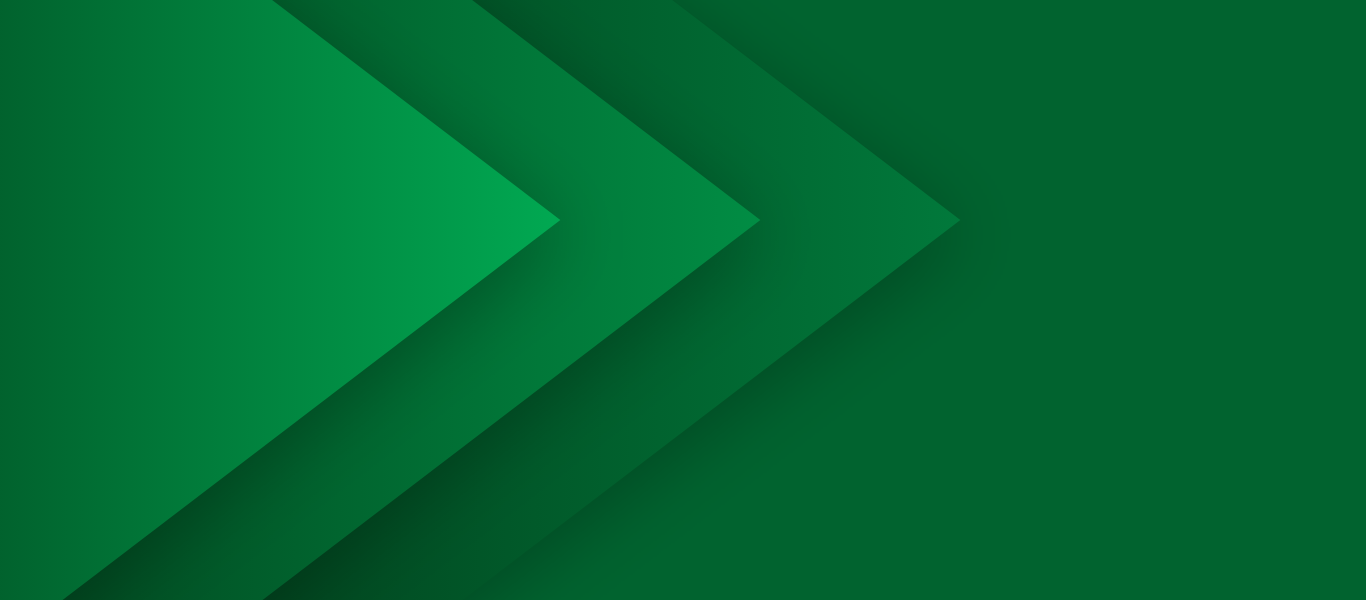
Simio Digital Twin Simulation Software
Deliver the solution you need no matter the challenge — solve complex operational problems with a Digital Twin powered by Simio Discrete Event Simulation
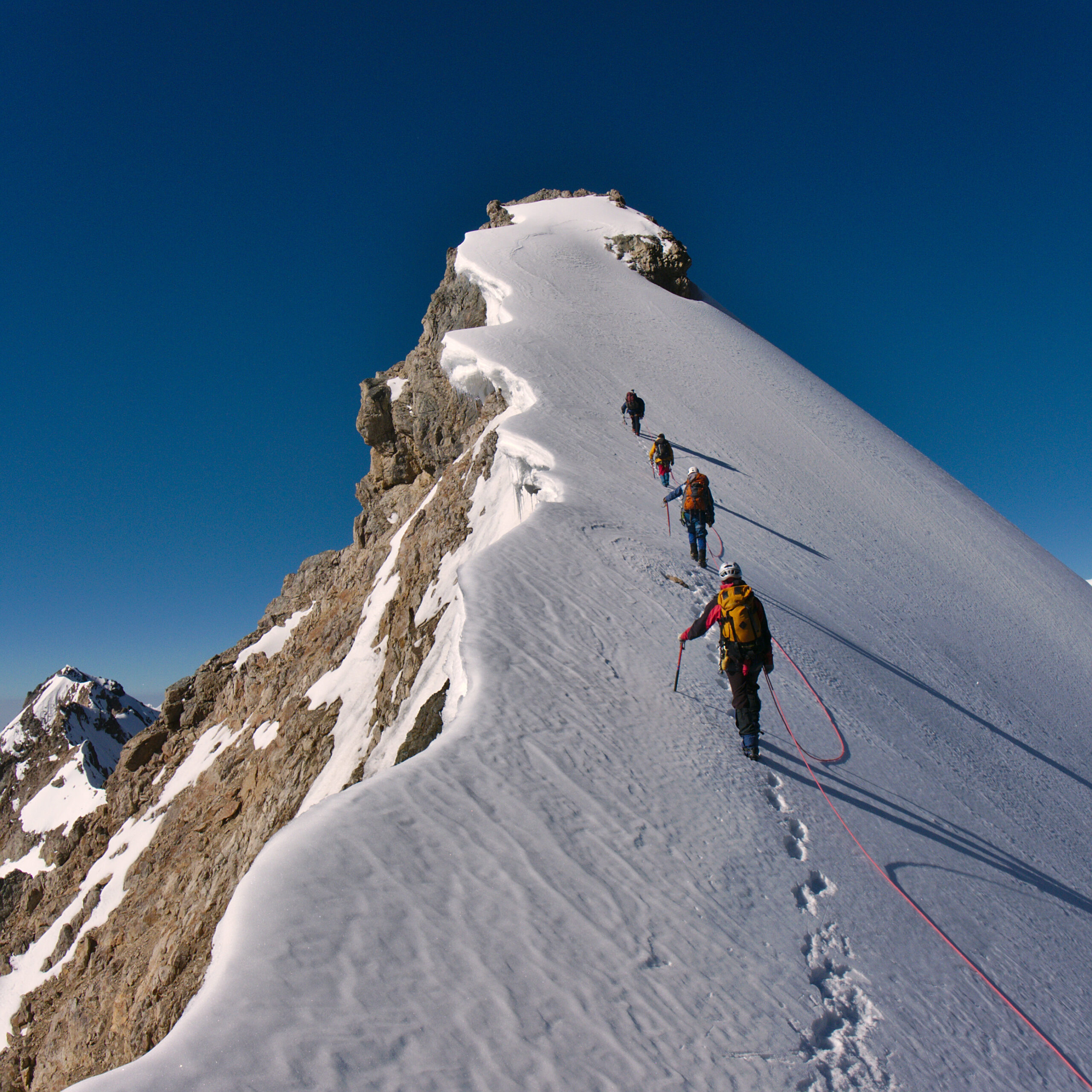
Simulation Pioneers
The development team behind Simio introduced their first commercially available Discrete Event Simulation product over 46 years ago. For five decades, this team has remained at the forefront of innovation, continuously advancing the science and art of Discrete Event Simulation. In 2009, Simio released a comprehensive, agile simulation platform that represents an evolutionary fourth-generation design — built from the ground up to be fully object-oriented, data-generated, data-driven, and highly adaptive — critical innovations for overcoming hurdles that hampered previous generations. Fast-forward to today, the Simio development team continues to build on this original architecture, advancing Simio’s capabilities. Time-tested and proven, the Simio Discrete Event Simulation Platform is fast, scalable, adaptive, and adept at fully utilizing enterprise data while seamlessly integrating with operational environments. Simio is taught in hundreds of universities, trusted by thousands of users, and deployed across a broad range of industries worldwide, including manufacturing, warehousing, logistics, supply chain, healthcare, mining, energy, transportation, foodservice, and consumer services.
The Simio Solution
