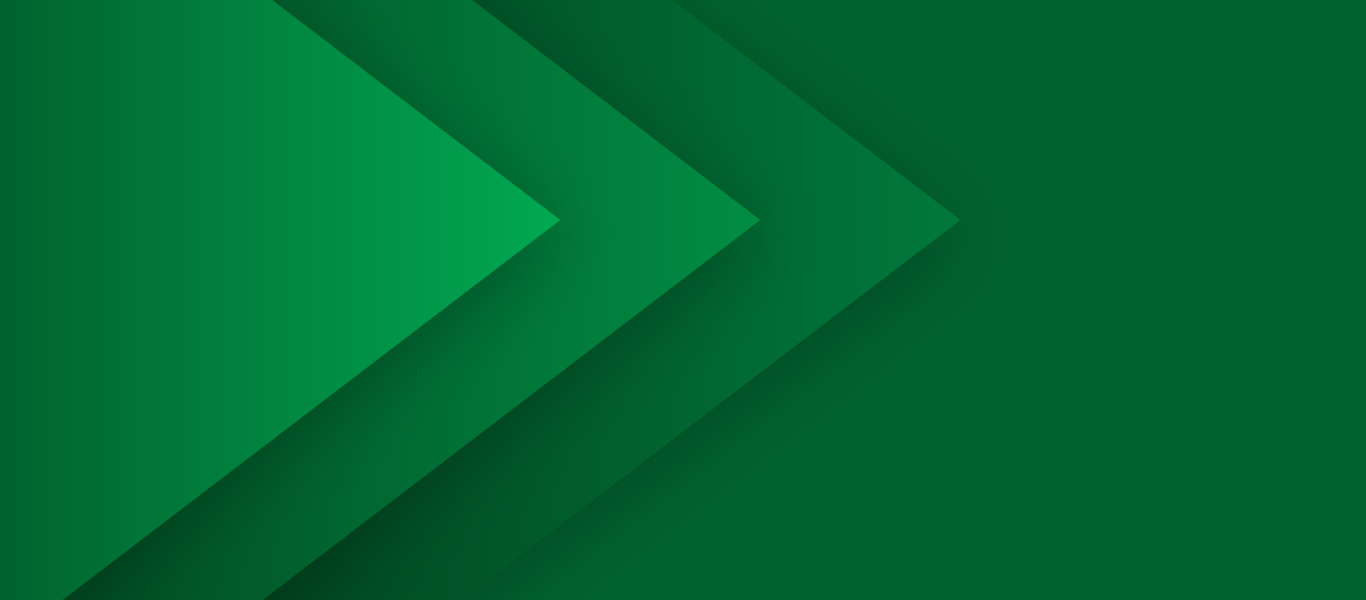
Simio Data & Integration Framework
The most flexible data and integration framework in the Discrete Event Simulation industry
Simio Key Data & Integration Differentiators
Simio is built from the ground up as an agile platform for developing Discrete Event Simulation-based Adaptive Process Digital Twins, with a strong emphasis on seamless data integration and streamlined automation across enterprise systems and other essential data sources. This focus has shaped Simio’s data and modeling features to support rapid model development that automatically adapts to dynamic data input.
Data Flexibility
- Simio is built on an efficient, ultra-fast in-memory relational database that can be fully configured to match the schema of any external data source, providing unparalleled flexibility.
Open Architecture
- Simio’s open architecture features an extensive, fully configurable set of data connectors that support the streamlined import of transactional and operational data from any external source.
Data-Generated & Data-Driven
- Simio provides a traditional point-and-click user interface alongside an intuitive data-generated, data-driven approach for developing and executing Process Digital Twin simulation models.
- A data-driven approach accelerates model development for complex scenarios, facilitating model reuse, and supports the scaling of models to new sites, multi-site applications, and end-to-end supply chains.
Rapid Model Creation & Automatic Updates
- All Process Digital Twin model objects and properties are templatized to be data-generated and data-driven, enabling rapid model creation and minimizing long-term support requirements.
- Process Digital Twins automatically adapt to changes in enterprise data, ensuring rock-solid uptime and minimizing long-term maintenance.
- No coding is required to build Simio Process Digital Twins.
- Industry and company specific templates and libraries can easily be created.
Fast Runtimes
- Simio’s simulation engine is designed to run efficiently and quickly, no matter the model size.
- Fast runtimes are essential to unlock the full potential of limitless experimentation and scenario analysis.
- Simulation runs can be performed manually or designed to be fully automated and event-triggered.
- Simio Discrete Event Simulation is capable of supporting Process Digital Twin models of large, complex operational environments such as single or multi-site manufacturing and warehouse facilities, as well as end-to-end supply chains.
