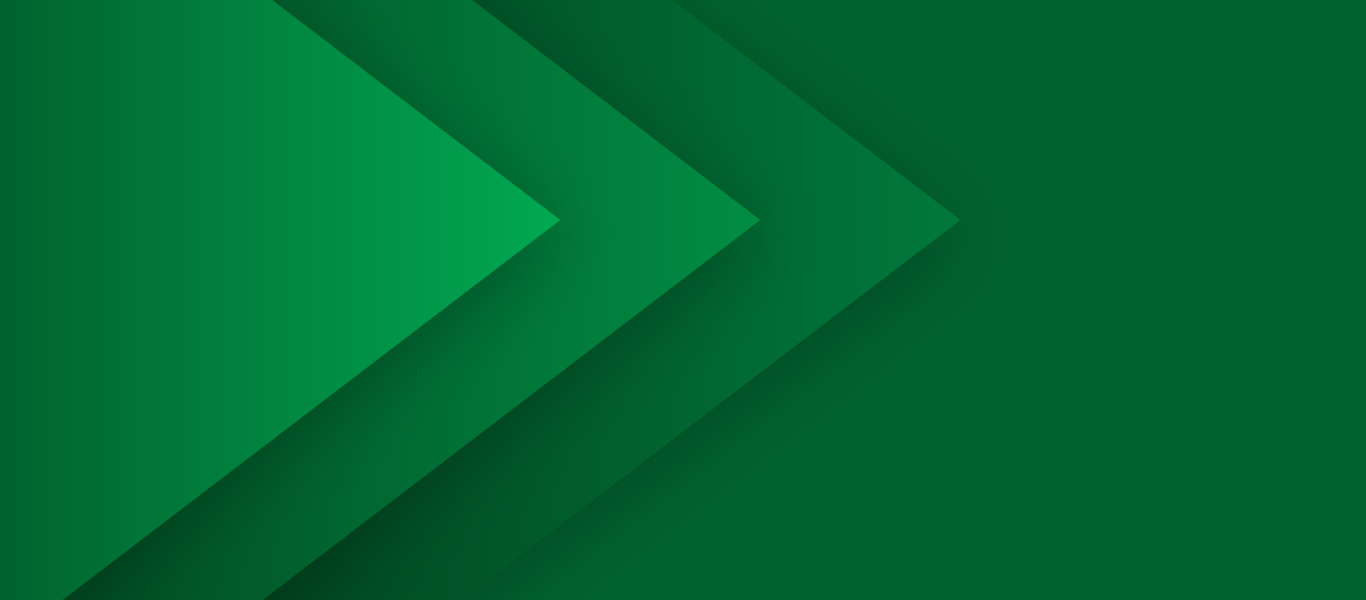
Advanced Planning and Scheduling Software (APS)
A Simio Discrete Event Simulation-powered APS solution delivering real-time, synchronized, risk-based, dynamic production planning and scheduling that is always feasible and always optimized
Simio Advanced Planning and Scheduling (APS Software)
Simio Discrete Event Simulation Powered Advanced Planning and Scheduling (APS) leverages Intelligent Adaptive Process Digital Twin technology to perform real-time, synchronized, risk-based dynamic scheduling. This state-of-the-art approach to a historically challenging undertaking, results in feasible plans and schedules for manufacturing, warehouse, and supply chain execution across all relevant time ranges, ensuring that all operations are resource-capacity, material, and timeline feasible.
Why Simio for APS?
Using Simio Intelligent Adaptive Process Digital Twins to perform Advanced Planning and Scheduling (APS) enables real-time analysis, helping you make decisions that ensure your business meets its commitments by effectively managing unexpected disruptive events such as machinery breakdowns, material shortages, and unplanned orders. Simio’s agile platform for developing Intelligent Adaptive Process Digital Twins allows you to easily build data-generated simulation models without coding, fully capturing detailed constraints, business rules, and decision logic within your system. Discrete events and flow processes are depicted within the same model, and realistic 3D animation provides an engaging visual representation. With powerful AI-enabled optimization at your fingertips, you can freely experiment with operational scenarios, facilitating detailed what-if analyses that result in comprehensive insights into system performance, thereby empowering your teams to make informed decisions and maximize business KPIs.
Absolute Feasibility
- Simio Advanced Planning and Scheduling operates with a Discrete Event Simulation-based, resource-task-oriented architecture that ensures material and planning/scheduling timeline feasibility.
- Process Digital Twins incorporate digital replicas of the processes, equipment, people, and devices that make up factories, warehouses, and supply chains.
- System resources in Process Digital Twins not only have busy, idle, and off-shift states, but they are also modeled as objects that exhibit behavior and move around the system. These resources interact with other objects to fully replicate the behavior and detailed constraints of real-world operating environments.