Simio has developed an agile platform specifically designed to meet the demands of creating Intelligent Adaptive Process Digital Twin models that precisely replicate the real-world behavior of operational processes and integrate seamlessly with enterprise data and systems. Built on our industry-leading Discrete Event Simulation technology, the Simio platform is engineered to support Industry 4.0 digital transformation journeys. From a robust environment for designing, experimenting, analyzing, and optimizing simulation models to enhance operational efficiency and decision support, to the deployment of tightly integrated Intelligent Adaptive Process Digital Twins that enable fully autonomous lights-out operations, Simio equips and guides users through a seamless journey across the entire design-to-operate continuum.
Intelligent
Combining Discrete Event Simulation and AI creates a powerful synergy, resulting in Simio Process Digital Twins with unparalleled intelligence, capable of generating highly optimized solutions to complex operational problems with lightning-fast efficiency.
Adaptive
Simio Process Digital Twins have the ability to automatically adapt to changes in enterprise data such as process-related resources, materials, properties and attributes, product routings, network changes, bill of materials, labor requirements and schedules, maintenance schedules, and product mix.
Process
Business processes across a wide range of industries can be modeled with a Simio Process Digital Twin, including detailed manufacturing operations within single facilities and across multiple sites, warehouse operations, and complex end-to-end supply chains.
