by Rie Gaku (St. Andrew’s University) and Soemon Takakuwa (Chuo University)
As presented at the 2017 Winter Simulation Conference
Abstract
Simulation models are proposed for modeling Shuttle Vehicle-type Mini-load storage and retrieval systems (SVM-AS/RSs). The SVM-AS/RS is a fast shuttle vehicle-type mini-load automated storage and retrieval system designed to provide for storage and sorting functions including inventory buffer before shipping, picking, assorting, palletizing, or merging. The systems considered in this study consist of lightweight shuttle vehicles installed on each level, storing and retrieving lifters, layer conveyors connecting lifters and shuttle vehicles, and incoming and outgoing aisle conveyors. To analyze its performance, simulation models are performed taking the relationships of the storage locations and load sequences into consideration. It is emphasized that AS/RS operations of the mini-load system can be confirmed by simulation experiments. In addition, the key performance indicators from the simulation analysis can be used to understand and validate its efficiency and effectiveness under different layouts.
Introduction
During the past two decades, the Business-to-Consumer e-commerce (BtoC-EC) market has become immense and is unprecedented. As varied forms of online marketing have been increasingly used by organizations, online marking is projected to have a major impact on both consumer behavior and logistics management. The sales figures of BtoC-EC recently soared to an annual total of 6.51 trillion yen, and its market scale has expanded for 17 consecutive years (Dentsusoken 2017). In the past decade, to enhance customers’ usability, the competition in fast shipping service based on specified delivery destinations and desired delivery times and dates has intensified in Japan’s e-commerce industry. Several suppliers, including Amazon Japan, Yodobashi, and Rakuten, have successfully provided faster delivery service within 3 hours after receipt of orders in their logistics operations to some areas of Japan to satisfy customers’ faster delivery service needs.
It should be emphasized that enhancing customers’ usability by shortening the lead time from the order of merchandise to final delivery to a user is an important element of supporting the competitiveness of e-commerce. In this environment, suppliers who do BtoC-EC business face many challenges in identifying which item should be retrieved, from which location, and how fast it should be shipped to customers to satisfy an online order.
Flexible storage and sorting response functions are required in logistics operations of e-commerce business to satisfy customers’ faster delivery service needs. Flexible storage and sorting functions include inventory buffers before shipping, picking, sorting, and palletizing or merging of cartons, totes, and trays by group or specified sequence. However, performance analysis of an automated storage and retrieval system (AS/RS) is a complex issue to logistics managers in an dynamic BtoC-EC environment.
Simulations have traditionally been used as a decision-making tool for logistics operations to ensure continuous operations are maintained. Many studies focus on simulation modeling for large-scale AS/RS operations. It has been necessary to model and perform simulation experiments so as to analyze and compare possible alternatives of an AS/RS (Takakuwa 1989; Takakuwa 1994; Takakuwa 1995). A cost- effectiveness optimization analysis of an actual looped-truck automated guided vehicle (AGV) system was performed using a simulation to develop policies and examine operational specifications (Takakuwa 1993). Takakuwa (1996) presented a module-based modeling method for generating simulation programs for complex and large-scale AS/RS-AGV systems.
Several studies described unit load AVS/RSs to design and analyze the performance of logistics operations. Hu et al. (2005) used simulation to validate the optimal design of a rectangular-in-time AS/RS rack taking the stay dwell point policy into consideration. A computationally efficient cycle time model for unit load AVS/RSs using autonomous vehicle technology was presented to estimate vehicle utilization where the objective was to specify the range of design profiles warranting more extensive simulation- based evaluation and validation (Kuo et al. 2007). Goozen et al. (2016) developed scheduling heuristics to assign tasks to shuttles with the goal of minimizing the number of out-of-sequence occurrences and maximizing the throughput capacity of a full roaming-shuttle system (FRS). The FRS has been deemed suitable for slow-moving products in retail and wholesale distribution centers. In this paper, a simulation model is proposed for modeling a fast Shuttle Vehicle-type Mini-load AS/RS system (SVM-AS/RS). The SVM-AS/RSs are designed to provide storage and sorting functions including inventory buffer before shipping, picking, assorting, palletizing, or merging to handle cartons, totes, and trays by group or a certain sequence. The simulation models differed from the above-mentioned studies because the simulation modeling was designed to specifically consider storage location and load sequence allocation. A novel solution for supporting fast mini-load AS/RS operations for an e-commerce business based on time units of hours and seconds is used as the means of confirming the effectiveness of the SVM-AS/RSs.