- Production scheduling decisions are made at the exact event time when resources and materials are required. Dynamic dispatching rules and detailed process logic are then applied to decide the next order to process and which resources to use.
- Absolute operational feasibility is ensured by fully synchronizing all material and resource requirements with the actual event timeline for each operation.
Accurate & Verifiable Results
- Simio Advanced Planning and Scheduling is a comprehensive solution that ensures predicted performance results are accurate and verifiable through the application of Process Digital Twins that incorporate all physical constraints, business rules, operating procedures, safety protocols, and operational decision logic required to effectively operate factories, warehouses, and supply chains.
- Eliminate unplanned downtime due to preventive maintenance and operational requirements by planning for and expecting everything.
- Improve throughput while maintaining schedule feasibility by making decisions based on expert insights into mission-critical factors such as resource utilization and material availability.
Fast Runtimes
- Simio Advanced Planning and Scheduling operates with Process Digital Twins, powered by fast and efficient Discrete Event Simulation.
- Fast runtimes are critical for supporting dynamic re-planning/scheduling and scenario analysis.
- Generate plans/schedules as frequently as needed for any time horizon – next shift/day/week/month/year/years.
- Runs can be performed manually or designed to be fully automated and event-triggered.
- Simio Advanced Planning and Scheduling is capable of supporting large, complex single or multi-site manufacturing and warehouse facilities, as well as end-to-end supply chains.
Rapid Model Creation & Automatic Updates
- All Process Digital Twin model objects and properties are templatized to be data-generated and data-driven, enabling rapid model creation and minimizing long-term support requirements.
- Process Digital Twins automatically adapt to changes in enterprise data, ensuring rock-solid uptime and minimizing long-term maintenance.
- No coding is required to build Simio Process Digital Twins.
- Industry and company specific templates and libraries can easily be created.
Bucketless Planning
- Simio Advanced Planning and Scheduling supports bucketless planning, enabling the generation of rolling plans/schedules over any selected time horizon – next shift/day/week/month/year/years.
- Simulations of operating environments are always initialized with current work-in-progress and optimized related to tasks and materials on a continuous timeline to ensure continuity of the timeline across current operations between planning periods.
Fully Transparent “Glass Box” Approach
- Simio Advanced Planning and Scheduling employs a “Glass Box” approach to the process of generating plans/schedules — rather than a “Black Box” approach. This ensures that operational parameters and resource settings are clear to the business and can be tested, validated, and supported by operations.
- Plans/schedules are based on current resource loading across the system.
- A “Glass Box” approach means that business rules and operational decision logic can be easily understood, and therefore can be challenged and evaluated for their impact and value.
Key Features
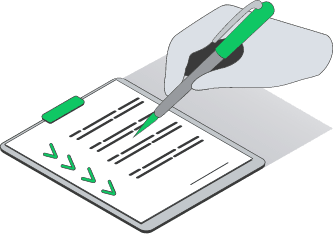
Risk-Based
Simio’s Advanced Planning and Scheduling engine is based on stochastic Discrete Event Simulation technology and operates on a comprehensive forward-looking view of expected production and delivery performance that accounts for risk associated with variability and random events to ensure that generated detailed operational schedules will meet expectations.
Data-Generated
Simio provides a traditional point-and-click user interface alongside an intuitive data-generated, data-driven approach for developing and executing Process Digital Twin models. A data-driven approach accelerates model development for complex scenarios, facilitates model reuse, and supports the scaling of models to new sites, multi-site applications, and end-to-end supply chains.
Scalable Deployments
Simio offers a range of deployment options, including cloud-based solutions, to broaden the reach and utility of Process Digital Twins for stakeholders across the enterprise — both internal and external — for applications such as Simulation, Planning & Scheduling, and Shop Floor Orchestration.
AI-Enabled
Simio supports training, testing, and embedding Deep Neural Network agents into Process Digital Twin models, along with bidirectional interaction with Machine Learning algorithms to enhance model intelligence, optimize results, and reduce execution run times. Simio also supports the import and direct use of Machine Learning regression models in the ONNX format.
Integrations
Simio’s architecture is built on an extensive integration framework that includes bidirectional database connectors, support for Excel and CSV, Web APIs for cloud, enterprise system, and IoT device integrations, and support for C#, Python, and SQL.
Object-Oriented
Build comprehensive Process Digital Twin models without coding using intelligent out-of-the-box object libraries, and easily expand these libraries through subclassing and creating custom user- and industry-specific objects. Any Simio model can be used as an object in another Simio model, facilitating reuse and hierarchical modeling.