Data & Integration Features
Excel/CSV
Data connectors enable temporary or user-specific systems to access operator-specific data maintained in Excel or CSV files, snapshots from custom systems, and data recorded in Excel during operations.
External Databases
Data connectors for database applications such as SQL Server and Oracle facilitate direct integration with databases used for staging and data transformation, as well as direct access to enterprise-level, application-specific data sources.
APIs & Web Services
Out-of-the box Simio APIs or web services can be used to integrate with MES systems such as AVEVA and Tulip to access dynamic process-related data for initializing a Process Digital Twin with the current factory status and provide execution data, such as task lists and start times, back to MES systems.
External Tools & Devices
Utilize industry-standard applications such as PTC Kepware IoT Gateway and HighByte Intelligence Hub to directly connect to IoT devices, external solvers, and AI-based applications or algorithms for dynamic real-time inputs and optimization during simulation runtime.
Cloud-Based Platforms
Simio Web APIs facilitate integration with cloud-based data sources such as AWS, Azure, and Google Cloud, which hold mission-critical data published by underlying enterprise systems, as well as direct integration with Enterprise Resource and Supply Chain Planning systems (ERP/SCP) such as SAP S/4HANA, OMP, Kinaxis, Oracle, and Microsoft Dynamics.
Integration Approaches
To facilitate integration with enterprise systems such as Enterprise Resource Planning (ERP), Manufacturing Execution Systems (MES), Supply Chain Planning (SCP), and Preventative Maintenance (PM), Simio developed two implementation methodologies tailored to existing customer IT infrastructure and preferences. These methodologies support both Indirect (“Push”) and Direct (“Pull”) approaches, catering to the customer’s specific requirements and data maturity levels.
Direct Integration Approach (PULL)
Leveraging the flexibility of Simio’s Web API data connector, Simio can initiate a PULL operation from data systems based on timed events or user input prior to executing a simulation run, ensuring the use of the latest information. However, the downside of using a PULL operation is the potential high demand it places on IT infrastructure and target data systems, depending on the timing of the PULL event.
Direct Integration Workflow:
- Simio initiates the integration workflow by sending a GET request to a middleware application associated with an ERP, MES, SCP, or IoT system.
- Upon receiving the initiated call from Simio, the middleware application acts as a web messenger, forwarding the request to the ERP/MES/SCP/IoT system, which then generates the necessary data and sends it back to the middleware application.
- The middleware application sends the message to Simio formatted in JSON or XML, which is stored in Simio’s memory-resident relational database using an XSLT (v1.0) stylesheet for data mapping and translation.
- Upon completion of the simulation run, Simio leverages full bi-directional integration capabilities, allowing it to push (POST) the scheduling information back to the middleware application and subsequently to the source ERP/MES/SCP/IoT system.
Indirect Integration Approach (PUSH)
Utilizing an additional persistence data layer, Simio supports a PUSH approach for integration with existing enterprise systems. Updates from enterprise systems are pushed via a middleware application to the staging database (persistence layer) driving Simio, ensuring data is available for simulation runs and generating production schedules. This method is ideal for routine daily or weekly scheduling and, unlike the PULL approach, minimizes the load on IT infrastructure.
Indirect Integration Workflow
- Initiated by a job scheduling process or trigger, the ERP/MES/SCP/IoT system generates messages that are sent to a middleware application.
- Before forwarding messages to Simio, the middleware application may need to perform transformation mappings based on the intended use of the data to align with Simio’s model table requirements. The updated messages are then transferred to the staging database utilizing the middleware database adapters or XML files.
- Simio then pulls the table data from the database using a data connector, updating the Simio in-memory tables.
- Upon completion of the simulation run, Simio leverages full bi-directional integration capabilities, allowing it to push scheduling information back to the staging area for access by the middleware application and subsequently the source ERP/MES/SCP/IoT system.
Data Detail and Speed
The state of your business’s data integrity, the level of detail contained in the data, the correlation between systems, and the speed at which data can be updated and made available are crucial for determining how granular a Simio Process Digital Twin can be modeled. These factors also affect the frequency with which a business can create new schedules for execution or experiments to support decision-making.
Level of Detail
The level of detail available in the data – such as part- and machine-specific routings, rather than just work cell and product family routings – determines the detail level of the model.
- Example: To model individual workers and their skills, the Simio Process Digital Twin requires the current and specific work schedule for each worker, along with up-to-date skills matrices.
Data Speed
Data speed refers to how quickly the Simio Process Digital Twin can be updated and re-run to provide the most current results for execution or decision-making.
- Example: With a traditional ERP system that batch-processes WIP inventory overnight, the Simio Process Digital Twin is limited in how frequently it can be run due to the time dependencies and accuracy of the data.