Shuttle Vehicle-Type Mini-Load AS/RS System
A general view of the SVM-AS/RSs is shown in Figure1. The SVM-AS/RSs considered in this study
consist of various subsystems including lightweight shuttle vehicles installed on every level, storing and retrieving lifters, layer conveyors connecting lifters and shuttle vehicles, and incoming and outgoing aisle conveyors. Storage and retrievals are performed to/from the racks by lightweight shuttle vehicles that can move only in horizontal direction. The racks are linked to the storing and retrieving lifters through the layer conveyors. Outgoing aisle conveyors are linked to the checking and packing area.
Operation Flow of SVM-AS/RSs
Every incoming mini-load is first moved onto an incoming aisle conveyor and then picked by a storing and retrieving lifter before being placed on a layer conveyor. Next, the mini-load is moved to its destination rack by a lightweight shuttle vehicle. Alternately, an outgoing mini-load is picked from its rack in the system by a lightweight shuttle vehicle, then transferred to the outgoing aisle conveyor through a layer conveyor, and finally onto a storing and retrieving lifter.
Lightweight shuttle vehicles as well as storing and retrieving lifters can be handled in accordance with operations priority and urgency. For retrieving operations, an urgent load comprised of a load of high-priority storage is given preferential treatment over low-priority loads. Similarly, if storage operations have a higher priority, then retrieving operations, storing using lightweight shuttle vehicles will have priority over retrievals; otherwise, the operations alternate between retrieval and storage operations cyclically.
In general, there are two picking methods in terms of schematic operation flows: the relay picking method and the parallel picking and palletizing method. There are not any arranging and sorting operations for processing the associated orders in the relay picking method. Hence, the relay picking method is considered to be more suitable for fast-moving products in BtoC-EC logistics environment. In this study, the SVM-AS/RSs adopt the relay picking method to perform storage and sorting functions before any required shipping, picking, assorting, palletizing, or merging operations.
Storage Locations Allocation Rules for Incoming and Outgoing Loads
To meet fast AS/RS service expectations based on time units of hours and seconds, storage-location allocation rules based on inbound and outbound frequency rates become an interesting challenge to resolve in logistics operations of e-commerce business. Two general storage-location allocation rules are considered in order to smooth AS/RS operations and to support fast and efficient operations of the SVM- AS/RSs.
The first rule is called the “Priority Allocation Rule” shown in Figure 3. In the event outgoing operations are concentrated around a certain time, the storage locations close to the layer conveyors are allocated and prioritized for the incoming loads to minimize the operation time of outgoing operations. Otherwise, storage locations are randomly assigned from the available locations among the various levels; this rule is called the “Random Allocation Rule Based on Level Balance.”
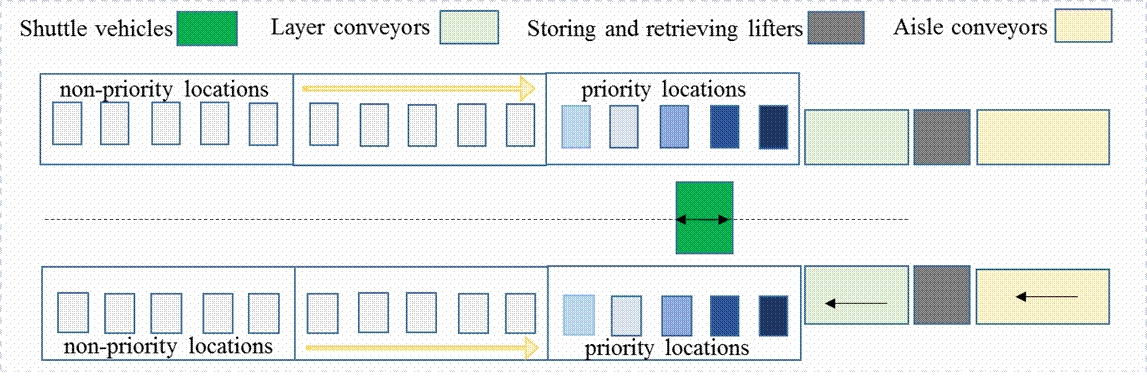
Procedures
Computer simulation is a method that can be used to describe, analyze, and predict the performance of a complex system without limiting assumptions. The objective of this study is to propose procedures that take the relationships of the storage locations and load sequences into consideration. As shown in Figure 4, the procedures to validate and improve the AS/RS operations of SVM-AS/RSs are detailed as follows:
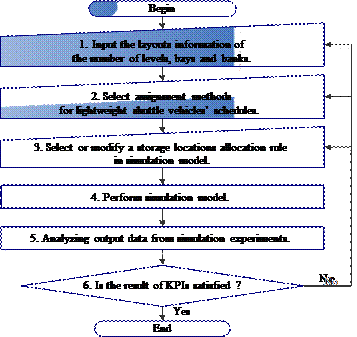
[Step 1] Collect and input the layout information including the number of levels, bays and banks, as described in Section 4.2.
[Step 2] Select assignment methods for the schedules of lightweight shuttle vehicles. [Step 3] Select or modify a storage-location allocation rule in the simulation model.
[Step 4] Perform a simulation model to observe the AS/RS operations of the SVM-AS/RSs. [Step 5] Obtain simulation results for simulation experiments.
[Step 6] If the result of KPIs from the simulation analysis is acceptable, terminate the procedure.
Otherwise, return to Step 1, 2 or 3 and adjust the data and parameters required for Step 4.
It is emphasized that the procedures proposed in this study can help logistics managers understand and validate AS/RS operations in a dynamic BtoC-EC environment, thereby confirming and improving the effectiveness of AS/RS operations that involve mini-loads under different layouts.
Application
The simulation model of AS/RS operations of SVM-AS/RSs was created using the Simio simulation package (Kelton, Smith, and Sturrock 2013). There are two essential types of material-flow processes typically that are performed in SVM-AS/RSs considered in this study, i.e., incoming and outgoing, as shown in Figure 5. Each process flow contains a sequence of activities performed by lightweight shuttle vehicles installed on every level, storing and retrieving lifters, layer conveyors, and incoming and outgoing aisle conveyors. All operating activities must be performed according to operations priority at Step 4. The essential process flows are identified so the materials handling operation flows of SVM- AS/RSs can be characterized.
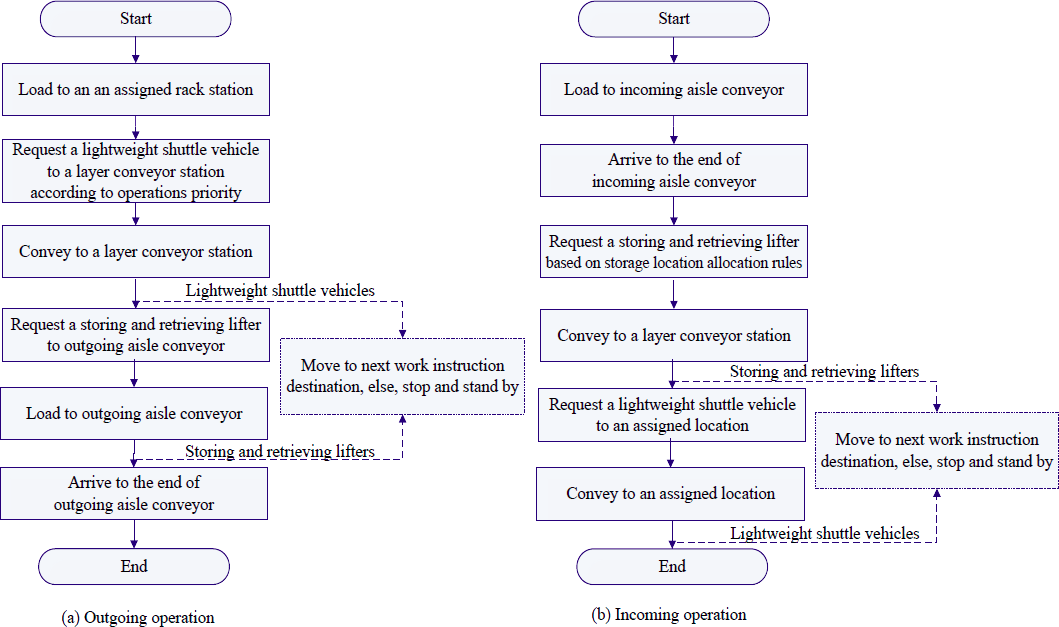
Parameters
Specifications of the system are defined as parameters, as shown in Table 1. As the parameters listed in Table 1 are used as the experimental conditions for the simulation model, all required parameters should be inputted into the model before performing the simulation model from Steps 1 to 3.
To illustrate the results of the simulation models at Step 1, three types of layouts for SVM-AS/RSs are considered. The numbers of the corresponding bank, bay, and level of the three types are as follows:
- Type 1: bank: 2, bay: 30, level: 6 = 360 (racks)
- Type 2: bank: 2, bay: 20, level: 6 = 240 (racks)
- Type 3: bank: 2, bay: 10, level: 6 = 120 (racks)
Table 1: Parameters of the SVM-AS/RSs.
Items |
Paramters |
Racks: |
360 ( = 2 × 6 × 30 ) |
Lightweight shuttle vehicles: |
6, 6, 6 (units) |
Velocity |
(16.88 m. / sec.) |
Loading time |
(5.76 sec./unit) |
Unloading time |
(3.51 sec./unit) |
Storing and retrieving lifters: |
|
Numbers of storing lifters |
1, 1, 1 (units) |
Numbers of retrieving lifters |
1, 1, 1 (units) |
Velocity |
(11.65 m. / sec.) |
Loading time |
(1.16 sec./unit) |
Unloading time |
(1.05 sec./unit) |
Layer conveyors |
6, 6, 6 (units) |
Velocity |
(14.71 m. / sec.) |
Aisle conveyors |
1, 1, 1 (units) |
Velocity |
(40m. / sec.) |
Length |
5 ( m. ) |
Items to be handled: |
900 (units/h.) |
Now, it is assumed that the same number of banks and levels are installed to execute simulation experiments for Type 1–3 at Step 1. A storing lifter and a retrieving lifter are sufficient in the case of two banks. The number of bays can be set to 30, 20, and 10, respectively.
For Step 2, the assignment methods for the schedules of lightweight shuttle vehicles are considered and illustrated. For the purposes of this study, each simulation experiment starts at the point of an incoming operation. When the retrieval instructions are assigned, then the operations alternate between retrieval and storage operations cyclically. For Step 3, the priority allocation rule is selected in the simulation model. For Step 4, the statistics are measured and recorded for the cyclical operations’ periods according to the selected storage-location allocation rule for incoming and outgoing loads. Thirty independent simulation runs are made for each storage-location allocation rules for each layout type.
Key Performance Indicator Comparison among Alternative Layout and Storage-Location Allocation Rules
When key performance indicator (KPI) comparisons are performed between alternative layout and storage-location allocation rules, it is necessary to collect the following output results by performing the simulation model:
- Average number of outgoing retrieving/incoming storing loads per hour.
- Utilization of lightweight shuttle vehicles and storing and retrieving lifters.
- Lead time for retrieving a load from time of retrieval instruction to the finish time of retrieving the load.
- Racks utilization per hour.
Using the abovementioned KPI, the measures of performance for the designated system layout, such as handling capacity and bottleneck analysis, can be analyzed.
Before performing simulation analysis, the maximum number of outgoing retrieving/incoming storing loads per hour, i.e., I (units), can be estimated using the following equation:
where:
a: one-way moving time of a storing/retrieving lifter from the base position to the halfway point (s)
b: loading time onto a lifter (s)
c: unloading time from a lifter (s)
n: number of shuttle vehicles (units)
T: operation time (e.g., 3,600 s)
x: one-way moving time of a shuttle vehicle from the base position to the halfway point (s)
y: loading time onto a shuttle vehicle (s)
z: unloading time from a shuttle vehicle (s)
The term (2a+b+c) in the denominator of Equation (1) is the expected time of one round-trip of a lifter. In addition, (2x+y+z) is the expected time of one round-trip of a shuttle vehicle, and n units of shuttle vehicles are used for conveying both outgoing retrieving/incoming storing loads. Accordingly, the expected overall processing time is ((2(2x+y+z))/n). Therefore, depending on the specification of the AS/RS system, the bottleneck of the system will be either a lifter or shuttle vehicle. In Equation(1), the associated times on both a lifter and a shuttle vehicle can be measured via time study. Selected sample data obtained via time study on Type 1 are shown in Table 2.
Table 2: Selected sample data obtained via time study (Type 1: bank: 2, bay: 30, level: 6).
Transporters |
Items |
Time (s) |
|
Lifter |
One-way moving time |
a |
1.03 |
Loading time onto a lifter |
b |
1.16 |
|
Unloading time from a lifter |
c |
1.05 |
|
Shuttle Vehicle |
One-way moving time |
x |
3.49 |
Loading time onto a shuttle vehicle |
y |
5.76 |
|
Unloading time from a shuttle vehicle |
z |
3.51 |
On the other hand, simulation is a powerful tool for analyzing the performance of a large-scale AS/RS regardless of how large or complicated the system is. In SVM-AS/RSs used in a BtoC-EC, priority parcels need to be located on racks near the retrieving lifters for quick retrieval. Therefore, in this study, parcels are preferentially assigned and put on racks near retrieving lifters inside the AS/RS.
By performing a simulation, the actual average number of retrieving and storing loads per hour reflects the ability of SVM-AS/RSs, as shown in Figure 6. The 95% confidential interval on the average of the maximum number of outgoing retrieving/incoming storing loads for each type is shown in Figure 6. For example, the averages of the maximum number of outgoing retrieving and incoming storing loads for Type 3 are 658 and 590 pieces, respectively. From Figure 6, Type 3 is the most efficient among the three types in terms of the average number of outgoing retrieving and incoming storing loads.
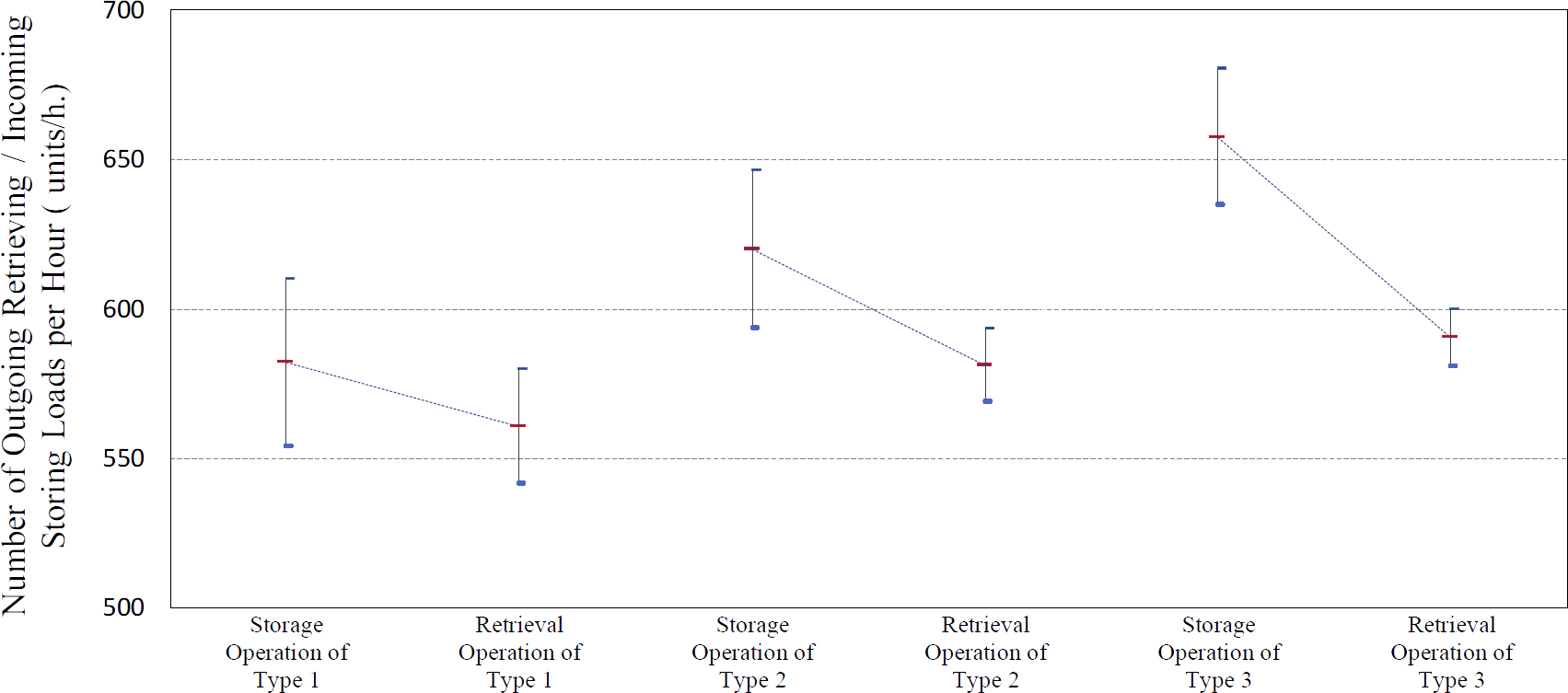
In addition, the 95% confidential interval on the average time between retrieving and storing loads for each type is shown in Figure 7. In Figure 7, it is observed that the average times between outgoing retrieving and incoming storing loads for Type 1, 2, and 3 are 116.81, 159.66, and 233.49 s, respectively. Type 1 is the shortest among the three types in terms of the average time between outgoing retrieving and incoming storing loads.
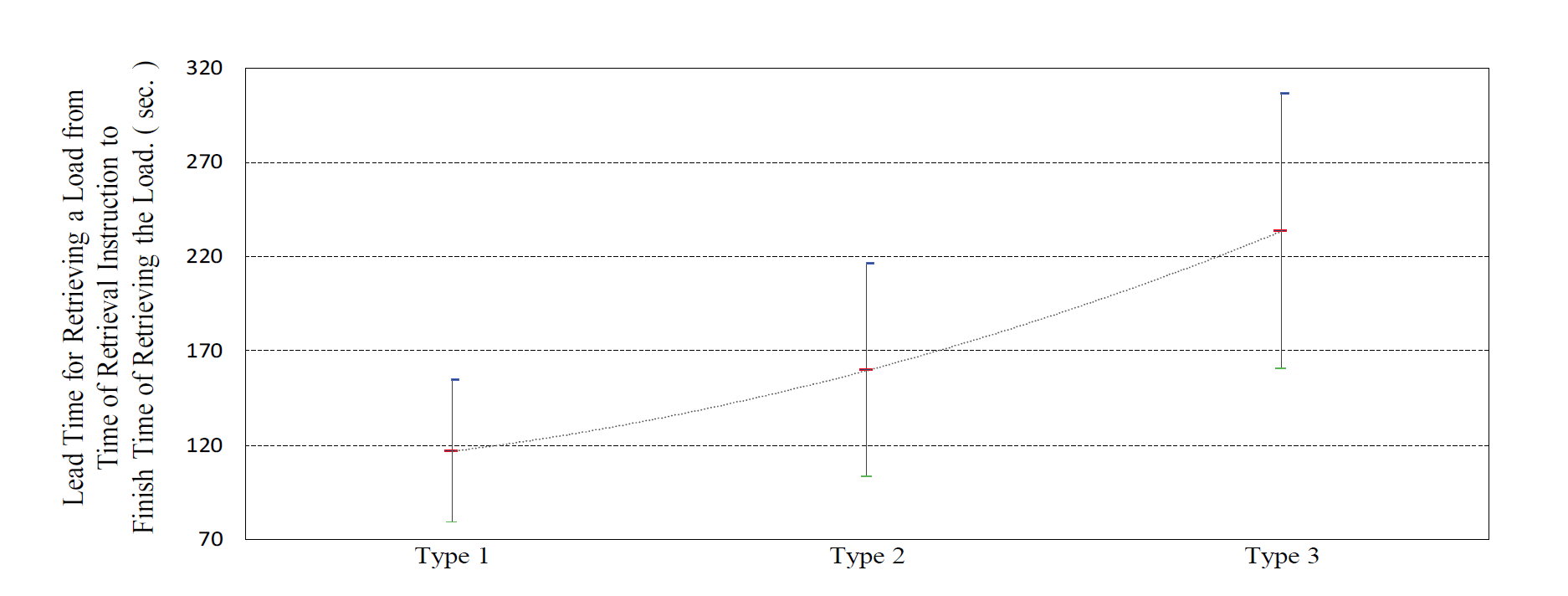
The results of lead time for retrieving a load from time of retrieval instruction to the finish time of retrieving the load is outputted, which can be used to examine both efficiency and effectiveness for any layout plan. The resulting lead times for retrieving a load from the time of the retrieval instruction to the finish time of retrieving the load, as obtained from the simulation, can be also used when considering methods for enhancing customers’ satisfaction by shortening the lead time from the order of merchandise to delivery to a customer. Therefore, the lead time is an important performance measure when evaluating the traceability of a delivery to a customer to improve the competitiveness of an e-commerce business.
From Equation (1), the maximum number of outgoing retrieving/incoming storing loads per hour for Type 1, 2, and 3 are 664.62, 623.92, and 588.56 s, respectively. The average time between outgoing
retrieving and incoming storing loads for Type 1, 2, and 3 are 5.42, 5.77, and 6.12 s, respectively. In addition, the bottlenecks of all types of layout are lightweight shuttle vehicles. Hence, it is found that Equation (1) is effective in estimating the general performance of SVM-AS/RSs.
Conclusion
- A simulation model of SVM-AS/RSs was constructed and used to analyze its performance while considering the relationship of the storage locations and load sequences.
- A systematic and flexible procedure for AS/RS operations of SVM-AS/RSs was described to validate and improve dynamic AS/RS operations under a BtoC-EC environment. The procedure and processes provide critical support for logistics managers by allowing for KPI comparisons between alternative allocation rules for layout and storage locations.
- The proposed procedure was applied to an actual case in which AS/RS operations were modeled. The results showed that the proposed procedure is both practical and powerful in assisting logistics managers with their efficient decision-making efforts under different layouts.
- A method to estimate the maximum number of outgoing retrieving/incoming storing loads per hour and find a bottleneck in the system was proposed before performing simulations to examine the detailed material handling operations.
ACKNOWLEDGMENTS
This research is supported by Grant-in-Aid for Young Scientists (B) of Japan Society for the Promotion of Science (JSPS) (Grant Number: 17K13801).