Templates
Simio provides a library of application-specific templates containing predefined objects, process logic, and data schemas to jump-start Process Digital Twin model development for complex operational processes. Each template is customizable to fit any user-specific requirements.
3D Visualization
Simio Process Digital Twin models are true digital twins in both operational accuracy and visual detail. With 3D, GIS, and VR capabilities, users have powerful visualization features at their disposal, in addition to extensive data reporting, Gantt charts, and dashboards to validate model behavior and showcase operational performance.

Seamless Integration
Simio Advanced Planning and Scheduling features a robust toolkit of integration technologies that can seamlessly integrate a Process Digital Twin into the information systems managing your organization’s day-to-day operations. During the implementation phase the Process Digital Twin is configured to interface with both transactional information systems, which provide inputs on work orders, job routings, and staffing levels, and operational information systems, which track the status of resources and the transformation of raw materials into finished products. Interconnectivity between enterprise systems and the Process Digital Twin is a crucial step towards realizing the Smart Factory.
The Process Digital Twin model of a factory provides three key levels of decision support to ensure schedule feasibility while adhering to all system constraints:
- All physical constraints, including resources, material, and labor
- All pertinent business rules, such as MOQs, inventory policies, and labor policies
- The detailed decision logic on the shop floor, including equipment preferences and operator skills, often undocumented and considered part of the “tribal knowledge” of the operators
Cloud Deployment for Operational Use
Simio Advanced Planning and Scheduling can be operated on the desktop or deployed in the cloud for manufacturing, warehousing, and supply chain applications. A Simio cloud deployment offers significant flexibility and a broad range of features, enabling stakeholders across the enterprise to engage in planning and scheduling processes. Stakeholders can perform various activities, including:
- Experimenting with scenarios to improve KPI performance
- Analyzing predicted performance using detailed Gantt charts and dashboards
- Reviewing detailed schedules for upcoming shifts
- Gaining insights into how priority orders affect overall process efficiency and throughput
- Using long-term planning simulation results to assess the impact of sales forecasts on resources, inventory and the overall supply chain
- Evaluate the impact of integrating automation, such as AGVs/AMRs and robotics, to improve efficiency and throughput in the warehouse
Simio’s cloud deployment includes a versatile Web API that enables seamless integration with operational environments, enterprise applications, and data sources. Simio Advanced Planning and Scheduling supports automated schedule generation that includes the triggering of re-planning/scheduling based on real-time events happening anywhere across the system. Generated plans/schedules can be published for workers and exported to machines for execution. Additionally, detailed Gantt charts and dashboards can be created and made available for global viewing across the organization to enhance decision support.
Manufacturing, Warehousing & Supply Chain Challenges
Market Changes
Manufacturing & warehousing now serve as the response buffer for supply chains, adapting to leaner operations and responding to changing market behavior.
Customer Demands
Customers demand increased product variety and configurability with smaller minimum order quantities, and shorter product life cycles requiring manufacturing & warehousing agility.
Complex Supply Chains
Manufacturing facilities are managing increasingly complex operations with semi-flexible resources to enhance manufacturing agility, while also navigating more complex supply chains.
Time Constraints
End customers are demanding shorter lead times and greater transparency into supply chain performance, with expectations of predictable delivery times.
Knowledge Drain
Manufacturing companies are facing a knowledge drain, with approximately 25% of their employees aged 55 and over retiring at a rate of 10,000 per day.
Simio APS in Action
Initiatives
- Evaluate and understand the impact of operational policies on business and factory/warehouse/supply chain operations.
- Analyze the impact of new product or material introductions on current delivery and operational performance.
- Assess Return on Investment of increasing production capacity by adding new equipment and tooling.
- Design efficient and cost-effective labor policies by evaluating how worker skills and shift patterns impact factory and warehouse operations.
- Evaluate different inventory policies, such as JIT, Kanban, and DDMRP, to assess the impact on factory delivery performance under varying material availability.
- Facilitate autonomous operations with near-real time scheduling and orchestration.
Example Results
- 20% Increase in throughput realized by synchronizing all materials & resources with actual event timeline of each operation across entire production process.
- 16% Reduction in cost of production achieved by optimizing efficiency of resources, limiting expediting costs, and eliminating missed delivery penalties.
- 12% Increase in On-Time Delivery performance achieved across all SKUs in complex high-volume production environment.
- 15% Reduction in inventory and Work-in-Process realized due to improved process synchronization.
- 10% reduction in labor costs achieved through improved shift scheduling effectiveness and reduced overtime expenses.
- 25% Reduction in manufacturing lead times realized due to improved effectiveness of resource and labor synchronization and changeovers.