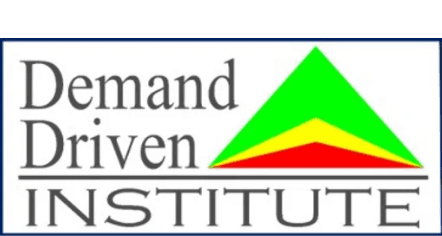
Demand Driven Institute (DDI)
Ptak and Smith then founded the Demand Driven Institute (DDI) as the governing body to advance and proliferate Demand Driven strategies and practices in the global industrial community by providing training, software & professional certifications.
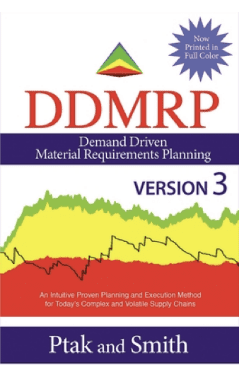
The DDMRP Book
The concept of Demand Driven Material Requirements Planning was introduced by Carol Ptak and Chad Smith in their first book: “Demand Driven Material Requirements Planning (DDMRP).” Visit the DDI website to see their library of Demand Driven publications.
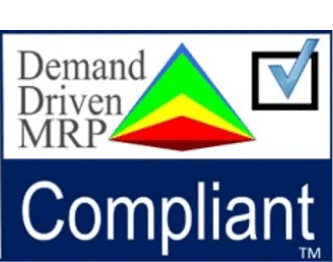
DDI Compliant Software
Simio has been certified by the Demand Driven Institute (DDI) for all three levels of software compliance to be used for Demand Driven Material Requirements Planning (DDMRP), Demand Driven Operating Model (DDOM) and Demand Driven Sales & Operations Planning (DDS&OP).