Digital Twin
Simio Process Digital Twins are object-oriented, data-generated, and data-driven Discrete Event Simulation models that accurately replicate the physical behavior of operational processes for systems of any size and complexity. Simio Process Digital Twins enable users to design, optimize, predict, and prescribe current and future system performance.
Strategic Application Use Cases
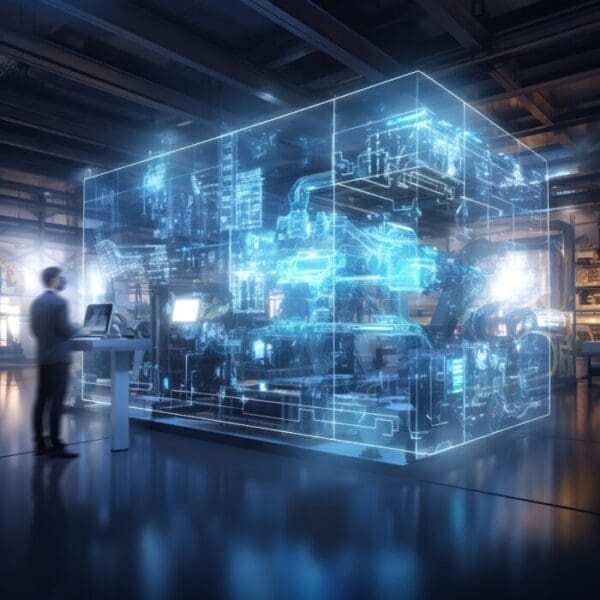
Game-Changing Workstreams
Develop a Clear Understanding
Design & Optimize
Predict & Prescribe
Knowledge Base
Operational Reference Model
Value of Process Digital Twins
Key Simio Platform Features
Simio’s architecture was designed from the ground up as an object-oriented, no-coding-required, state-of-the-art Discrete Event Simulation platform with native support for both simulation and scheduling applications. Simio pioneered this comprehensive platform for developing Intelligent Adaptive Process Digital Twins years before “Digital Twin” became a buzzword in the industry. Here are some key features that make Simio a best-in-class solution to help you solve operational challenges in your business.
Versatile
Simio Process Digital Twins can be used for both greenfield and brownfield applications, to design new or improve existing operational processes. They can simulate and analyze behavior occurring in the present or at any time in the future, and help understand a single mission-critical process or a complex network of processes that occur at a single site or across multiple sites.
Data-Generated
Simio provides a traditional point-and-click user interface alongside an intuitive data-generated, data-driven approach for developing and executing Process Digital Twin models. A data-driven approach accelerates model development for complex scenarios, facilitates model reuse, and supports the scaling of models to new sites, multi-site applications, and end-to-end supply chains.
Object-Oriented
Build comprehensive Process Digital Twin models without coding using intelligent out-of-the-box object libraries, and easily expand these libraries through subclassing and creating custom user- and industry-specific objects. Any Simio model can be used as an object in another Simio model, facilitating reuse and hierarchical modeling.
Templates
Simio provides a library of application-specific templates containing predefined objects, process logic, and data schemas to jump-start Process Digital Twin model development for complex operational processes. Each template is customizable to fit any user-specific requirements.
AI-Enabled
Simio supports training, testing, and embedding Deep Neural Network agents into Process Digital Twin models, along with bidirectional interaction with Machine Learning algorithms to enhance model intelligence, optimize results, and reduce execution run times. Simio also supports the import and direct use of Machine Learning regression models in the ONNX format.
Scalable Deployments
Simio offers a range of deployment options, including cloud-based solutions, to broaden the reach and utility of Process Digital Twins for stakeholders across the enterprise — both internal and external — for applications such as Simulation, Planning & Scheduling, and Shop Floor Orchestration.
Integrations
Simio’s architecture is built on an extensive integration framework that includes bidirectional database connectors, support for Excel and CSV, Web APIs for cloud, enterprise system, and IoT device integrations, and support for C#, Python, and SQL.
3D Visualization
Simio Process Digital Twin models are true digital twins in both operational accuracy and visual detail. With 3D, GIS, and VR capabilities, users have powerful visualization features at their disposal, in addition to extensive data reporting, Gantt charts, and dashboards to validate model behavior and showcase operational performance.
User Feedback
Broad Industry Adoption
From commercial businesses and government agencies to academic institutions, across every industry and business size, organizations grappling with complex operational challenges can harness the versatile capabilities of Simio’s Discrete Event Simulation software. Simio’s comprehensive application workstreams span Simulation & Analysis, Process Design & Optimization, Planning & Scheduling, Shop Floor Orchestration, and Design-to-Operate Process Management. Industries using Simio’s best-in-class simulation software include: